Industry 4.0: No impact on energy consumption?
To what extent does the digitalisation of industrial and manufacturing processes (Industry 4.0) improve energy efficiency and thus reduce energy intensity?
China accounts for 30% of global manufacturing value added and the largest share of global manufacturing and industrial output. There are widespread expectations that Industry 4.0 – the comprehensive digitalisation of industrial production processes – will simultaneously boost economic growth and achieve energy-savings targets. However, there is disagreement within the scientific community as to whether Industry 4.0 can in fact reconcile these two goals.
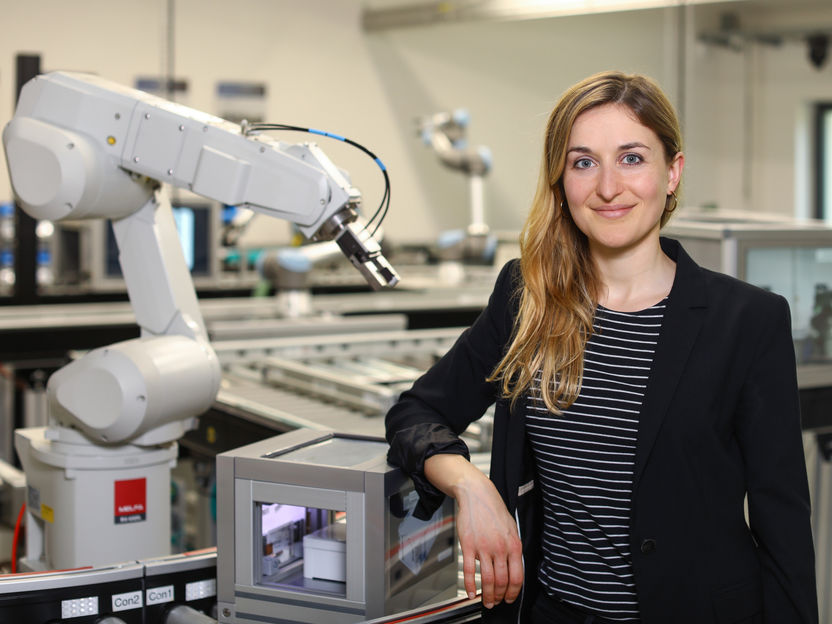
One conclusion of the RIFS study is that the often postulated mantra of "increasing energy efficiency through digitalization" is mostly ineffective for sustainability goals and the decarbonization of industry.
RIFS/ Kathleen Friedrich
A study by the Research Institute for Sustainability (RIFS) analysed ten Chinese manufacturing sectors between 2006 and 2019 with the aim of identifying correlations between Industry 4.0 and energy indicators. Although some studies have already analysed the impact of digital technologies on energy consumption, few have focussed on the Chinese context. “Moreover, previous studies did not properly address the concept of Industry 4.0," says lead author Stefanie Kunkel. “For example, some studies of Industry 4.0 in the Chinese context oversimplified the concept and equated the use of robots in manufacturing with artificial intelligence, for example. In doing so, these studies ignore the knowledge and innovation dimensions of Industry 4.0.” In addition, few of the previous studies examined aggregate energy consumption. Instead, most focused on relative energy consumption or energy efficiency. However, gains here can distract from the goal of reducing total energy consumption, which is vital for the decarbonization of the industrial sector.
Is there a significant link between industry 4.0 and energy consumption?
The main aim of the study is to understand the extent to which the uptake and degree of Industry 4.0 technologies impacts on overall energy consumption and energy intensity in the Chinese manufacturing sector – and whether the thesis that Industry 4.0 contributes to efficiency and thus energy savings is supported by statistical findings.
The term “energy intensity” measures the energy consumed within a given sector per euro of output. Kunkel and her co-authors conducted a panel data analysis that included data from ten industrial sectors over a period of 14 years (2006 to 2019). The manufacturing sectors covered included the textile industry, metal industry and the food industry, among others.
Digital rebound and growth versus efficiency effects
As far as total energy consumption in the manufacturing sector in China is concerned, the results show that there is no significant link between the degree of Industry 4.0 and energy consumption. "The relationship is positive, but not significant," comments Kunkel. For example, using robots instead of manual labour in textiles manufacturing, which is currently less digitalised, may likely increase energy consumption in that sector. So-called "digital rebound effects" often occur when efficiency gains achieved through digitalisation lead to cost savings. These savings can then be fully or partially reinvested, thus neutralizing some or all of the efficiency gains and thus expected resource savings. In addition, digitalisation generally has a growth-promoting effect, which is also likely to increase energy consumption.
The findings of Kunkel et al. contradict other studies, which found that the use of robots and industrial digitalisation reduced the energy intensity of industry and manufacturing – in other words, that they delivered efficiency gains. The RIFS study, on the other hand, was only able to identify a negative correlation between Industry 4.0 and energy intensity for sectors that are already highly digitalised. One explanation for this could be that Industry 4.0 innovations can be better integrated into strongly digitalised sectors, such as transport, enabling potential gains in efficiency to be realised to a greater degree.
One challenge for the analysis of the effect of industry 4.0 on energy indicators is that digitalisation-related offshoring and thus reductions in energy intensity may be attributed to digitalisation itself. In order to partially capture such effects, Kunkel et al. included the indicator "CO2 imports" as a proxy for the energy intensity of imported goods. There were significant positive associations between CO2 imports and the extent of Industry 4.0, which suggest that an increasing degree of Industry 4.0 is associated with increasing CO2 imports. However, further research is needed to understand the underlying dynamics.
Conclusion
Energy consumption in industry accounted for 37% of global energy consumption in 2022, with China accounting for the largest share. Reducing energy consumption and improving the environmental performance of industrial production in China will therefore be critical to efforts to mitigate climate change.
A key finding of this RIFS study is that focussing exclusively on potential gains in energy efficiency through digitalisation can undermine efforts to achieve sustainability goals and decarbonise industry as growth and offshoring dynamics driven by digitalisation may result in an overall increase in energy consumption. Other factors must be considered, such as impacts on industrial offshoring, the sector-specific impacts of different digital technologies, human capabilities to enable the absorption of innovations and harness their benefits for sustainability, as well as the simultaneous integration of renewable energy in industrial manufacturing.
In addition to energy variables, the Kunkel et al. also recommends including other sustainability indicators such as resource consumption and electronic waste from digital technologies in future studies on the sustainability of Industry 4.0. Such analyses of the relationship between energy and Industry 4.0 are of considerable relevance to industry representatives and political decision-makers beyond China. The European Union and countries around the world are hopeful that digitalisation can be harnessed in the pursuit of more sustainable development. This study shows that achieving this outcome is not a given, but that it will require careful steering.
Summary and recommendations
- Firstly, efforts should be undertaken through international cooperation and supply chain agreements to ensure that the adoption of Industry 4.0 innovations in the manufacturing industry reduces energy and resource demands along the entire value chain. This could help to prevent the increased offshoring of energy-intensive manufacturing processes to countries with lower environmental standards in the context of Industry 4.0.
- Secondly, further research is needed to improve understanding of the mechanisms and effects through which specific technologies affect energy consumption in industry and manufacturing. This would help to identify innovations in the field of Industry 4.0 with the capacity to reduce the overall environmental burden of industry and how policy and industry can support their uptake.
- Thirdly, the growth-accelerating effects of Industry 40 should be steered towards achieving sustainability targets such as decarbonization and the development of a circular ec