Hydrogen economy: BAM develops more efficient test method for materials
Green hydrogen is to be used as an emission-free energy carrier on a large scale as soon as possible. Before this happens, materials and components, e.g. for fittings, seals, distribution networks and hydrogen filling stations, must be carefully tested for their suitability and safety. The Federal Institute for Materials Research and Testing (BAM) is developing an innovative testing methodology for this purpose, which should significantly accelerate the market ramp-up of hydrogen.

In the method, hydrogen is passed through a material sample from the inside. This significantly reduces the safety effort and thus the costs. Florian Konert (BAM) inspects the test setup.
BAM
Germany has more than 500,000 kilometers of natural gas pipelines supplying energy to industry and households. This infrastructure will play a key role in the transition to a hydrogen economy: fossil natural gas is to be gradually replaced entirely and up to 100 percent hydrogen is to be fed into the existing distribution network, which can also serve as a storage facility for the energy carrier. In addition, the construction of new hydrogen pipelines is planned.
Before that, important safety aspects must be clarified; for example, whether the pipelines, seals and distribution stations, some of which are decades old, are at all suitable for transporting pure hydrogen.
In principle, hydrogen can be transported in a similar way to natural gas; however, the atoms are particularly small, which favors their absorption by metals. In steels, for example, such as those used in today's infrastructure, this can lead to a deterioration of the material properties. Under mechanical stresses, such as those found in any gas network, this can promote cracking and lead to dangerous leaks.
To check pipeline steels for degradation, material samples have so far been subjected to elaborate tests: They are exposed to hydrogen in an autoclave and mechanically stressed in the process. "Because of the large amount of hydrogen required, such laboratory tests require a high level of safety and are correspondingly costly. This hinders a rapid expansion of testing capacities as they will be needed in the coming years," explains Florian Konert, scientist at the Hydrogen Competence Center H2Safety@BAM.
The engineer and the team are working on a testing technique that will make it much easier to show possible damage in the future - at lower cost. This involves filling a steel specimen with hydrogen from the inside and simultaneously subjecting it to a mechanical tensile load. The method requires only a fraction of the previous amount of hydrogen, which significantly reduces the safety-related expense. "We are convinced that our approach will expand the existing testing possibilities and thus enable a faster market ramp-up of hydrogen," says Konert's colleague Jonathan Nietzke, also a scientist at BAM's Hydrogen Competence Center.
Using their innovative testing technique, the two researchers plan to rank materials according to their suitability for hydrogen use, including pipeline materials in the natural gas distribution network. The results can provide companies that operate gas networks or that manufacture components for the hydrogen economy with an important basis for evaluating materials and thus accelerate the retrofitting of existing plants or the construction of new ones.
Note: This article has been translated using a computer system without human intervention. LUMITOS offers these automatic translations to present a wider range of current news. Since this article has been translated with automatic translation, it is possible that it contains errors in vocabulary, syntax or grammar. The original article in German can be found here.
Other news from the department science
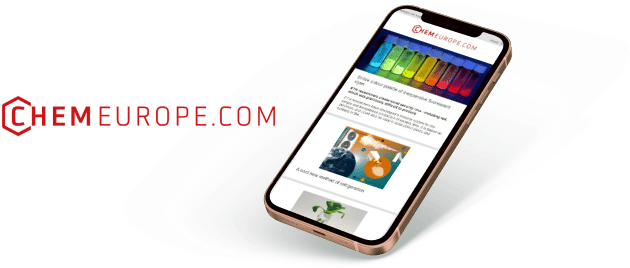
Get the chemical industry in your inbox
By submitting this form you agree that LUMITOS AG will send you the newsletter(s) selected above by email. Your data will not be passed on to third parties. Your data will be stored and processed in accordance with our data protection regulations. LUMITOS may contact you by email for the purpose of advertising or market and opinion surveys. You can revoke your consent at any time without giving reasons to LUMITOS AG, Ernst-Augustin-Str. 2, 12489 Berlin, Germany or by e-mail at revoke@lumitos.com with effect for the future. In addition, each email contains a link to unsubscribe from the corresponding newsletter.
Most read news
More news from our other portals
Last viewed contents
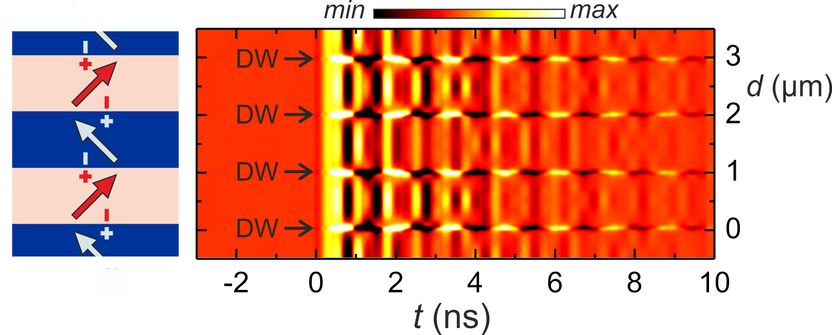
Manipulation of the characteristics of magnetic materials
Inorganic materials display massive and instantaneous swelling and shrinkage
Lipoic_acid
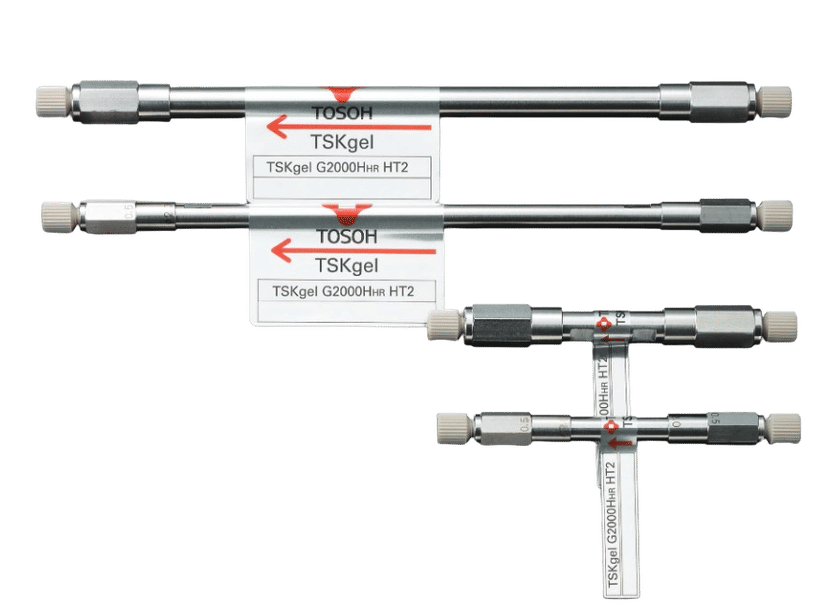
TSKgel HT2 Series Columns | GPC columns | Tosoh
Vesuvianite
Category:EC_3.11
Table_of_nuclides,_73-96
