Researchers develop innovative battery recycling method
A research team at Rice University led by James Tour, the T.T. and W.F. Chao Professor of Chemistry and professor of materials science and nanoengineering, is tackling the environmental issue of efficiently recycling lithium ion batteries amid their increasing use.
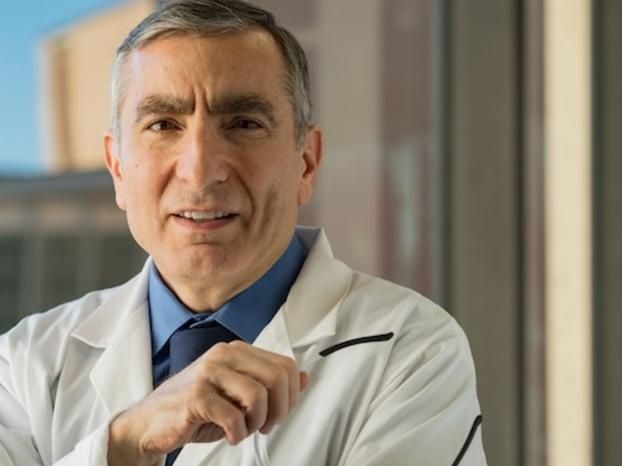
Rice researchers led by James Tour have developed an innovative battery recycling method.
Photo by Jeff Fitlow/Rice University
The team has pioneered a new method to extract purified active materials from battery waste as detailed in the journal Nature Communications on July 24. Their findings have the potential to facilitate the effective separation and recycling of valuable battery materials at a minimal fee, contributing to a greener production of electric vehicles (EVs).
“With the surge in battery use, particularly in EVs, the need for developing sustainable recycling methods is pressing,” Tour said.
Conventional recycling techniques typically involve breaking down battery materials into their elemental forms through energy-intensive thermal or chemical processes that are costly and have significant environmental impacts.
The team proposed that magnetic properties could facilitate the separation and purification of spent battery materials.
Their innovation uses a method known as solvent-free flash Joule heating (FJH). This technique devised by Tour involves passing a current through a moderately resistive material to rapidly heat and transform it into other substances.
Using FJH, the researchers heated battery waste to 2,500 Kelvin within seconds, creating unique features with magnetic shells and stable core structures. The magnetic separation allowed for efficient purification.
During the process, the cobalt-based battery cathodes — typically used in EVs and associated with high financial, environmental and social costs — unexpectedly showed magnetism in the outer spinel cobalt oxide layers, allowing for easy separation.
The researchers’ approach resulted in a high battery metal recovery yield of 98% with the value of battery structure maintained.
“Notably, the metal impurities were significantly reduced after separation while preserving the structure and functionality of the materials,” Tour said. “The bulk structure of battery materials remains stable and is ready to be reconstituted into new cathodes.”
Original publication
Weiyin Chen, Yi Cheng, Jinhang Chen, Ksenia V. Bets, Rodrigo V. Salvatierra, Chang Ge, John Tianci Li, Duy Xuan Luong, Carter Kittrell, Zicheng Wang, Emily A. McHugh, Guanhui Gao, Bing Deng, Yimo Han, Boris I. Yakobson, James M. Tour; "Nondestructive flash cathode recycling"; Nature Communications, Volume 15, 2024-7-24
Other news from the department science
These products might interest you
Most read news
More news from our other portals
See the theme worlds for related content
Topic World Battery Technology
The topic world Battery Technology combines relevant knowledge in a unique way. Here you will find everything about suppliers and their products, webinars, white papers, catalogs and brochures.
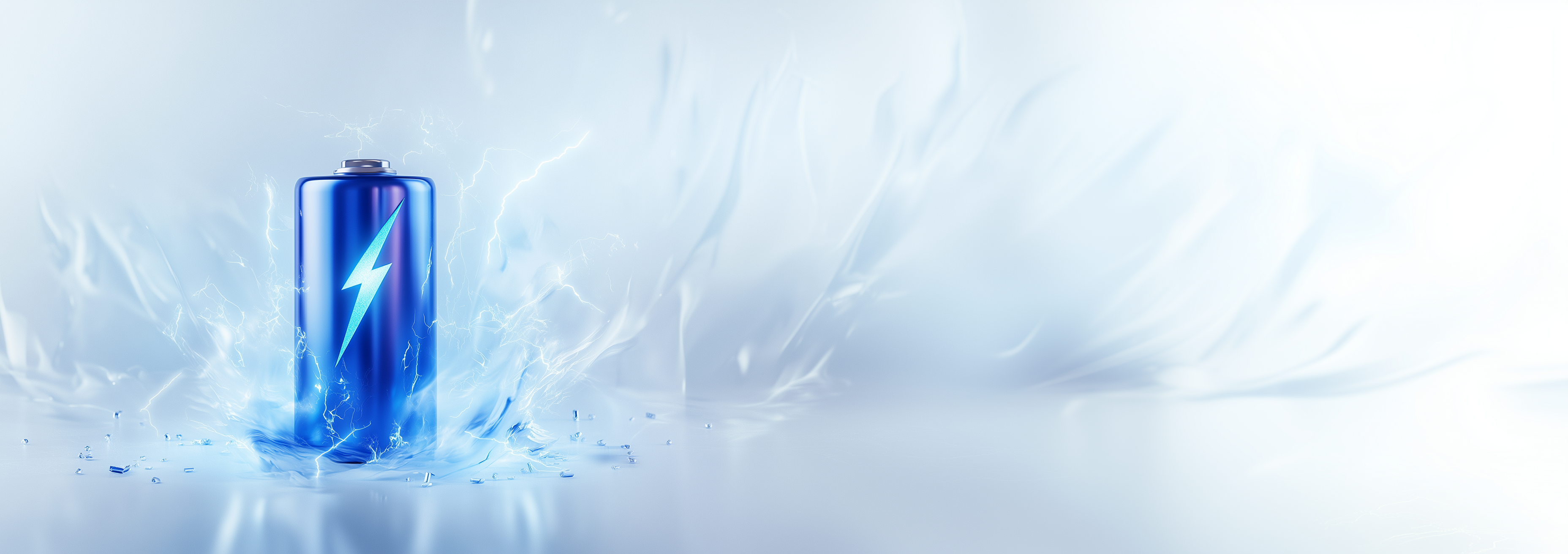
Topic World Battery Technology
The topic world Battery Technology combines relevant knowledge in a unique way. Here you will find everything about suppliers and their products, webinars, white papers, catalogs and brochures.