New upcycling system for commercial polyesters
Using commonly available materials and a simple mixing and heating process, polyesters can be transformed into highly recyclable, high-value materials
While plastics or synthetic polymers have many useful properties, their mismanagement has resulted in widespread pollution that chokes up our ecosystems. As a solution to this, many synthetic polymers are sent for reprocessing and recycling; polyethylene terephthalate (PET) is one of the most common products frequently seen in the recycling loop in many countries. However, recycling has its own set of problems. During plastic recycling, partial fractions of the polymer chains are decomposed resulting in structurally weak, downgraded polymers. These sub-standard recycled plastics have much reduced properties and are only good for use as solid fuels. This leaves manufacturers with little choice other than to make new plastic products with fast-depleting petroleum feedstocks.
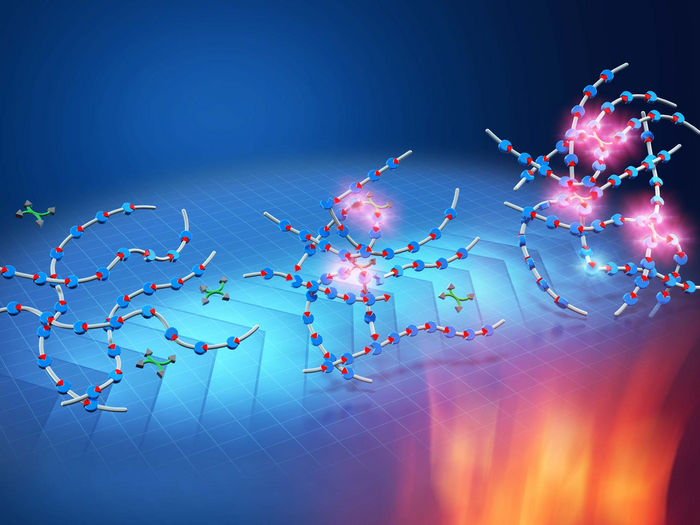
Scientists have developed a one-shot process to transform commonly available polymeric plastics, such as polyesters into highly functional materials called “vitrimers” that can be easily recycled into useful products while retaining enhanced thermo-mechanical properties of the original polymer.
Dr. Mikihiro Hayashi and Nagoya Institute of Technology, Japan
As such, researchers across the world are engaged in developing sustainable cross-linked polymer materials that can be recycled efficiently and cost-effectively. Adding to the growing body of knowledge, Dr. Mikihiro Hayashi, Assistant Professor at Nagoya Institute of Technology, Japan, and his colleague Mr. Takahiro Kimura have developed a simple method to recycle polyester, a common plastic material, into a cross-linked polymer that retains its strength and properties when recycled. Their method centers around transforming polyesters into vitrimers—a new class of polymers possessing dynamic covalent bonds that can reversibly break and reform to create new cross-links. The dynamic covalent bonds render the vitrimer with desirable properties, such as recyclability, reprocessability, and healing capabilities, which are characteristics of high-value functional materials. The study was published on August 1, 2022 in the Journal of Materials Chemistry A.
Talking about their study, Dr. Hayashi says, “Our research demonstrates a one-shot upcycling process of commercial polyesters into cross-linked vitrimers with enhanced thermo-mechanical properties and sustainable functions.” He and his colleague created the vitrimers by simply mixing polyester with a cross-linker molecule— tetra-epoxy, along with the chemical compound 1,8-diazabicyclo[5.4.0]undec-7-ene (DBU) as a catalyst in the presence of tetrahydrofuran as the solvent. The solvent was later evaporated, and the remaining mixture was heated at 200°C for 24 hours, producing a film of vitrimer.
With this method, the cross-linking for producing vitrimer occurs in three quick sequential stages—hydrolysis (breaking of the polyester bonds), epoxy-opening reaction, and intermolecular transesterification. Discussing the superior mechano-elastic properties of the produced vitrimers, Dr. Hayashi says, “The highly cross-linked and recyclable vitrimer exhibits a 60-fold increase in tensile modulus or Young’s modulus and a 10-fold increase in the maximum endurable stress when compared with the original polyester. It also has a gel fraction of nearly 100%.” Moreover, the vitrimer was observed to retain its properties even after being ground into fractured pieces and pressed into a flat sheet, which reaffirms its recyclability.
Plastics are essential materials with many benefits and useful properties because they are lightweight, cheap, non-toxic, and easy to produce. However, at the same time, it is necessary to acknowledge and limit the environmental damage they cause. Improving the recyclability of plastic polymers will encourage recycling programs and reduce the use of petroleum, a non-renewable resource. As Dr. Hayashi rightly observes, “The world needs versatile options for recycling synthetic polymers. The method we propose will not only eliminate the use of petroleum-derived chemicals, but it could also be the first step towards a practical and sustainable upcycling system for the future, which adheres to the principles of circular economy and helps realize the SDGs.”
As a step forward, the researchers are now planning to devise a more direct transformation of polyesters into vitrimer without using any solvents and are also looking into using their method to transform commercial PET into other highly recyclable materials. If successful, the developed method could lead to a closed loop of plastic production and avert any further environmental crises caused by excessive plastic production.
Most read news
Topics
Organizations
Other news from the department science
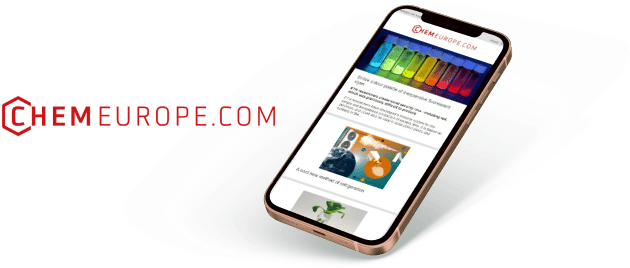
Get the chemical industry in your inbox
By submitting this form you agree that LUMITOS AG will send you the newsletter(s) selected above by email. Your data will not be passed on to third parties. Your data will be stored and processed in accordance with our data protection regulations. LUMITOS may contact you by email for the purpose of advertising or market and opinion surveys. You can revoke your consent at any time without giving reasons to LUMITOS AG, Ernst-Augustin-Str. 2, 12489 Berlin, Germany or by e-mail at revoke@lumitos.com with effect for the future. In addition, each email contains a link to unsubscribe from the corresponding newsletter.