Spinoff opens new frontier for batteries
Blue Current achieves success with a breakthrough material: Top priority has been to develop a completely safe battery
There is broad consensus that there is no silver bullet for climate change. Rather, many solutions will be required. What makes the challenge particularly daunting is the enormous reductions in greenhouse gas emissions needed in a short period of time. Some experts are concerned that there is not enough time to turn breakthrough scientific discoveries into the revolutionary products necessary to achieve aggressive decarbonization goals.
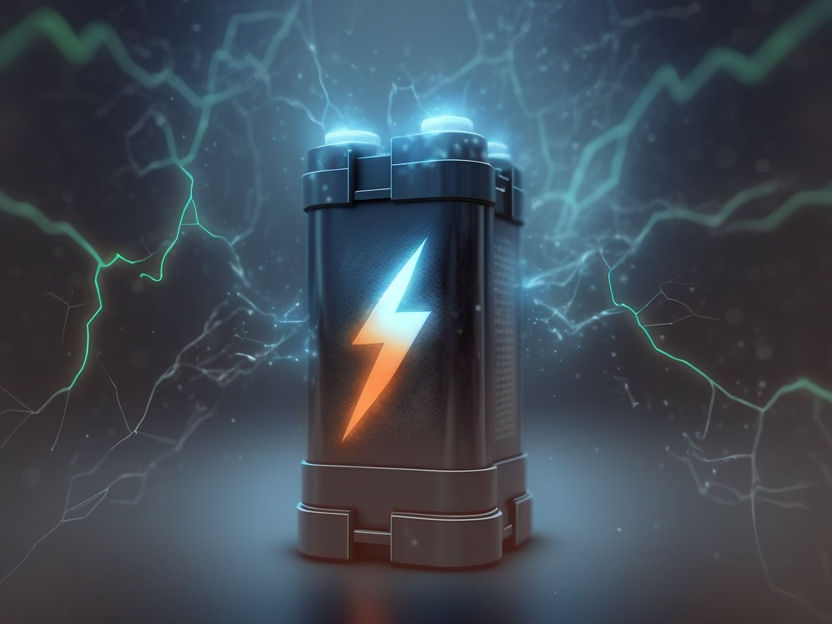
Symbolic image
Computer-generated image
The Joint Center for Energy Storage Research (JCESR), an Energy Innovation Hub led by the U.S. Department of Energy’s (DOE) Argonne National Laboratory, recognized this dilemma when it launched in 2012. JCESR brings together more than 150 researchers from 20 institutions — including national laboratories, universities and industry — to build materials to enable breakthrough batteries.
“JCESR creates and proves the ideas that eventually go commercial,” said George Crabtree, JCESR’s director and an Argonne senior scientist. “These are the riskier ideas that no investors would fund — and that companies are unlikely to pursue — because the outcome is so uncertain. If proven, these ideas can drive the rapid progress on climate change that we need.”
The successful trajectory of JCESR spinoff company Blue Current points to the wisdom of this approach. In 2015, one of JCESR’s laboratories discovered a promising new battery material, known as a “composite,” that can make batteries dramatically safer. Inspired by the composite’s potential, Blue Current developed it further. Now, Blue Current is ramping up production of its battery cells. What’s more, an arm of Koch Industries has invested $30 million in the company to build its first megawatt-scale pilot factory in Hayward, California.
A focus on safety from the start
Safety is an important issue with batteries. When batteries are charged and discharged, substances known as electrolytes carry charge between the positive and negative electrodes. The liquid electrolytes found in many commercial lithium-ion batteries are flammable.
Since its founding, Blue Current’s top priority has been to develop a completely safe battery. At the same time, it has gone to great lengths to avoid the safety related design compromises that other battery companies have made. Its primary target market is electric vehicles (EVs).
“Helping the transition to sustainable energy is part of our core mission, and EVs provide the biggest platform to do that,” said Kevin Wujcik, Blue Current’s chief technology officer. Wujcik was on the JCESR research team that discovered the composite material. At the time, he was pursuing his Ph.D. studies at University of California, Berkeley.
Developing batteries for EVs is particularly challenging because many needs have to be met at once. “An EV battery has to be both a marathon runner and a sprinter,” said Wujcik. “It has to have a very long driving range and operate for a long time. But it also has to be able to charge very quickly. And it needs to work well in low and high temperatures.”
Two internationally recognized battery researchers founded Blue Current in 2014. Nitash Balsara is a JCESR scientist, a professor of chemical engineering at the University of California, Berkeley and a senior faculty scientist at Lawrence Berkeley National Laboratory. Joseph DeSimone, who was a chemistry professor at the University of North Carolina at Chapel Hill in 2014, is a Stanford chemical engineering professor today.
