Tests confirm quality of purified graphite from used lithium-ion batteries
Important step for the Circular Economy
lithium-ion batteries have become an integral part of everyday life. The number of used batteries is correspondingly high. They contain considerable amounts of important raw materials such as Graphite. recycling this mineral for being reused for new batteries with the same performance is an important goal. Researchers at the Helmholtz Institute Ulm and the Helmholtz Institute Freiberg for Resource Technology (HIF) at the Helmholtz-Zentrum Dresden-Rossendorf (HZDR) have now demonstrated that a graphite recycling technology is successful as intended. In tests, the purified graphite showed excellent capacity retention comparable to pristine commercial anode-grade graphite.
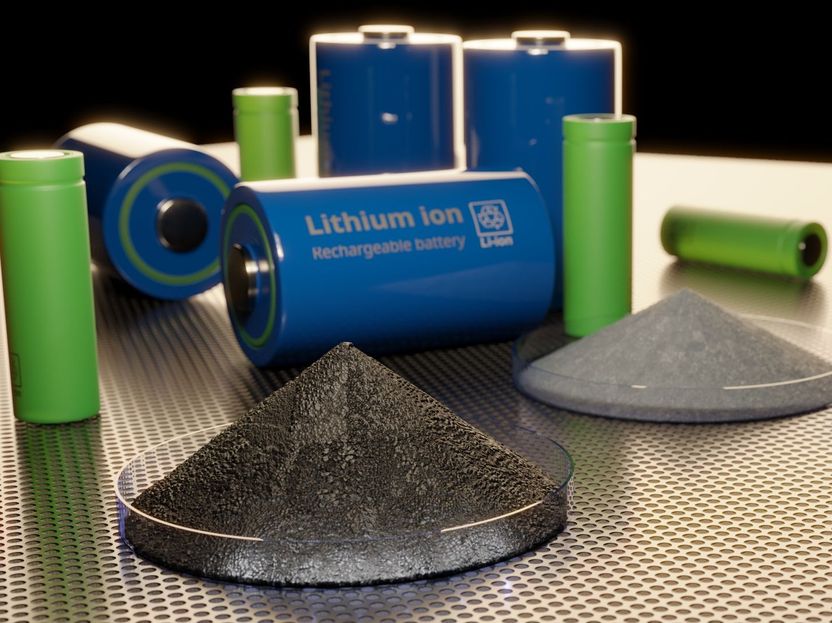
Lithium-ion batteries contain many important raw materials such as lithium, copper, nickel, cobalt, aluminum and graphite. The recycling of graphite is very important, as constituting approximately 15-25 percent of the battery´s weight.
Bernd Schröder
Lithium-ion batteries (LIBs) are contained in almost all of our electrical appliances and are an important energy supplier for e-mobility. However, various ageing processes reduce the performance of a battery over its usage period. LIBs contain many important raw materials. In addition to the lithium that gives them their name, they contain metals such as copper, nickel, cobalt, aluminum and graphite. The latter refers to the anode material, constituting approximately 15-25 percent of the battery's weight. The purer the graphite, the better this mechanism works. Synthetic graphite, i.e. graphite produced using an energy intensive coke-based process, fulfils this task particularly well thanks to its optimized and adaptable properties. However, both natural (i.e. mined from ores) and synthetic anode graphite come largely from China and have a significant environmental footprint. Recycling is therefore essential in order to recover the raw materials and at the same time minimize dependence on China. Currently, around 100,000 tons of used batteries are recycled in Europe every year.
Purification and reuse of graphite
To recover graphite from end-of-life batteries, these are first shredded, leaving behind what is known as black mass. The graphite is extracted from this fine powder using froth flotation. The process is based on the selective hydrophobization, i.e. water-repellent property, of minerals and the attachment of these particles to gas bubbles, which are subsequently recovered via a froth. The resulting concentrate is purified, often with inorganic acids such as hydrofluoric acid, which can also cause environmental damage. In this case, the Australian company EcoGraf cleaned the graphite particles using an environmentally friendly process that does not require highly toxic hydrofluoric acid.
