Catalyst technology for mobile use of liquid hydrogen storage systems
In the research project "Power density hydrogen release from LOHC systems on mobile platforms", the Fraunhofer Heinrich Hertz Institute (HHI) and the Helmholtz Institute Erlangen-Nuremberg (HI ERN) have developed an efficient and stable surface catalyst for the release of hydrogen from liquid storage materials. With this catalyst, the researchers pave the way for the mobile application of Liquid-Organic-Hydrogen-Carrier (LOHC) technology using rail transport as an applied case. In correspondance, current diesel trains are replaceable by modern alternatives using low-emission hydrogen in the future.
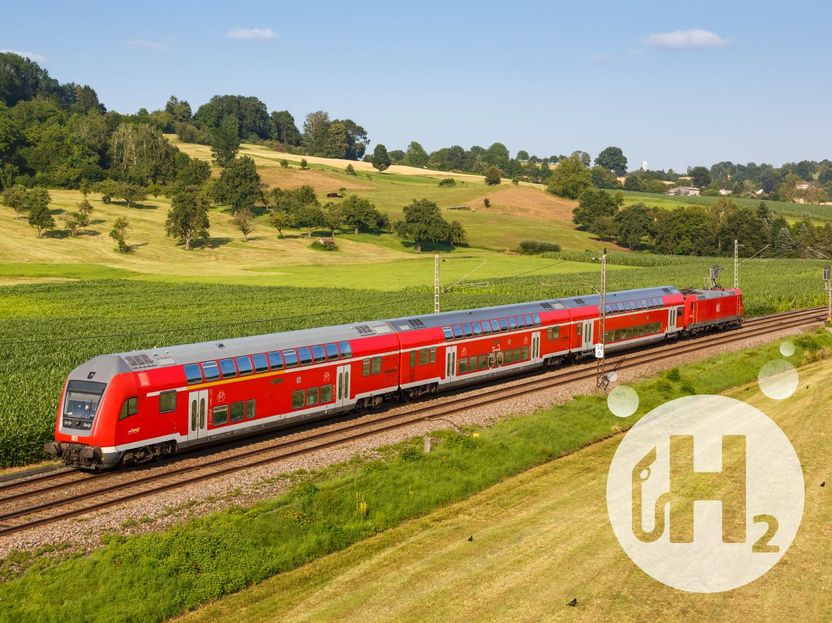
"Emission-free and highly emission-reduced rail transport on non-electrified tracks"
© Markus Mainka/Shutterstock.com, r.classen/Shutterstock.com edited by Fraunhofer H
In context, 40 percent of the German rail network is not electrified yet. A large part of the infrastructure is not suited for electric locomotives because encompassing electrification is cost- and time-intensive. LOHC technology offers an alternative to this scenario. Serving as a transport vector for green hydrogen, it can save emissions while maintaining the train service infrastructure.
In the LOHC process, gaseous hydrogen is bound to a non-hazardous carrier liquid which is safe to store and transport. The bound hydrogen can be released again in a catalytic reaction utilizing heat. The organic carrier liquid is thereby not consumed but reusable. Concerning its handling and physical properties, the oily substance is similar to conventional fuels and is easily transportable by tankers and trains.
LOHC technology has been researched well for several years. However, there have not yet been any so-called 'hydrogen releasers' that could perform the process efficiently for mobile applications. The joint research team from Fraunhofer HHI and HI ERN has now developed an apparatus that elevates the hydrogen release process to a reproducible and scalable level. Additionally, a significant increase in power density is achieved compared to conventional hydrogen releasers.
The core of the apparatus is a so-called surface catalyst. Catalysts need as much surface area as possible to release hydrogen efficiently. Previous processes work with porous pellets for this purpose. Unfortunately, these pellet catalysts wear off quickly in mobile applications because the mechanical stability of the pellets is not high enough.
For the surface catalyst, aluminum plates are structured using a femtosecond laser and then coated with fine platinum dots. The surface of the structured plate thus offers a large internal surface area which can be enlarged by 7,000 to 10,000 times within this process. Consequently, even small aluminum plates provide enough surface area for effective hydrogen release. Another advantage of this process is the conversion of existing and industrially proven heat exchanger technologies into hydrogen releasers. Such dynamics allow researchers to apply the technology cost-effectively and quickly.
On behalf of HI ERN, the "Fiber Optic Sensor Systems" department of Fraunhofer HHI is currently manufacturing additional surface catalysts that would also be applicable for constructing a first demonstrator train powered by hydrogen.
The development of the catalyst technology is part of the large-scale project "Emission-free and highly emission-reduced rail transport on non-electrified tracks", funded with 28 million euros by the Bavarian Ministry of Economic Affairs, Regional Development and Energy.
Most read news
Other news from the department science
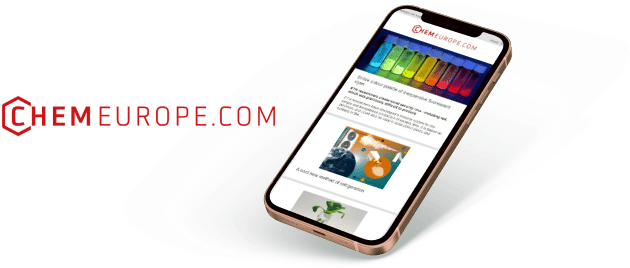
Get the chemical industry in your inbox
By submitting this form you agree that LUMITOS AG will send you the newsletter(s) selected above by email. Your data will not be passed on to third parties. Your data will be stored and processed in accordance with our data protection regulations. LUMITOS may contact you by email for the purpose of advertising or market and opinion surveys. You can revoke your consent at any time without giving reasons to LUMITOS AG, Ernst-Augustin-Str. 2, 12489 Berlin, Germany or by e-mail at revoke@lumitos.com with effect for the future. In addition, each email contains a link to unsubscribe from the corresponding newsletter.