Small but powerful – microorganisms contribute to greater sustainability at BASF
White biotechnology is becoming an increasingly important part of BASF’s toolbox
At BASF, innovation and sustainability are inextricably linked. Researchers worldwide are working on innovative solutions to tap alternative raw material sources and to develop climate-friendly production processes and products. Current research projects and examples of innovation for various value chain steps were presented by Dr. Melanie Maas-Brunner, member of the Board of Executive Directors of BASF SE and Chief Technology Officer, together with scientists at BASF’s Research Press Conference. The event focused on technologies where microorganisms contribute to greater sustainability.
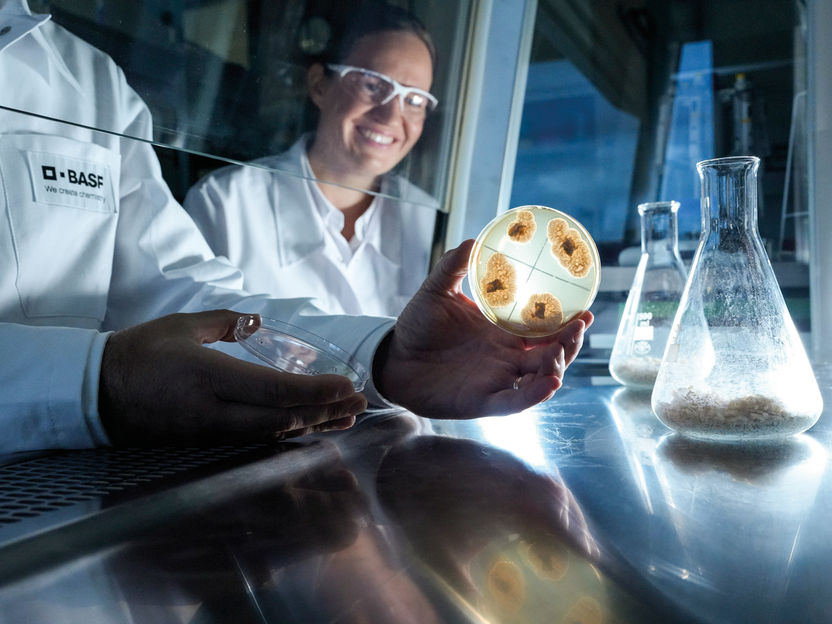
White biotechnology uses microorganisms to make resource-conserving and climate-friendly products from a variety of feedstocks
BASF SE
BASF’s unique R&D platform serves as the foundation for the development of sustainable chemical solutions. “In recent years, we have systematically adapted this platform to the needs of our customers,” said Maas-Brunner. BASF has around 10,000 employees working in research and development worldwide. In 2021, the company invested around €2.2 billion in the development of sustainable products and new technology fields. “Expanding our competencies is an ongoing task for us,” said Maas-Brunner. Examples include generating CO2-free hydrogen, electrifying production processes and advancing the circular economy, as well as tapping new raw material sources and using digital tools even more efficiently.
The investments in research and development are paying off, as evidenced by more than €11 billion in sales generated by products that BASF has placed on the market in the past five years. Within the chemical industry, BASF has a leading position in terms of the number and quality of its patents. “I am especially happy that in 2021, 45 percent of our patent applications were related to innovations with a particular focus on sustainability – and this trend is growing,” Maas-Brunner said. In the long term as well, the company wants to increase its sales and earnings from products that make a significant contribution to sustainability.
“Many of the technologies that will enable a climate-neutral society have not yet been invented,” Maas-Brunner said. It is therefore important to overcome future challenges by being open to technologies and incorporating alternative technology concepts. “To do this, we need alliances – with all players in industry, science, politics and society. Alliances between companies and legislators are especially important because we need good framework conditions underpinning our actions,” Maas-Brunner said.
White biotechnology becoming increasingly important
With its wide range of technological competencies, BASF is well positioned to develop innovative solutions for climate-neutral chemistry. White biotechnology is becoming an increasingly important part of BASF’s toolbox. “These are nature’s tools; people have been using these for a long time and are constantly refining them,” said Dr. Doreen Schachtschabel, Vice President White Biotechnology Research at BASF. Microorganisms, such as bacteria or fungi, are involved in these bioprocesses, including fermentation and bio-catalysis. They use diverse organic materials to transform them into completely different end products. These can be wine, bread or cheese, but also substances for the chemical industry. “White biotechnology has become one of our key technologies that enables us to produce using a variety of feedstocks in an efficient, resource-conserving and, most importantly, flexible manner,” said Schachtschabel.
The list of chemicals and products that BASF produces with white biotechnology methods is long: biopolymers, essential ingredients for human and animal nutrition such as vitamins and enzymes, crop protection products, flavors and fragrances as well as enzymes for detergents and cosmetic ingredients. In five of BASF’s six segments – Chemicals, Materials, Industrial Solutions, Nutrition & Care and Agricultural Solutions – the company already produces more than 3,000 products that are associated with biotechnology or are biodegradable. In 2021, these contributed more than €3.5 billion to sales, and the trend is rising.
To develop new processes and products, BASF researchers work with numerous external academic and industrial partners. The technological foundations and the approaches are usually very similar despite the differing properties of the molecules.
