Using particle showers to scan the interior of structures
HZDR researchers seek to harness muon imaging for bridges, chemical parks, and Castor containers
Earth is constantly being struck by cosmic particles. High-energy muons can easily penetrate several meters of steel or concrete. A team at the Helmholtz-Zentrum Dresden-Rossendorf (HZDR) seeks to harness the potential of this unavoidable background radiation to view the interior of industrial facilities or structures. The problem is that muon detectors used in high-energy physics at research centers such as CERN are highly sensitive and expensive. This is why tomography experts at the HZDR are now developing a demonstrator – a low-cost, large-scale, and high-resolution muon detector for non-destructive condition monitoring. The Helmholtz Association is providing €500,000 in funding for the project over a period of two years as part of its transfer campaign. The project is set to start on July 1, 2023.
According to the Federal Highway Research Institute, one in ten bridges in Germany is dilapidated. Corrosive attacks on concrete reinforcement have a major impact, which is why bridges are checked regularly. Continuous monitoring of production facilities is also essential in the basic materials industry, incurring enormous costs. Distillation columns up to 50 meters high, large steel casting plants, and rotary kilns for waste incineration must be brought to a standstill, because this is the only way to detect signs of wear. And what about the condition of the spent fuel elements currently kept in storage casks at Germany’s 17 interim storage facilities?
“In theory, muon imaging is ideal for such applications,” emphasizes Professor Uwe Hampel, departmental head at the HZDR’s Institute of Fluid Dynamics. For example, it was in early March that the media again reported on a chamber discovered in 2017 in the 4,500-year-old Great Pyramid of Giza. What is a sensation for archaeologists owes much to muon imaging.
Muons are a component of cosmic rays. The charged particles are extremely energetic and penetrate deep into materials. This is why high-resolution detectors can be used to obtain three-dimensional images of the interior of large industrial facilities and structures.
“However, existing detector types are not sufficiently robust for monitoring, and are far too expensive,” explained the expert in imaging techniques in energy and process engineering. The cost drivers are complex manufacturing on the one hand, and the number of electronic channels required for high-resolution images on the other.
Clever adaptation to obtain inexpensive and robust detectors
It is hoped that new ideas will now help muon imaging achieve a breakthrough: One such idea is a detector concept with a special matrix structure for the electronics, which Hampel’s team originally designed for a patented wire-mesh sensor.
“Our structure is characterized by the ability to locate and transmit signals in the area with high efficiency, and then evaluate them using algorithms developed in-house. We have already managed to transfer this scheme to muon detectors,” Uwe Hampel reported.
In principle, the matrix structure is suitable not only for the wire electrodes of a gas ionization detector, but also for the optical fibers of a scintillation detector. Yet another advantage: Thanks to the sophisticated addressing scheme, both the number of electronics channels and the detector costs can be drastically reduced.
In the MYTOS project, which has received €500,000 in funding, experts at the HZDR are taking on the task of comparatively analyzing different detector principles. “We are particularly interested in whether the test detectors prove to be robust in an industrial environment, i.e. in the event of temperature fluctuations or vibrations,” Uwe Hampel explained.
Armed with the knowledge gained, he and his team of experienced measurement engineers and scientists plan to build a prototype and test it experimentally in collaboration with potential users. Also on board are BASF, EWN Entsorgungswerk für Nuklearanlagen [EWN Nuclear Waste Disposal Plant], and the Bundesanstalt für Materialforschung und -prüfung [Federal Institute for Materials Research and Testing, BAM].
As yet, the idea is limited to inspecting plants and structures using modular, mobile detectors at regular intervals. But Uwe Hampel is pursuing a clear vision: “In the long term, we want to reduce the cost of sensors and measurement technology to such an extent that stationary long-term monitoring becomes feasible.”
