Efficient recovery of lithium from end-of-life batteries and battery production scrap
BASF and Tenova agree long-term cooperation for battery recycling
BASF has entered into a long-term collaboration agreement with Tenova Advanced Technologies (TAT) of Yokneam, Israel, for its battery recycling prototype plant in Schwarzheide, Germany.
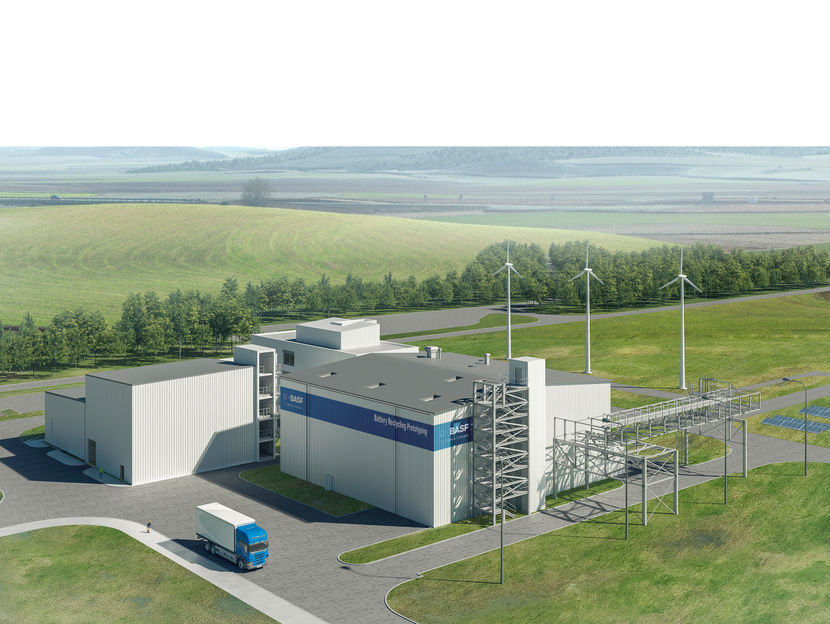
The Schwarzheide battery recycling prototype plant will use innovative technology for extracting lithium, nickel, cobalt and manganese from end-of-life lithium-ion batteries and production scrap.
BASF SE
Both companies agreed to jointly optimize the hydrometallurgical recycling process, leveraging TAT’s novel process for the recovery and production of lithium, which includes lithium solvent extraction (LiSX™) and lithium electrolysis (LiEL™).
The process development activities include pilot campaigns at TAT’s R&D center and the design and fabrication of a prototype plant to be operated at BASF’s facilities in Schwarzheide, Germany. Startup of the prototype plant is targeted for later this year.
Irad Rekem, TAT Managing Director, stated: “We are proud to bring our expertise and innovative technologies to this collaborative effort with BASF to recycle end-of-life batteries. This will be a recycling process that will demonstrate efficient metal recovery and production of lithium salts based on solvent extraction.”
“Using recycled metals for production of new battery materials can reduce the CO2 emission impact of batteries by about 25 percent compared to the use of virgin metals,” said Daniel Schönfelder, Senior Vice President Battery Base Metals and Recycling at BASF. “We will close the loop from end-of-life batteries to new battery production and will ensure an exceptionally low CO2 footprint for key metals needed to meet the growing demand for eMobility. By collaborating with Tenova we can assess new approaches in further optimizing the recycling process.”
TAT is part of Tenova, a global company specialized in sustainable solutions for the green transition of the metals industry, and it is also highly experienced in hydrometallurgy and project-specific process technologies.
Successful startup and operation of the prototype plant is an important milestone in BASF’s strategy to grow its footprint in recycling and recovering valuable metals, including nickel, cobalt, and lithium.
The investment in Schwarzheide reinforces BASF’s support of the European Commission’s agenda towards a European battery production value chain and is part of the “Important Project of Common European Interest (IPCEI)” approved by the European Commission on December 9, 2019 under the European Union State aid rules. The launch of innovative battery materials from the Schwarzheide plant and research to develop next-generation battery materials and process development, including battery recycling, is funded by the Federal Ministry for Economics and Climate Action on the basis of a resolution of the German Bundestag and by the Ministry for Economic Affairs, Labor and Energy of the State of Brandenburg on the basis of a resolution of the Brandenburg State Parliament as part of the IPCEI for Batteries: Funding codes 16BZF101A/B.
