Fraunhofer IWS Installs Europe’s Unique Industrial 3D Printer
“SpreeTec next”: Powder Bed-Based Additive Laser Manufacturing System to Give New Impetus to Lusatia Region
The Fraunhofer Institute for Material and Beam Technology IWS in Dresden will install a Europe-wide unique industrial 3D printer. The Additive Manufacturing system from manufacturer Farsoon is based on selective laser beam melting in a powder bed. It can produce substantial components with complex geometries from aluminum, titanium, nickel, iron, copper, and other metallic powders layer by layer.
Fraunhofer IWS scientists are directing their research and development work with the manufacturing facility, such as combustion chambers for hydrogen energy systems, blade wheel enclosures for turbines, and other complex machine components or tools. With their help, together with the Brandenburg University of Technology Cottbus-Senftenberg (BTU) in the joint project “SpreeTec neXt”, they want to establish new manufacturing processes and value chains for the post-coal era in Lusatia, for instance. Entirely new business models for repairing spare parts that are difficult to obtain for agriculture, energy technology, or industry may also be foreseeable.
Unique Selling Propositions for Regional Small and Medium-Sized Businesses
“With such system technology, the East German SMEs can develop special unique selling propositions with the help of Fraunhofer IWS,” emphasizes institute director Prof. Christoph Leyens. “Especially in the transformation region of Lusatia, projects like ‘SpreeTec neXt’ give new impulses to the regional economy.” It is true that some companies already use 3D printers. However, these devices are usually limited in their capabilities. For example, they only specialize in plastic prototypes, can just produce comparatively small metallic components, or, although significant, tend to produce less complex shaped components using other manufacturing processes such as buildup welding. However, modern 3D printers like the one at Fraunhofer IWS reshuffle the cards: the new AM system can generate components that measure up to 62 by 62 by 110 centimeters.
“This system thus offers completely new possibilities to additively manufacture even huge components with complex geometry in high quality,” explains Dr. Lukas Stepien, who heads the Powder Bed Processes and Printing Group at Fraunhofer IWS. “Thus, it opens up application opportunities for industrial 3D printing in even more industries and applications.”
For example, decentralized Additive Manufacturing (AM) is conceivable where new components and tools for small batch sizes are permanently needed or replacement components are challenging to obtain—this interests automotive manufacturing, aerospace, the energy plant industry, and toolmaking, for instance. In the future, such large-scale AM systems may also facilitate the rapid procurement of spare parts for high-quality agricultural machinery in the agricultural sector.
Most read news
Organizations
Other news from the department research and development
These products might interest you
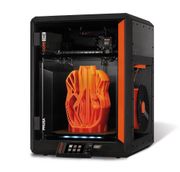
Filament-Drucker Prusa CORE One by Carl Roth
Prusa 3D printers – Advanced material versatility and flexibility
combines quality, reliability, and innovative technology with quiet high-speed printing
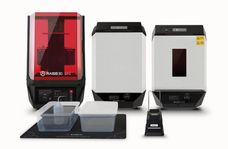
Resin-3D-Drucker Raise3D DF2 Komplett-Paket by Carl Roth
High-precision prints with fine details and smooth surfaces – ideal for prototyping
Specifically designed for the production of prototypes, manufacturing aids, and small series
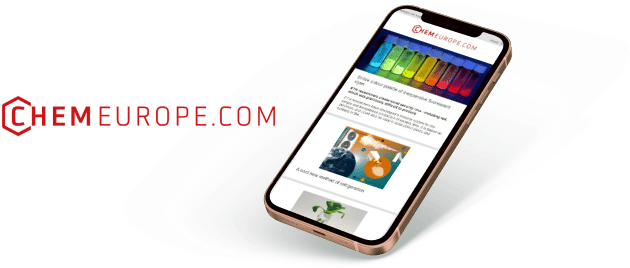
Get the chemical industry in your inbox
By submitting this form you agree that LUMITOS AG will send you the newsletter(s) selected above by email. Your data will not be passed on to third parties. Your data will be stored and processed in accordance with our data protection regulations. LUMITOS may contact you by email for the purpose of advertising or market and opinion surveys. You can revoke your consent at any time without giving reasons to LUMITOS AG, Ernst-Augustin-Str. 2, 12489 Berlin, Germany or by e-mail at revoke@lumitos.com with effect for the future. In addition, each email contains a link to unsubscribe from the corresponding newsletter.