Organizations
Other news from the department science
These products might interest you
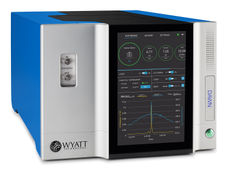
DAWN® by Wyatt Technology
The instrument for Multi-Angle Light Scattering (MALS): The DAWN® from Wyatt Technology
The world's most advanced light scattering instrument for absolute characterization of macromolecules
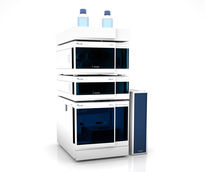
AZURA Analytical HPLC by KNAUER
Maximize your analytical efficiency with customized HPLC system solutions
Let your application define your analytical system solution
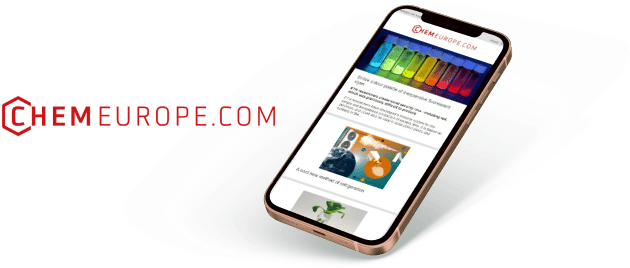
Get the chemical industry in your inbox
By submitting this form you agree that LUMITOS AG will send you the newsletter(s) selected above by email. Your data will not be passed on to third parties. Your data will be stored and processed in accordance with our data protection regulations. LUMITOS may contact you by email for the purpose of advertising or market