Other news from the department business & finance
These products might interest you
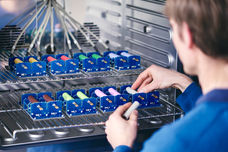
Battery Testing Services by Battery Dynamics
Learn more about the performance and service life of your battery cells in less time
Benefit from modern measurement technology and an experienced team
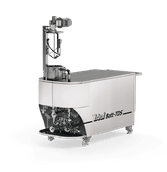
Batt-TDS by ystral
YSTRAL Batt-TDS mixing and dispersing machine
Boost your battery slurry process
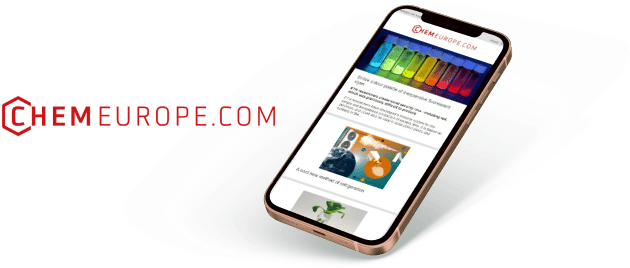
Get the chemical industry in your inbox
By submitting this form you agree that LUMITOS AG will send you the newsletter(s) selected above by email. Your data will not be passed on to third parties. Your data will be stored and processed in accordance with our data protection regulations. LUMITOS may contact you by email for the purpose of advertising or market and opinion surveys. You can revoke your consent at any time without giving reasons to LUMITOS AG, Ernst-Augustin-Str. 2, 12489 Berlin, Germany or by e-mail at revoke@lumitos.com with effect for the future. In addition, each email contains a link to unsubscribe from the corresponding newsletter.
Most read news
More news from our other portals
See the theme worlds for related content
Topic world Extraction