An early pivot
Solid-state batteries, which contain solid electrolytes, are much less flammable than liquid batteries. That’s why many battery developers view solid-state technologies as key to developing completely safe batteries. But solid electrolytes face many technical challenges, and no company has successfully commercialized a solid-state battery to date.
A crystalline class of solids known as glass ceramics have good conductivity, which is the ability to move lithium ions quickly. But they lack the ability to stick to the chemically active materials in battery electrodes that store lithium ions.
Another class of materials known as polymers — large molecules with repeating chemical units — are effective at sticking to electrodes. But they have low conductivity.
Initially, Blue Current focused on developing a battery cell with a nonflammable liquid electrolyte. Then, in 2015, as part of JCESR-sponsored research, Balsara’s lab made a breakthrough discovery that turned out to be a key formative event for Blue Current. The lab addressed the shortcomings of glass ceramics and polymers by bonding them together. The resulting composite solid electrolyte demonstrated good conductivity and good stickiness. Recognizing the composite’s potential to address key challenges with solid-state batteries, Blue Current pivoted to the solid-state field in 2016.
“By combining these materials, the JCESR discovery solved the challenges that each material faced on its own,” said Wujcik. “We decided that using composites was the best way to make the safest battery possible.”
“Getting the science right”
Initially, the anode (negative electrode) of Blue Current’s battery cell was made of lithium metal. Then, in 2018, the company decided to use silicon as the chemically active anode material. One reason for the switch was safety: Lithium metal is highly reactive and flammable, even in solid-state batteries.
Since 2018, the company has refined its composite electrolytes, silicon anode and other battery materials, with an aim of solving the technical challenges of solid-state technology.
“We have focused on getting the science right,” said Wujcik.
One solid-state challenge involves the amount of pressure needed for good battery performance. To help solid electrolytes stick to electrodes, some companies add heavy metal plates and bolts that put battery cells under high pressure. These fixtures increase manufacturing costs while reducing energy density — the amount of energy that can be stored in batteries per unit weight or volume. Lower energy density in EV batteries translates into shorter driving ranges unless the manufacturer increases the size and weight of the batteries. Shorter driving ranges tend to make EVs less attractive to consumers.
Blue Current’s vision has been to use the adhesiveness and elasticity of its composite electrolyte to lower the amount of pressure required for cells to operate. The composite is able to maintain good contact with silicon particles in the anode — without the use of heavy metal plates. This is an impressive achievement: Silicon expands and contracts as a battery cell charges and discharges, which makes it particularly difficult for solid electrolytes to maintain contact.
A second challenge that Blue Current has overcome involves temperature. Because polymer electrolytes have low conductivity, many solid-state battery developers use heating elements to raise the temperature of the cells. While the heat improves the polymers’ conductivity, it requires energy, reducing the battery’s cost-effectiveness. As a result, this approach is not viable for many commercial applications. Today, the high conductivity of Blue Current’s composite electrolytes enables its cells to operate effectively at room temperature.
Solid-state battery developers often struggle to design cost-effective, large-scale manufacturing processes. For example, solid-state cells with lithium metal anodes require specialized manufacturing equipment to avoid formation of dendrites during battery operation. Dendrites are needle-like lithium structures that make batteries less safe and less durable.
Blue Current has overcome this barrier by selecting affordable, abundant silicon anode materials. Additionally, it has designed its components so that they can be processed with the same equipment used by high-volume, lithium-ion battery manufacturers today.
Blue Current’s cells have demonstrated excellent performance. As part of rigorous safety testing, the company subjected its cells to harsh conditions that EVs could encounter in the real world, including crushing, puncturing and overcharging. Thermal runaway — an overheating event in batteries that can lead to fires — never occurred.
“If you get rid of thermal runaway, you make the battery a lot safer,” said JCESR’s Crabtree. “This is especially important in EVs. The batteries are located under the passenger seats.”
In other recent tests, Blue Current’s cells retained 85% of their energy capacity after more than 1,000 charge-discharge cycles — the equivalent of driving hundreds of thousands of miles. It’s a promising sign that the cells will last a long time. According to an EV industry rule-of-thumb, 80% capacity retention is excellent.
The path forward
Blue Current is currently outfitting its Hayward pilot manufacturing plant with high-volume manufacturing equipment. When completed in 2023, the plant will have an annual production capacity of 1–2 megawatt-hours. Here, it will develop the specifications for manufacturing even higher volumes. “The plant is going to lay the groundwork for the next facility,” said Wujcik.
