Developers of thin-film gas sensors benefit from heated substrate platform
Material characterization of metal oxides and organic materials
The Fraunhofer Institute for Photonic Microsystems IPMS develops and manufactures individual heatable test chips for the characterization of new gas sensor materials. Deposited sensing layers and their application-specific parameters, such as sensitivity and selectivity, can thus be specifically evaluated. Customized chip designs allow the optimal and highly accurate characterization of these thin films.
The detection of gases such as NO2, NH3, CO, H2S or volatile organic compounds (VOC) such as acetone, formaldehyde and methanol is of great importance for the assessment of potential health risks.
Gas sensors based on single-component metal oxides and carbon-based materials currently suffer from limitations such as low sensitivity in the lower ppm and ppb range as well as limited lifetime, which prevents their widespread use as high-performance gas sensors.
Therefore, further developments are needed to achieve electrical and thermal properties in combination with high sensitivity, fast response, high selectivity and fast repeatability.
In the context of such research, the characterization of sensitive layers plays a decisive role in order to be able to produce and use the materials in a targeted manner. Fraunhofer IPMS develops and produces conductivity and single transistor structures for the evaluation of novel materials. These substrates can be used, for example, to characterize the electrical properties of thin-film gas sensors. These substrates can also be used as a basis for further product developments.
"Gas sensors often need to be operated at defined temperatures. Our substrates make it possible to control the temperature of the layers, allowing materials to be studied easily and effectively. This includes studying stability and drift over different time periods. In addition, the behavior in processes can be investigated already during the deposition. We are looking for partners to further develop the technology and can also provide chips for measurements," explains Dr. Alexander Graf, Head of the Gas Sensors and Systems Group.
Advantages of Fraunhofer IPMS substrates
The chip substrates produced at Fraunhofer IPMS offer high-precision structures and high-performance materials, providing a promising basis for reproducible material evaluation in the context of R&D questions and qualification. The substrates offer different customized designs of the electrode structures, e.g. different channel widths and lengths on one chip, so that the ideal parameters can be used for specific applications.
The substrates are regularly fabricated in a clean room on silicon wafers with thermal silicon dioxide (SiO2), with other oxides such as hafnium dioxide (HfO2) available as dielectrics.
In sensor development, the sensitive materials determine the performance of the entire sensor. Material and process developers can apply semiconductor layers to the substrates by solution, chemical vapor deposition (CVD), or physical vapor deposition (PVD). Subsequent electrical characterization allows for characterization and evaluation based on conductivity, carrier mobility, and other performance parameters. As soon as a gas-sensitive material comes into contact with the analyte, this leads to a change in the electrical properties.
The substrates from Fraunhofer IPMS offer a simple way to record these changes. The sensor materials can be evaluated with respect to sensitivity and drift and then optimized, e.g. by adjusting the deposition parameters. Due to the wafer-level manufacturing technology, the substrates are also an interesting basis for product-oriented development. The test structures can be easily contacted and measured with the specially developed prober.
Most read news
Organizations
Other news from the department science
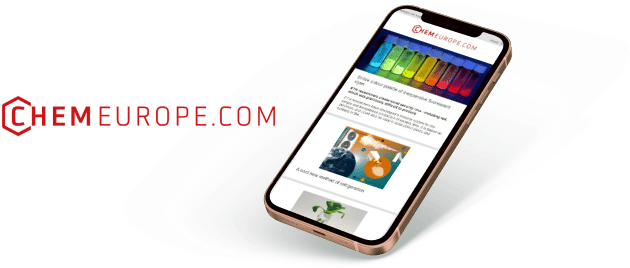
Get the chemical industry in your inbox
By submitting this form you agree that LUMITOS AG will send you the newsletter(s) selected above by email. Your data will not be passed on to third parties. Your data will be stored and processed in accordance with our data protection regulations. LUMITOS may contact you by email for the purpose of advertising or market and opinion surveys. You can revoke your consent at any time without giving reasons to LUMITOS AG, Ernst-Augustin-Str. 2, 12489 Berlin, Germany or by e-mail at revoke@lumitos.com with effect for the future. In addition, each email contains a link to unsubscribe from the corresponding newsletter.