Researchers from the Helmholtz Institutes in Ulm and Freiberg, examined the graphite particles with regard to purity and reuse as anode material. "With the tests we carried out we could prove that the electrochemical performance of the graphite recovered from discarded LIBs matches that of new anode graphite. Structure and morphology are insignificantly changed in comparison. Most importantly, the recycled graphite has a remarkable reversible specific capacity of more than 350 mAh/g despite minor impurities from the recycling process," says Dr. Anna Vanderbruggen, a scientist at the HIF at the time of the study, explaining the test results. Tests with newly assembled battery cells made from recycled graphite show excellent cycle stability. The test cell was subjected to 1,000 charging and discharging cycles, with a capacity retention of 80 percent. This is comparable to the performance of reference full-cells made of pure material.
Important step for the Circular Economy
The results are an important step towards meeting the requirements of the European Battery Regulation, which was only amended last year. It provides for an increase in the minimum recycling efficiency from 50 to 70 percent by 2030. As graphite accounts for up to 25 percent of the total mass of LIBs and will remain an essential component of LIBs in the near to medium future, this recycling process represents significant progress in aligning with the requirements of the European Green Deal and, above all, in advancing towards a circular economy.
Original publication
Other news from the department science
These products might interest you
Most read news
More news from our other portals
See the theme worlds for related content
Topic World Battery Technology
The topic world Battery Technology combines relevant knowledge in a unique way. Here you will find everything about suppliers and their products, webinars, white papers, catalogs and brochures.
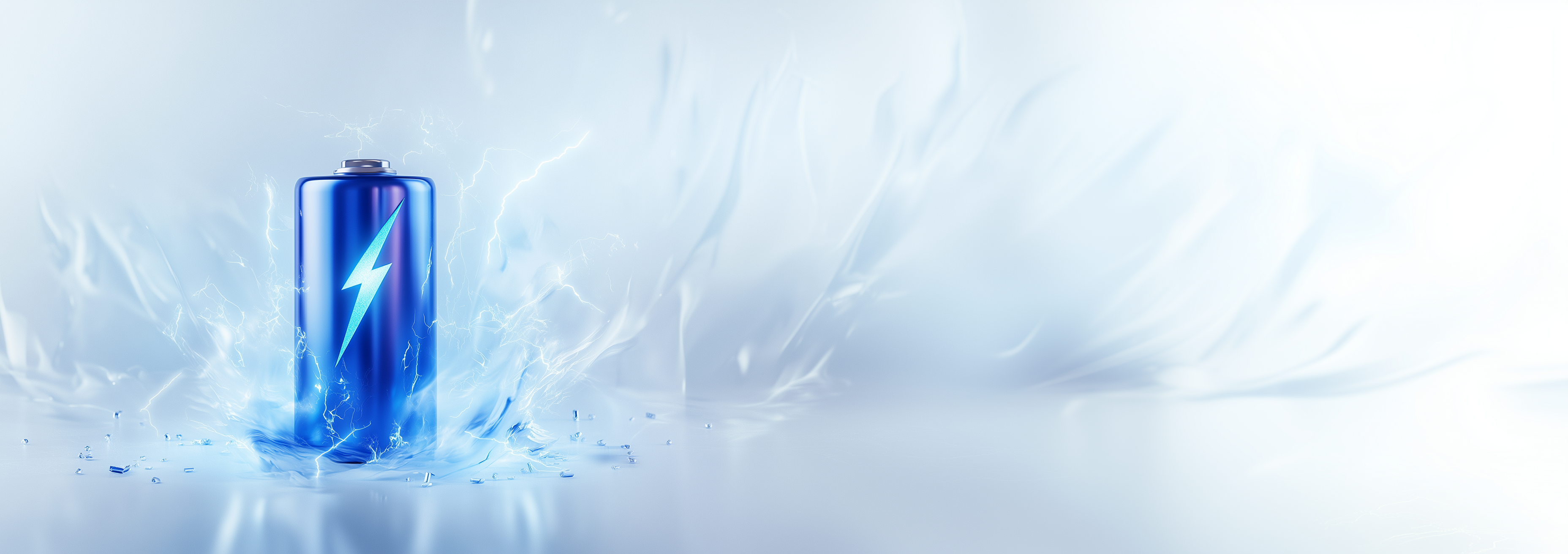
Topic World Battery Technology
The topic world Battery Technology combines relevant knowledge in a unique way. Here you will find everything about suppliers and their products, webinars, white papers, catalogs and brochures.