Faster charging with diamonds
Increasing the road performance and service life of electric cars and significantly reducing charging times
Diamond is known for its outstanding thermal conductivity. This makes the material ideal for cooling electronic components with high power densities, such as those used in processors, semiconductor lasers or electric vehicles. Researchers at Fraunhofer USA, an independent international affiliate of the Fraunhofer-Gesellschaft, have succeeded in developing wafer-thin nanomembranes from synthetic diamonds that can be integrated into electronic components, thereby reducing the local heat load by up to ten times. This helps to improve the road performance and service life of electric cars and significantly reduces battery charging time.
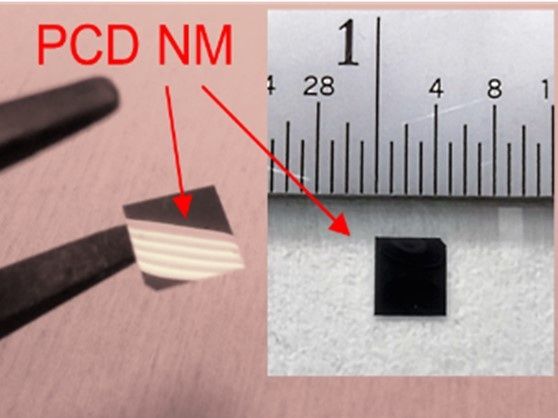
Photographs of freestanding polycrystalline diamond nanomembranes
© Fraunhofer USA, Center Midwest
An increase in power density and the resulting higher heat dissipation in electronic components require new materials. Diamond is known for its high thermal conductivity, which is four to five times higher than that of copper. For this reason, it is a particularly interesting material when it comes to cooling power electronics in electric transportation, photovoltaics or storage systems. Until now, heat sinks made of copper or aluminum plates have increased the heat-emitting surface of components that produce heat, thus preventing damage due to overheating. Scientists at Fraunhofer USA Inc., Center Midwest CMW in East Lansing in Michigan, an independent international affiliate of the Fraunhofer-Gesellschaft, have now developed nanomembranes from synthetic diamonds that are thinner than a human hair. The flexible material can be integrated directly into electronic components to cool the power electronics in electric vehicles, which transfer traction energy from the battery to the electric motor and convert the current from direct current to alternating current. The flexible, electrically insulating nanomembranes developed by Fraunhofer USA have the potential to reduce the local heat load of electronic components, such as current regulators in electric motors, by a factor of ten. The energy efficiency, service life and road performance of electric cars are improved significantly as a result. Another advantage is the fact that, when used in the charging infrastructure, the diamond membranes contribute to charging speeds that are five times higher.
Diamond membranes replace the insulating intermediate layer
Generally speaking, applying a copper layer underneath the component improves the heat flow. However, there is an electrically insulating oxide or nitride layer between the copper and the component, which has poor thermal conductivity. “We want to replace this intermediate layer with our diamond nanomembrane, which is extremely effective at transferring heat to the copper, as diamond can be processed into conductive paths,” says Dr. Matthias Mühle, head of the Diamond Technologies group at the Fraunhofer USA Center Midwest CMW. “As our membrane is flexible and free-standing, it can be positioned anywhere on the component or the copper or integrated directly into the cooling circuit.”
Mühle and his team achieve this by growing the polycrystalline diamond nanomembrane on a separate silicon wafer, then detaching it, turning it over and etching away the back of the diamond layer. This results in a free-standing, smooth diamond that can be heated at a low temperature of 80 degrees Celsius and subsequently attached to the component. “The heat treatment automatically bonds the micrometer-thick membrane to the electronic component. The diamond is then no longer free-standing but integrated into the system,” explains the researcher.
The nanomembrane can be produced on a wafer scale (4 inches and larger), making it well suited for industrial applications. A patent has already been filed for the development. Application tests with inverters and transformers in application fields such as electric transportation and telecommunications are due to start this year.
Other news from the department science
These products might interest you
Most read news
More news from our other portals
See the theme worlds for related content
Topic World Battery Technology
The topic world Battery Technology combines relevant knowledge in a unique way. Here you will find everything about suppliers and their products, webinars, white papers, catalogs and brochures.
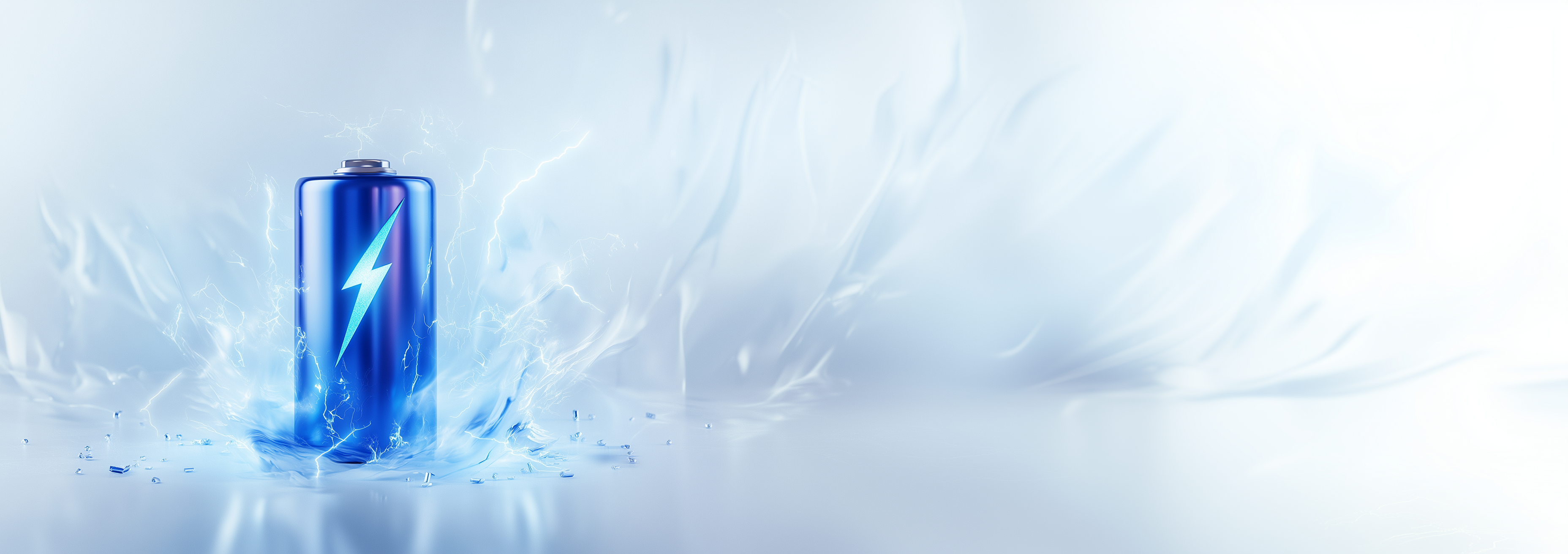
Topic World Battery Technology
The topic world Battery Technology combines relevant knowledge in a unique way. Here you will find everything about suppliers and their products, webinars, white papers, catalogs and brochures.