When the Machine Reports Its Status
Even if the central concern of digitally integrated production or Industry 4.0 is networking industrial systems – the individual machine remains a central focus point of optimization. The reasons: Networking requires interfaces that must first be implemented on the individual machine. Fraunhofer IPK discussed the challenges facing machine builders in the development of intelligent mechatronic system technology with experts as part of a trend report.
Networked processes are based on data from individual systems. Machines – whether machine tools or robots – are being given more and more digital functions. With the help of electric drive technology, they become more flexible and can be retooled more quickly, for example. Integration of electronics also makes it possible to continuously monitor the status and behavior of systems and to map them in digital system twins. This way, production and environmental influences can be detected and corrected, and adjustments can be simulated in advance. This allows processes to be set up more efficiently than ever before. In addition, it is possible to intervene at an early stage, if a process is not running smoothly or if machine damage is imminent.
Sensors monitor machines and support their control
Sensors and network technologies integrated into machines are the basis needed for such functions. These components are becoming ever cheaper, especially in comparison to mechanics. The benefit is accurate monitoring of parameters such as temperatures, vibrations and energy consumption. Machine learning and artificial intelligence algorithms can learn from such data, for example, what the »normal state« of a machine looks like – and warn when deviations from the target occur or problematic trends emerge. As a consequence, smart and predictive maintenance can be carried out before a machine breaks down. This facilitates completely new maintenance concepts.
But also setting up machining processes and running them as best as possible benefits massively from intelligent data analysis based on sensor technology. Scarce or expensive resources such as energy can thus be used more economically and efficiently than before. And there is another aspect to be considered: When machines optimize their processes to a certain extent autonomously with the help of AI, quality is achieved with greater consistency. In addition, know-how can be transferred easily and securely to different locations, if it is encapsulated as an automated process within a system.
Hardware for digital functions must be durable
A prerequisite is careful selection of electronic components, because it is a problem for mechanical engineering that development cycles in the electronics sector are becoming shorter and shorter. Many electronic devices are developed with mass markets in mind, which want fast system changes in the interest of ever greater performance and capacity. Mechanical engineering needs greater consistency. Some companies now have enormous difficulties finding components that are available even for five years. The risk of an expensive machine tool coming to a standstill because a three-euro sensor fails or control software can no longer be updated is very real. This places immense demands on the flexibility of software and development. »From the point of view of the machine manufacturers, the goal must therefore be to find a good balance between the added value that can be achieved through digitalization and the associated expense,« says Prof. Dr.-Ing. Jörg Krüger, head of the Automation Technology division at Fraunhofer IPK. »Against this background, it is conceivable to keep electronic components in machines interchangeable. Retrofitting is also a viable option.«
New control methods make robotics universally applicable
When it comes to setting up manufacturing environments in such a way that they can be flexibly adapted to new tasks at any time, systems technology beyond the classic machine tool also becomes interesting. Robots have »learned« a lot in recent years: Thanks to modern force control and new solutions for human-robot cooperation, they have evolved into universal and even mobile processing and assembly machines. Robots become particularly flexible when humans can safely work with them in a confined space. Then the path guidance does not have to be programmed down to the last millimeter. Humans can fine-tune the robot movement manually – also using new concepts for programming, for example based on gestures. »Further developing intelligent human-robot interaction will shape the future, focusing on people and their strengths«, according to Jörg Krüger.
Other news from the department science
These products might interest you
Most read news
More news from our other portals
See the theme worlds for related content
Topic world Sensor technology
Sensor technology has revolutionized the chemical industry by providing accurate, timely and reliable data across a wide range of processes. From monitoring critical parameters in production lines to early detection of potential malfunctions or hazards, sensors are the silent sentinels that ensure quality, efficiency and safety.
