Dow and Evonik announce startup of hydrogen peroxide to propylene glycol (HPPG) pilot plant
Innovative technology offer flexibility, lower costs, and a smaller environmental footprint
Dow and Evonik are proud to announce the successful start-up and operation of a pioneering hydrogen peroxide to propylene glycol (HPPG) pilot plant at Evonik’s site in Hanau, Germany. Collaboratively developed by Dow and Evonik, the plant uses the distinct HYPROSYN® method to enable the direct synthesis of propylene glycol (PG) from hydrogen peroxide and propylene.
“At Dow, we believe in collaborating with our customers and other stakeholders to create, innovate and find solutions to big challenges. So, I am delighted to see this plant become operational through this collaboration,” said Andrew Jones, global business director for Chlor-Alkali Vinyl & Propylene Oxide, Propylene Glycol, at Dow. “With this innovative technology and flexible asset and business model, we are well positioned to meet our customers’ needs and growing market demand.”
“At Evonik Active Oxygens, we put sustainability at the core of futurizing our business. This relies not only on innovative technologies, but also the ability to scale these up and bring them to market,” remarked Michael Träxler, head of Evonik’s Active Oxygens business line. “That’s where excellent strategic partnerships come into play. The startup of this pilot plant in Hanau thus not only represents a major technological milestone in our efforts to make industry more sustainable, it is also a prime example of how cross-company collaboration, like this partnership with Dow, is essential to driving sustainable solutions.”
The pilot plant will demonstrate the benefits of the novel technology. In contrast to the traditional process, where propylene is used to make propylene oxide (PO), which is converted to PG through hydrolysis, the HYPROSYN® process uses a novel catalytic system to generate PG directly from propylene and hydrogen peroxide. The integration of all key reaction stages in a single reactor eliminates the need for additional investments in PO capacity and lowers capital requirements. The process also enables a reduced environmental footprint, e.g., water consumption is reduced to less than 5% compared to conventional PG methods. In addition, existing PG plants can be retrofitted to benefit from this new technology.
Propylene glycol serves as an essential ingredient such as a high-performing additive, intermediate, or initiator in a wide range of applications — including industrial, food and animal feed, pharmaceuticals, and cosmetics. Over the next few years, the Dow and Evonik teams will continuously evaluate the plant’s operations and capabilities to scale up manufacturing, in support of growing market demand.
Organizations
Other news from the department manufacturing
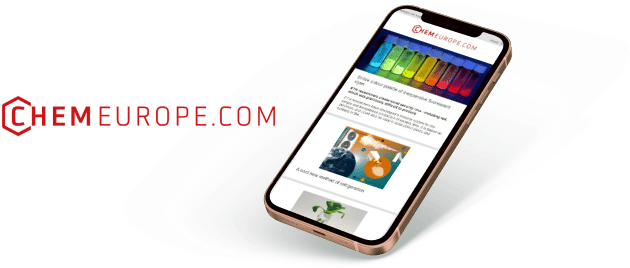
Get the chemical industry in your inbox
By submitting this form you agree that LUMITOS AG will send you the newsletter(s) selected above by email. Your data will not be passed on to third parties. Your data will be stored and processed in accordance with our data protection regulations. LUMITOS may contact you by email for the purpose of advertising or market and opinion surveys. You can revoke your consent at any time without giving reasons to LUMITOS AG, Ernst-Augustin-Str. 2, 12489 Berlin, Germany or by e-mail at revoke@lumitos.com with effect for the future. In addition, each email contains a link to unsubscribe from the corresponding newsletter.
Most read news
More news from our other portals
Last viewed contents
Evonik / BCD Chemie distribution agreement for Switzerland
Difficult year for the German chemical industry - Business developments 2015
Shedding light on the origin of chirality on Earth
Spanish salt venture opens new markets for AkzoNobel - New salt packing facility opens mediterranean market
Merck KGaA: Kley Elected Vice President of the German Chemical Industry Association
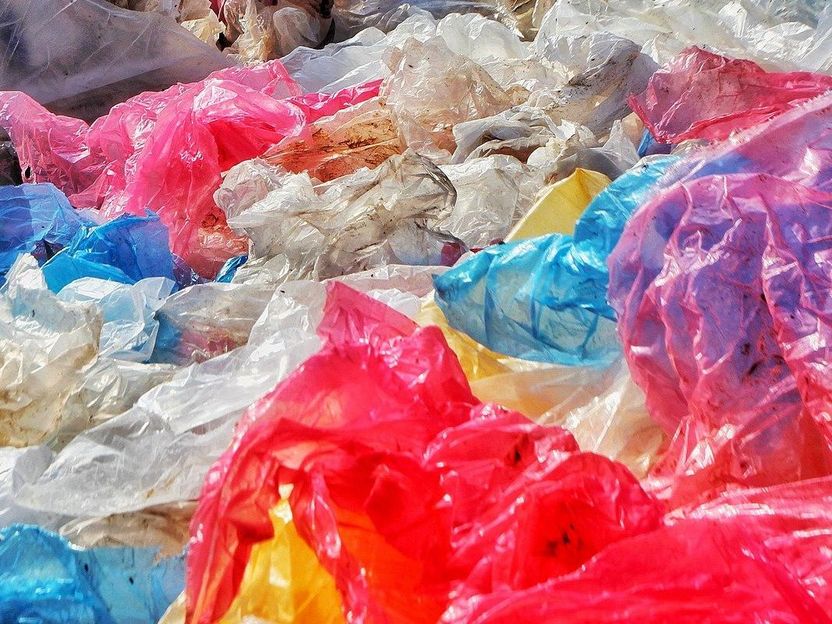