Green gold: Torrefied biomass to replace coal and oil
Start-up enables green chemicals from wood and hay
In February, the Estonian-based startup New Standard Oil successfully commissioned their first industrial-scale prototype for drying and torrefaction of biogenic feedstock operating with superheated steam at atmospheric pressure. The energy-efficient process was developed at the Fraunhofer Institute for Interfacial Engineering and Biotechnology IGB in Stuttgart, Germany, and produces valuable raw materials for the chemical and energy industries: basic chemicals, biocoal and water.
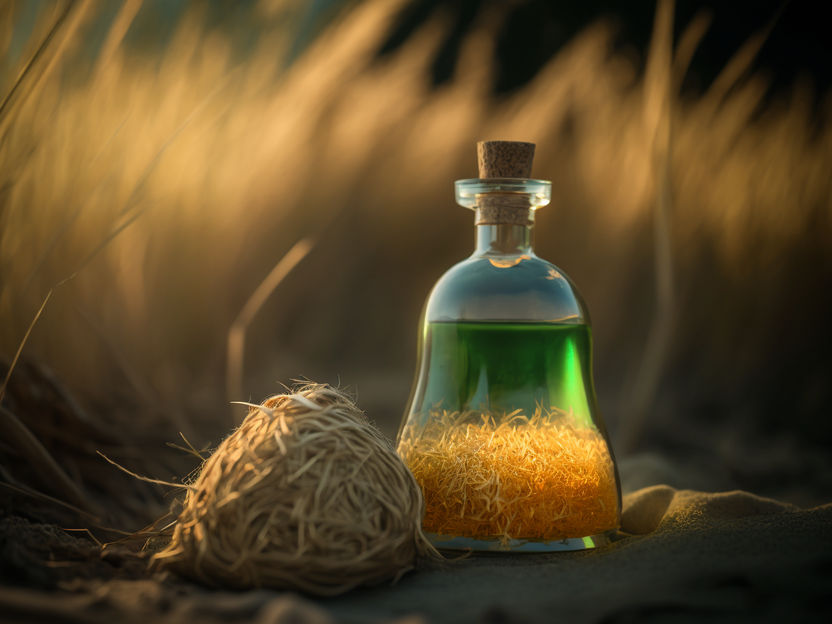
Symbolic image
Computer-generated image
Plant biomass is considered a climate-friendly alternative to fossil raw materials. For material and chemical use, renewable raw materials and residual material streams from agriculture and forestry or downstream industries are in many cases converted via biotechnological or chemical conversion processes into special chemicals, such as sugars or polymer building blocks.
A different approach, which allows biomass to be used completely in a single process, is being pursued by the startup New Standard Oil from Estonia: It relies on the thermal refinement and fractionation of biogenic residues such as wood and hay in order to convert them into “green” chemicals and “green” coal without leaving any residues. This is made possible by a process developed at the Fraunhofer Institute for Interfacial Engineering and Biotechnology IGB in Stuttgart, Germany, up to pilot scale, in which biomass is heated in a closed atmosphere of superheated steam without oxygen and thereby torrefied, i.e. thermochemically degraded.
Torrefaction provides green chemicals and green coal
“We have been working with New Standard Oil over the past few years and are looking forward to partnering with the Estonian startup company as a global licensee for our know-how in value-added torrefaction of biomass with superheated steam at atmospheric pressure and valorization of the chemicals,” says Dr.-Ing. Antoine Dalibard of Fraunhofer IGB.
The torrefaction process works similarly to mild pyrolysis and follows a drying step in which the water bound in the biomass evaporates. “In the same plant, at temperatures between 200 and 300 degrees Celsius, we then expel the volatile substances in the biomass, which originate primarily from hemicellulose, one of the three main components of biomass,” explains the thermal separation technology expert.
One of the key advantages of the process arises from the special design of the superheated steam drying system. “In addition to evaporated water, the gas phase also contains valuable volatile compounds. By cooling down the gaseous phase, we obtain a condensate that we can separate into various platform chemicals using subsequent separation processes such as distillation, extraction or electrodialysis,” Dalibard explains. The engineer has further developed and scaled up the process at Fraunhofer IGB and also investigated possible downstream processes for adding value to the chemicals condensed.
What remains as a solid is the torrefied biomass, which can be seen as biocoal. Compared to untreated biomass, its carbon content and thus its specific calorific value is significantly increased. Milled into powder or compressed into pellets, the “green” coal can be used, for example, for climate-neutral firing of power plants and replace fossil coal or gas.
Large-scale prototype for a zero-emission energy and carbon economy
“Faced with energy prices rallying and energy security at an all-time low, we have invested in this process aiming to make a local clean and carbon-neutral energy supply a reality with our ‘Uniformer®’ technology, as we named it,” says Sven Papp, one of the four co-founders of New Standard Oil. In February 2023, the startup launched its first industrial-scale prototype in Paldiski, Estonia, to convert fast-growing biomass and various low-quality biomass mixtures into water, green chemicals and biocoal in the established cascade process of drying and torrefaction. The young company even plans to use the waste heat arising in the process for feeding into the heating network.
“Our Uniformer® prototype can process up to 150 kilograms of biomass per hour and is already producing 100 percent marketable products from woodchips and non-feed hay: biocoal as a solid brown coal-level biofuel, renewable chemicals such as methanol, furfurals and other chemicals, furthermore desalinated water as well as the process heat”, Sven Papp confirms the Fraunhofer IGB results.
Biocoal can replace wood pellets or gas for combined heat and power (CHP) generation. A plus for energy security and grid stability: Electricity from CHP systems is dispatchable and can be generated on demand at night or during calm periods when the sun and wind fail to deliver sufficiently. “With the help of this new innovative approach we calculate that prices for dispatchable renewable electricity from biocoal could even be lower than that of land-based wind power”, Papp continues. The founders are optimistic and are meanwhile preparing to commercialize their first Uniformer® plants for the European market.
Other news from the department research and development
Most read news
More news from our other portals
Something is happening in the chemical industry ...
This is what true pioneering spirit looks like: Plenty of innovative start-ups are bringing fresh ideas, lifeblood and entrepreneurial spirit to change tomorrow's world for the better. Immerse yourself in the world of these young companies and take the opportunity to get in touch with the founders.