Blue Current also plans to remain focused on research and development. “We’re seeing the battery industry shifting towards the use of silicon anodes to improve the performance of both traditional lithium-ion batteries and next-generation, solid-state batteries,” said Wujcik. “Because the solid-state silicon field is still in an early stage, it’s essential for us to continue our efforts developing new materials.”
Indeed, Blue Current’s success with solid-state silicon batteries opens up a new field for researchers and other companies to explore. “There’s a lot of work that can be done in this space,” said Wujcik. “Researchers can investigate which solid electrolytes and silicon materials to use and how composite electrolytes stick to anode materials.”
Wujcik expressed appreciation for JCSER’s important role in Blue Current’s success.
“The idea of using composites in batteries was new and unproven prior to the JCESR program,” he said. “JCESR put resources behind composites because the materials had potential to address a market need for safe, solid-state batteries while solving important technical challenges. By proving these materials, JCESR made it a lot easier for us to move forward with the technology.”
Something is happening in the chemical industry ...
This is what true pioneering spirit looks like: Plenty of innovative start-ups are bringing fresh ideas, lifeblood and entrepreneurial spirit to change tomorrow's world for the better. Immerse yourself in the world of these young companies and take the opportunity to get in touch with the founders.
See the theme worlds for related content
Topic World Battery Technology
The topic world Battery Technology combines relevant knowledge in a unique way. Here you will find everything about suppliers and their products, webinars, white papers, catalogs and brochures.
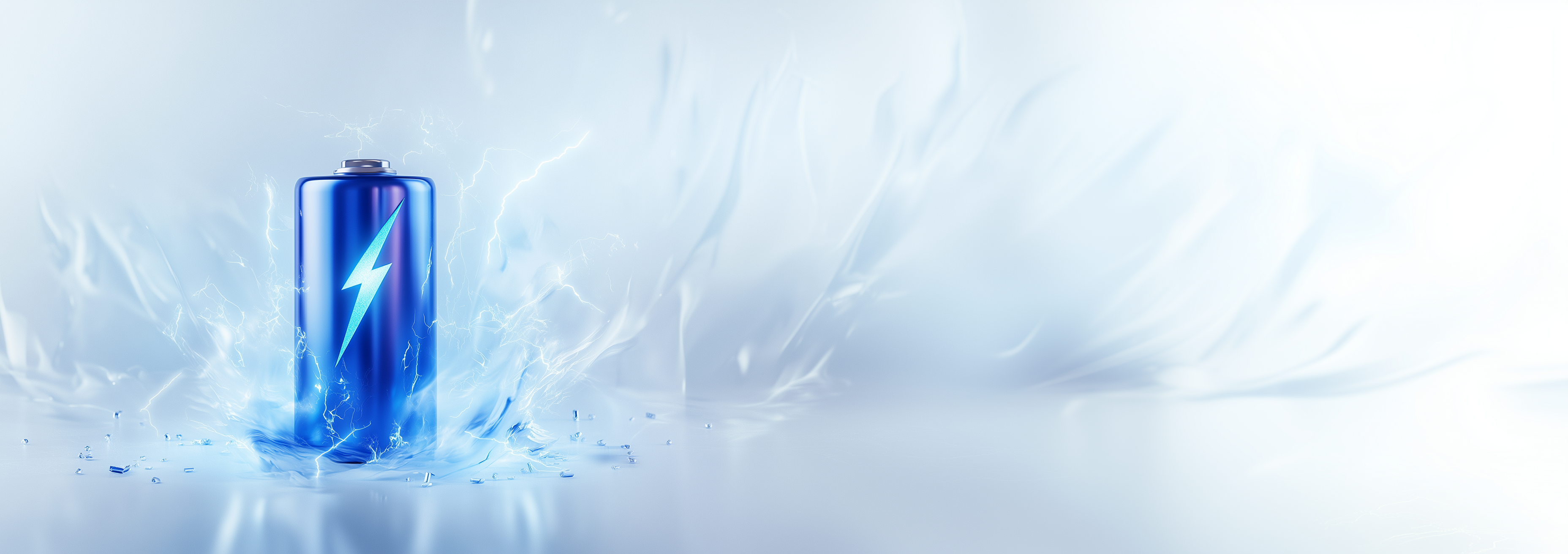
Topic World Battery Technology
The topic world Battery Technology combines relevant knowledge in a unique way. Here you will find everything about suppliers and their products, webinars, white papers, catalogs and brochures.