Extraction is a fundamental process in the chemical laboratory that enables specific components to be isolated and concentrated from a mixture. Whether it's extracting active ingredients from natural products, removing impurities from synthesis products, or preparing analytical samples, extraction is a key step in achieving precise and efficient results in chemical research and analysis.
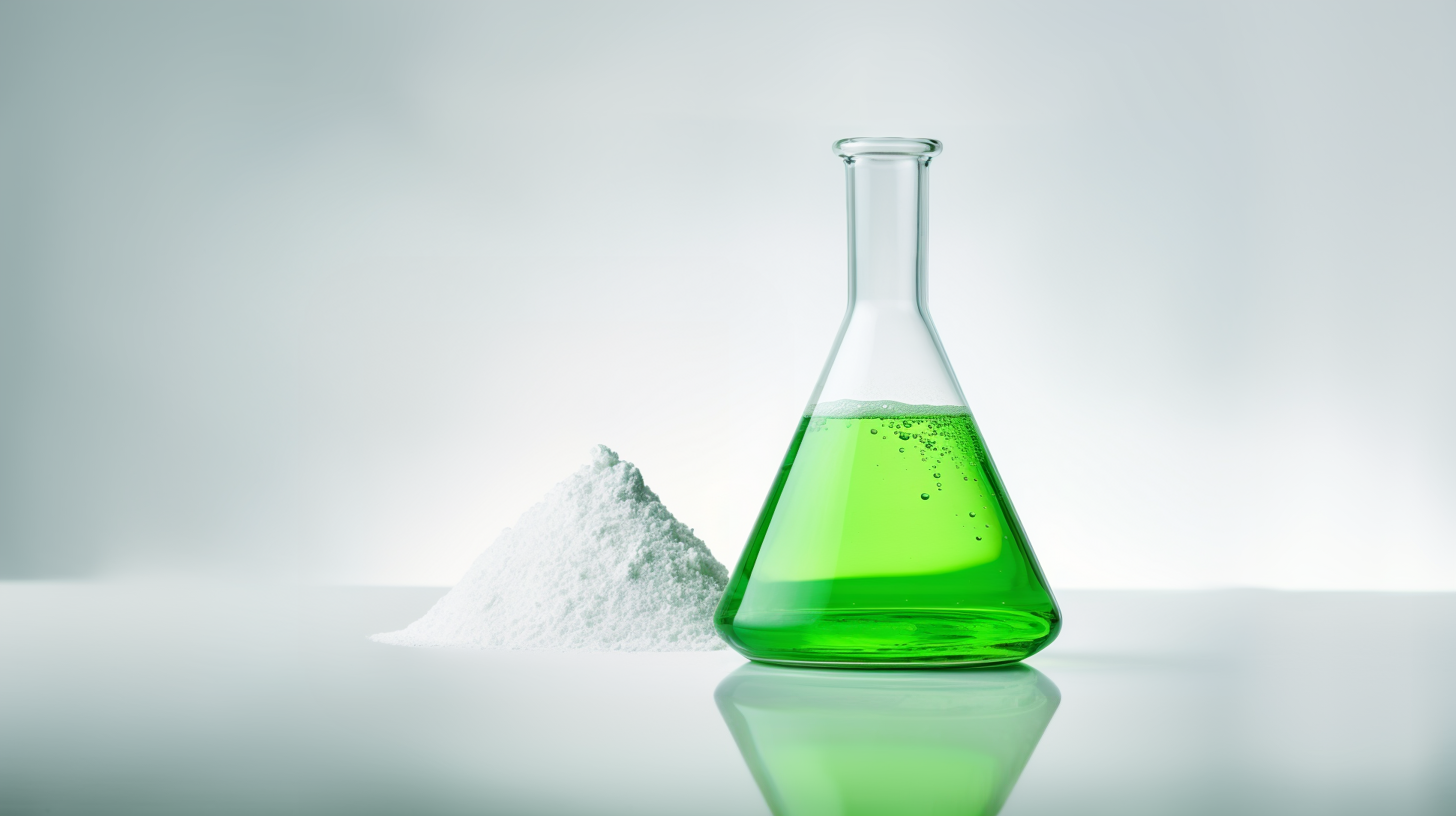
Topic world Extraction
Extraction is a fundamental process in the chemical laboratory that enables specific components to be isolated and concentrated from a mixture. Whether it's extracting active ingredients from natural products, removing impurities from synthesis products, or preparing analytical samples, extraction is a key step in achieving precise and efficient results in chemical research and analysis.
Topic World Battery Technology
The topic world Battery Technology combines relevant knowledge in a unique way. Here you will find everything about suppliers and their products, webinars, white papers, catalogs and brochures.
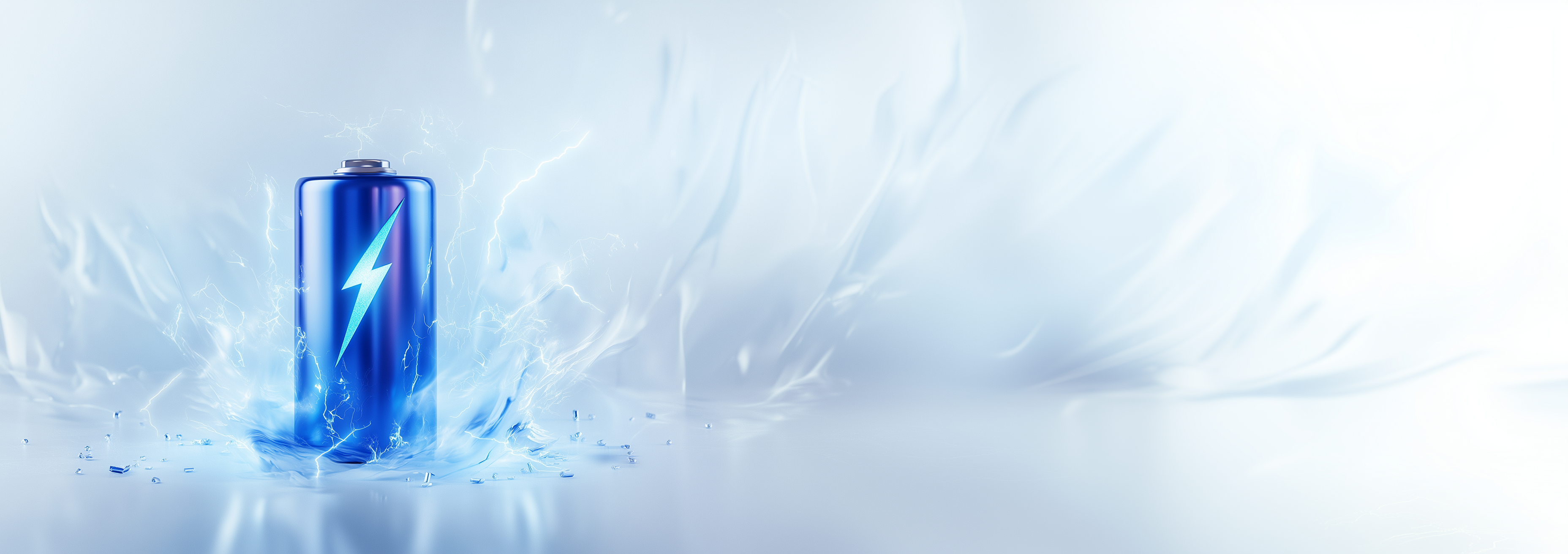
Topic World Battery Technology
The topic world Battery Technology combines relevant knowledge in a unique way. Here you will find everything about suppliers and their products, webinars, white papers, catalogs and brochures.