A newly developed catalyst makes single-use plastics easier to upcycle, recycle, and biodegrade
Revolutionary breakthrough: The catalyst transforms motor oil, plastic and natural gas into sustainable materials
Researchers created a new catalyst that transforms hydrocarbons into chemicals and materials that are higher value, easier to recycle, and biodegrade in the environment. This catalyst transforms materials such as motor oil, plastics in single-use grocery bags, water or milk bottles, and their caps, and even natural gas. It was developed by a team of scientists led by Aaron Sadow, a scientist at Ames National Laboratory, director of the Institute for Cooperative Upcycling of Plastic (iCOUP), and professor of chemistry at Iowa State University.
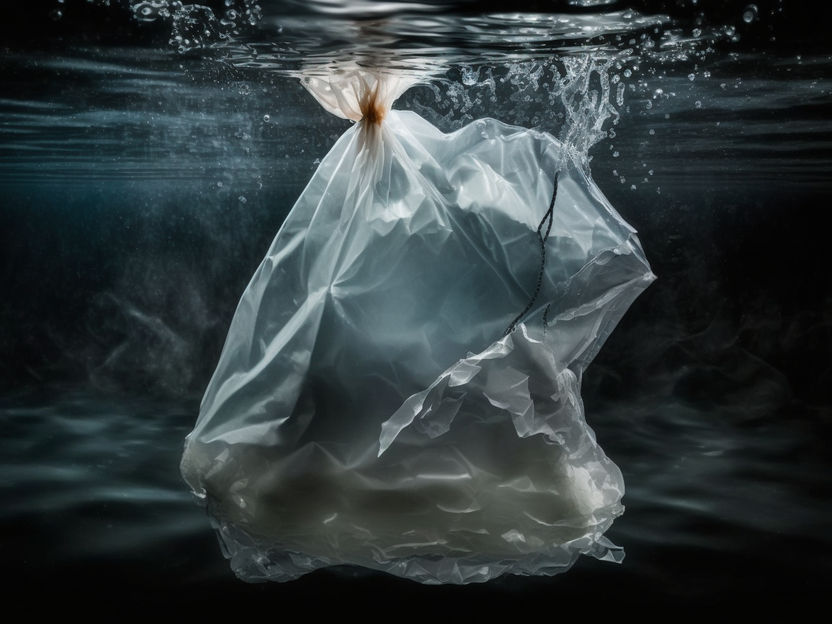
Plastic bag in water (symbolic image)
Computer-generated image
The new catalyst is designed to introduce functional groups into aliphatic hydrocarbons. Aliphatic hydrocarbons are organic compounds made up of only hydrogen and carbon. They typically do not mix with water, instead creating distinct layers, partly because they do not contain functional groups. Functional groups are specific groupings of atoms within molecules that have unique characteristics. Adding functional groups to these hydrocarbon chains can drastically affect their properties and make the materials recyclable.
“Methane in natural gas is the simplest of hydrocarbons with nothing but carbon-hydrogen (CH) bonds. Oils and polymers have chains of carbon atoms, linked by carbon-carbon (CC) bonds,” Sadow explained.
Aliphatic hydrocarbons make up a lot of petroleum and refined petroleum products, such as plastics and motor oils. These materials “don’t have other functional groups, which means they are not easy to biodegrade,” Sadow said. “So, it has long been a goal in the field of catalysis to be able to take these kinds of materials and add other atoms, such as oxygen, or build new structures from these simple chemicals.”
Unfortunately, the conventional way to add atoms to hydrocarbon chains requires considerable energy inputs. First petroleum is “cracked” with heat and pressure into small building blocks. Next, those building blocks are used to grow chains. Finally the desired atoms are added at the end of the chains. In this new approach, existing aliphatic hydrocarbons are converted directly without cracking and at low temperature.
Sadow’s team previously used a catalyst to break the CC bonds in these hydrocarbon chains and simultaneously attached aluminum to the ends of the smaller chains. Next, they inserted oxygen or other atoms to introduce functional groups. To develop a complementary process, the team found a way to avoid the CC bond breaking step. “Depending on the starting material’s chain length and the desired properties of the product, we might want to shorten chains or simply add the oxygen functional group,” Sadow said. “If we could avoid the CC cleavage, we could, in principle, just transfer the chains from the catalyst to aluminum and then add air to install the functional group.”
Sadow explained that the catalyst is synthesized by attaching a commercially available zirconium compound onto commercially available silica-alumina. The substances are all earth-abundant and inexpensive, which is beneficial for potential future commercial applications.
Additionally, the catalyst and reactant are advantageous in terms of sustainability and cost. Aluminum is the most abundant metal on earth, and the aluminum reactant used is synthesized without creating waste by-products. The zirconium alkoxide-based catalyst precursor is air stable, readily available, and activated in the reactor. “So unlike a lot of early organometallic chemistry that's extremely air sensitive, this catalyst precursor is easy to handle,” Sadow said.
This chemistry is a step towards being able to affect the physical properties of a variety of plastics, such as making them stronger and easier to color. “As we develop the catalysis more, we expect that we'll be able to incorporate more and more functional groups to affect the physical properties of the polymers,” Sadow said.
Sadow credited the success of this project to the collaborative nature of iCOUP. Perras’ group at Ames National Laboratory studied catalyst structures using Nuclear Magnetic Resonance (NMR) spectroscopy. Coates’, LaPointe’s, and Delferro’s groups from Cornell University and Argonne National Laboratory investigated polymer structure and physical properties. And Peters’ group at the University of Illinois statistically modeled polymer functionalization. “Project successes in the center build on contributions of many groups’ expertise,” Sadow said. “This work highlights the benefits of team science.”