WACKER Confers Innovation Award for Optimized Polysilicon Manufacturing Process
Munich-based chemical group WACKER has given this year’s Alexander Wacker Innovation Award to a project team from Burghausen. The award was conferred for improvements to the polysilicon manufacturing process that further increase production efficiency. Paul Bönisch, Markus Wenzeis and their team succeeded in optimizing the control system such that the parameters for polysilicon deposition can now be adjusted in real time. The flexible modification to the process conditions enables optimized growth of the polysilicon rods. The €10,000 prize was awarded last Friday during the WACKER Innovation Days at the company’s Burghausen site.
WACKER produces polysilicon using the so-called “Siemens process,” which involves feeding gaseous trichlorosilane into reactors at a temperature of about 1,000 °C, at which point ultrapure polysilicon deposits onto seed rods. After several days, when the rods have grown to the desired diameter, the reactors are shut down and opened, and the polysilicon rods are removed and broken into smaller pieces. These then undergo an additional, complex cleaning process for semiconductor applications. Finished and packaged, the polysilicon pieces go to the customers – manufacturers of semiconductor and solar wafers all over the world.
Until now, the deposition process has been controlled according to conventionally set parameters. Using a newly developed sensor-based setup, Paul Bönisch, Markus Wenzeis and their team have been able to optimize the programming of the process control system via the detailed analysis of extensively collected data. This means that adjustments to the reactor conditions are now possible in real time. The efficiency of the entire process can be improved, and the quality of the end product further stabilized. The production process also becomes considerably more sustainable. “With this pioneering approach, we are strengthening our position as technology and market leader in the production of ultrapure polysilicon. At the same time, the new process makes an important contribution to achieving our CO2 reduction targets,” said WACKER Executive Board member Angela Wörl in her opening speech.
Thanks to their innovative approach to the optimization of polysilicon manufacturing, the Burghausen-based team managed to prevail against strong competition. This year, 24 teams from China, Germany, South Korea, the Czech Republic and the USA participated in the competition for the Innovation Award.
Most read news
Other news from the department manufacturing
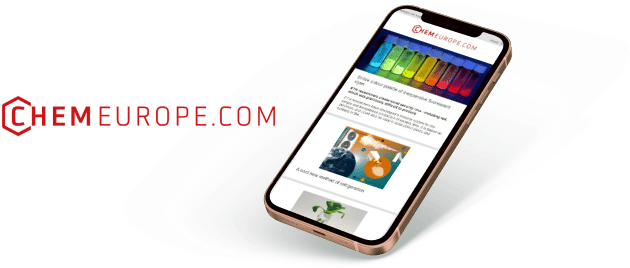
Get the chemical industry in your inbox
By submitting this form you agree that LUMITOS AG will send you the newsletter(s) selected above by email. Your data will not be passed on to third parties. Your data will be stored and processed in accordance with our data protection regulations. LUMITOS may contact you by email for the purpose of advertising or market and opinion surveys. You can revoke your consent at any time without giving reasons to LUMITOS AG, Ernst-Augustin-Str. 2, 12489 Berlin, Germany or by e-mail at revoke@lumitos.com with effect for the future. In addition, each email contains a link to unsubscribe from the corresponding newsletter.