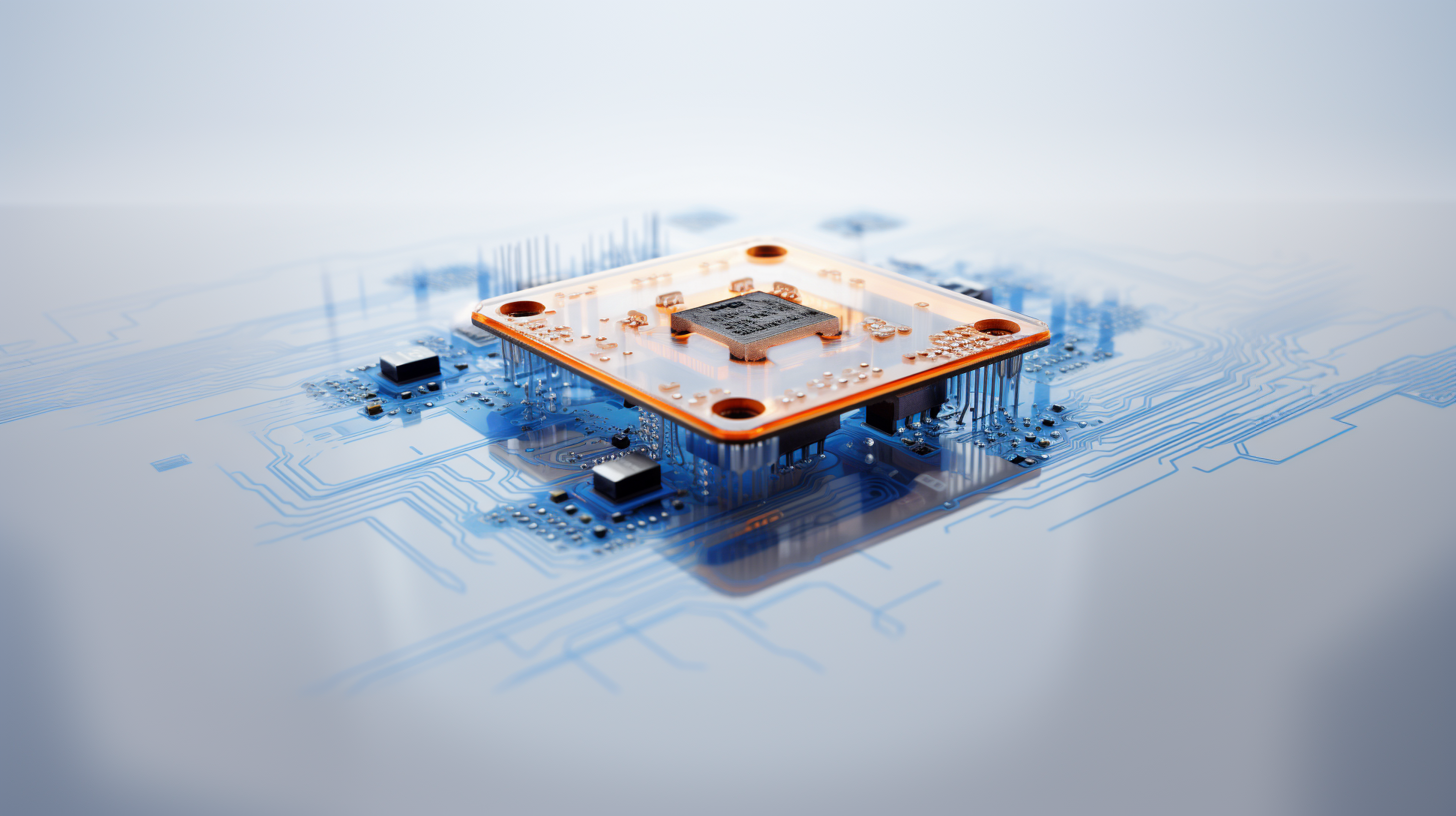
Topic world Sensor technology
Sensor technology has revolutionized the chemical industry by providing accurate, timely and reliable data across a wide range of processes. From monitoring critical parameters in production lines to early detection of potential malfunctions or hazards, sensors are the silent sentinels that ensure quality, efficiency and safety.