First, a suitable microorganism is identified which can be cultivated. In the next step, the genome is changed, if necessary, thus changing the metabolism in such a way that the bacterium or fungus either makes more of a certain substance or produces an entirely new molecule with new properties.
Then the actual bioprocess begins: The microorganisms produce the target molecule in the desired volumes under optimal conditions. The nutrients and building blocks can be renewable raw materials, such as sugar, but also waste streams, recycled products and chemically synthesized molecules.
Digitalization is essential for the development of new processes and products. It is not only about working more efficiently and effectively. “Without computational biology, specifically bioinformatics, we would not be able to do what we are doing today,” said Schachtschabel.
The development of the insecticide Inscalis™ shows how classical chemistry and biotechnology can ideally complement each other. The first step in the production of this insecticide is fermentation. The intermediate product is then transformed into a finished crop protection product in a subsequent production process based on classical chemistry. “Here, we bring together the best of both worlds: By combining fermentation with selective chemical synthesis, the hybrid process enables us to produce a highly effective and sustainable product cost-efficiently,” said Schachtschabel.
In the future, BASF will continue to rely on a flexible and wide basis of raw materials and technologies. “We recognize that biotechnology, engineering and classical chemistry, when they are optimally integrated, enable processes that are very efficient as well as economically and environmentally sustainable. This will help BASF to achieve its sustainability goals,” said Schachtschabel.
Gaseous carbon as alternative feedstock source
In addition to classical fermentation, which is usually based on renewable raw materials, BASF and the U.S. firm LanzaTech are working together on special processes in which bacteria use gaseous carbon sources, such as carbon monoxide and carbon dioxide, as a raw material. The carbon can come from off-gases from steel mills, refineries and chemical plants but also from gasified household waste. “We would like to tap the potential of gas fermentation to make chemicals for chemical value chains,” said Prof. Michael Helmut Kopf, Director Alternative Fermentation Platforms at BASF. LanzaTech production facilities in China are already using this technology to produce ethanol and a further plant in Belgium will soon be operational. The two companies would now like to produce higher alcohols and other intermediates using gas-fermentation processes.
“Our bacteria are specially designed so that they can transform waste carbon into a variety of desired intermediates,” explained Dr. Sean Simpson, LanzaTech’s founder and Chief Scientific Officer. BASF, in turn, contributes its expertise in chemistry and process technology as well as process intensification into this development project. BASF is also designing the process to separate and purify the products from the fermentation system so these can be fed into the value chains.
There are more than enough alternative carbon sources worldwide that can be used for gas fermentation. “But this will require a change of mindset to enable projects with a cross-sectoral character, for example, connecting the chemical industry with steel mills or waste management firms,” Simpson said. Greater availability of such alternative raw material sources will mean less need for virgin fossil feedstocks to produce chemicals.
“Gasification technologies for residual materials, gas fermentation – together with sustainable hydrogen and renewable energy for product synthesis – and efficient purification processes for the product outputs can, in the future, make an important contribution to improving the sustainability of our value chains,” said Kopf, commenting on the technology’s potential.
Understanding biodegradability in detail
At BASF, bacteria and fungi play a role not only in the production of sustainable products. “For us, sustainability also means knowing exactly how and why microorganisms in the environment biodegrade our products after they are used,” said Professor Andreas Künkel, BASF’s Vice President Research Biopolymers. Biodegradability means that microorganisms metabolize complex organic molecules into energy, water, carbon dioxide and biomass.
To use this natural method and develop fully biodegradable products requires a fundamental understanding of chemistry and of biological processes. Therefore, BASF has significantly expanded its R&D activities relating to biodegradability over the past 10 years. “This incredibly complex topic can only be mastered as an interdisciplinary team,” said Künkel. He stressed the importance of internal and external collaboration with customers, universities and research institutes, with whom BASF carried out extensive experiments in the lab and in the field. “We look in great detail at how we should design materials so that our products biodegrade in soil and in technical systems such as compost and sewage treatment facilities,” Künkel explained.
One example of this is ecovio® mulch film. It is certified biodegradable in soil and helps farmers achieve higher yields. After the harvest, the film can simply be plowed under and will be broken down by microorganisms in the soil. BASF researchers worked with scientists from ETH Zurich to examine how and why the film biodegrades in soil – both in the laboratory as well as in the field. To do so, they developed new methods of analysis which can prove that the carbon in the film is biologically transformed into carbon dioxide and biomass.
Another important application for biodegradable materials are ingredients for laundry detergents, dishwasher detergents and cosmetics that end up in wastewater treatment plants at the end of their life cycles. Here, too, it is crucial to understand exactly how the structure of the material influences its biodegradability.
To expand the portfolio of new certified biodegradable products, digital tools are an important component of the research work. With its extensive collection of data on biodegradability, BASF can develop computer models that can predict at a very early stage of product development the properties and biodegradability of molecules and materials, and thus enable their structures to be adapted accordingly. “BASF is a pioneer and a leader in digital modelling of predictive biodegradability. This is helpful when cooperating with customers to develop tailor-made biodegradable products for a particular application,” said Künkel.