and opinion surveys. You can revoke your consent at any time without giving reasons to LUMITOS AG, Ernst-Augustin-Str. 2, 12489 Berlin, Germany or by e-mail at revoke@lumitos.com with effect for the future. In addition, each email contains a link to unsubscribe from the corresponding newsletter.
Most read news
More news from our other portals
Last viewed contents
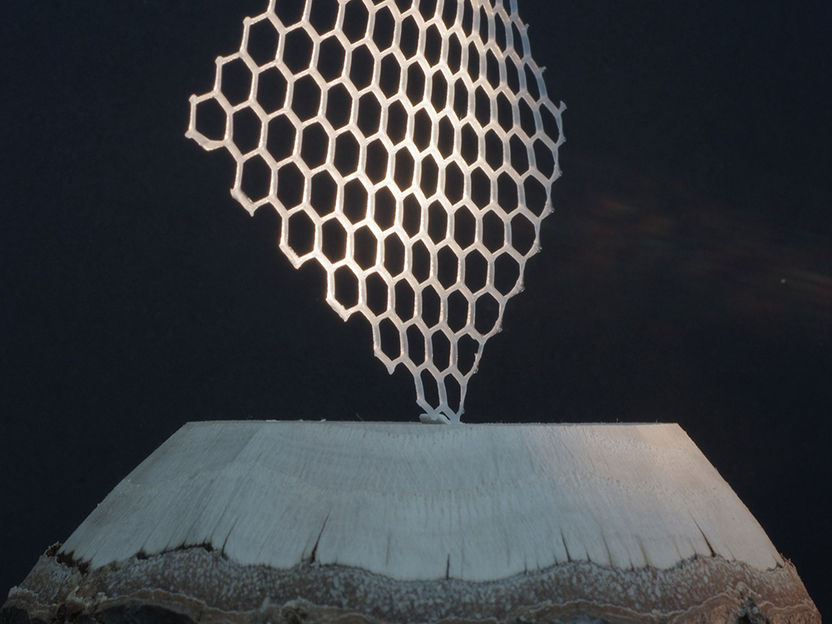
Printing complex cellulose-based objects
TERT
ATC_code_V01
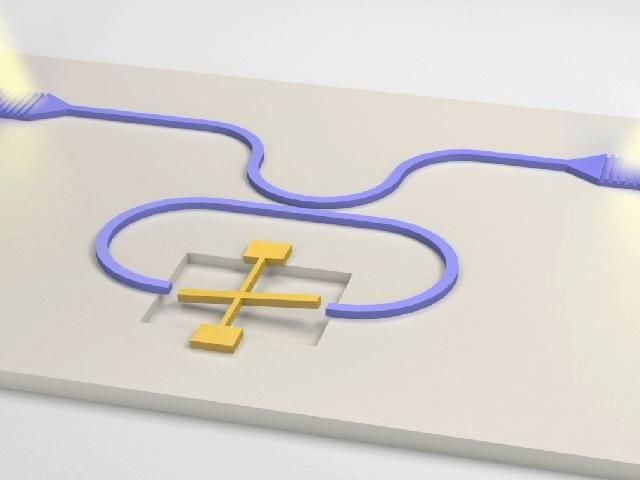
Sensing with a twist: A new kind of optical nanosensor uses torque for signal processing
Polyhedral_skeletal_electron_pair_theory
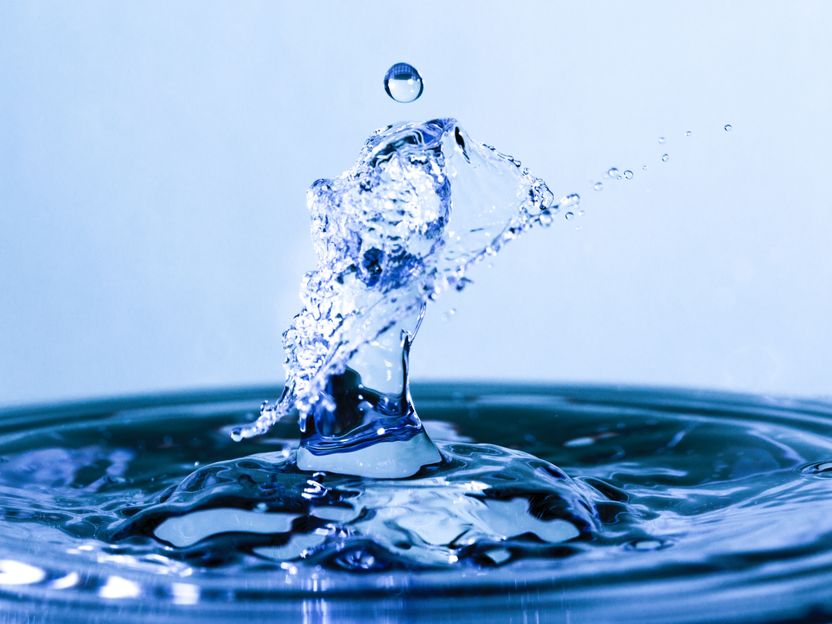
Designing better water filters with AI - Study demonstrates AI’s usefulness toward developing water purification membranes with novel properties

Controlling electron spin makes water splitting more efficient
Warm_filter
Ice_pack
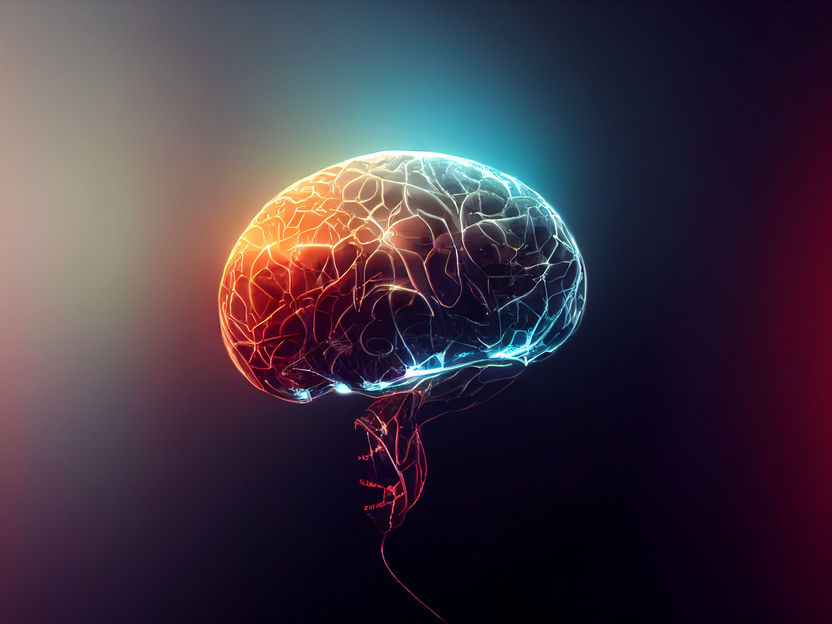