Clean production processes in the chemical industry
TU Delft and TNO prepare industry for scale-up phase of clean factory
Oil and gas shortages are not only pushing up the prices of gas and petrol, but also plastics, medicines and cosmetics. To make our society less dependent on fossil fuels and combat climate change, the chemical industry needs to change radically. In recent years, TU Delft and TNO have laid the foundation for cleaner production processes in the chemical industry. The new e-Chem partnership is now taking this a step further by actually constructing a clean factory of the future.
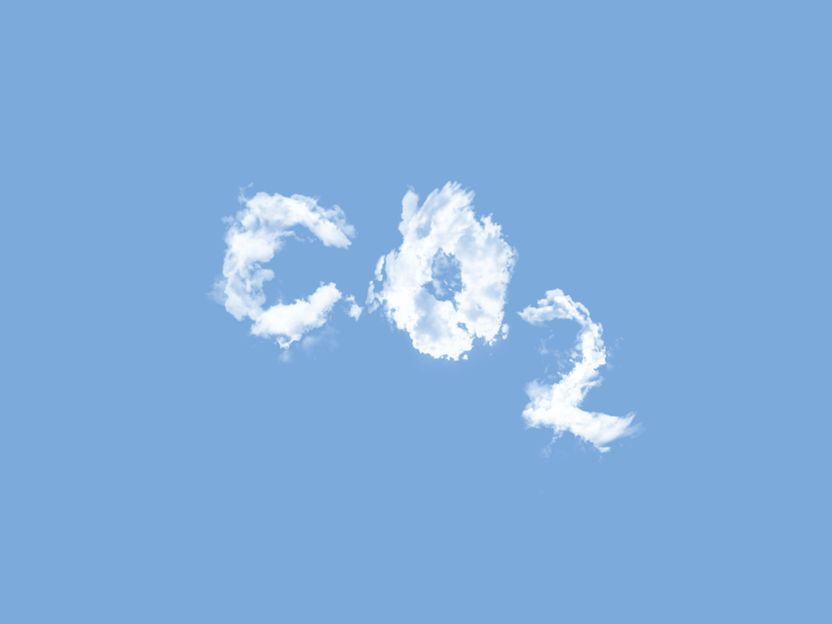
Together with other knowledge institutions and industry, e-Chem is now going to build large-scale installations that will convert CO2 from the air into three basic building blocks for the chemical industry using electrolysis on an industrial scale and at competitive prices: methanol, ethylene and kerosene.
Unsplash
According to the 2015 Paris Climate Agreement, by 2050 our society should be carbon-neutral. We will not achieve this goal without radically changing the chemical industry. One of the options is to take CO2 from the air and convert it into raw materials for the production of plastics and fuels, among other things, using sustainably generated electricity. To accelerate the process of making the chemical industry more sustainable, e-Refinery (TU Delft) and Voltachem (TNO), two large-scale research programmes in the field of electrification of the chemical industry, are joining forces in the e-Chem programme.
"The electrification of the chemical industry offers great opportunities for the Netherlands to become the leading supplier of high-end systems for the energy transition. And where better to develop such solutions than here in Delft, right next to Botlek, the largest petrochemical hub in north-western Europe? Together with other knowledge institutions and industry, e-Chem is now going to build large-scale installations that will convert CO2 from the air into three basic building blocks for the chemical industry using electrolysis on an industrial scale and at competitive prices: methanol, ethylene and kerosene. We are the first to build such large-scale plants. We decided to simply go for it, and we will learn by doing. This is the approach that will allow us to accelerate", Ruud van Ommen (e-Refinery) and Martijn de Graaff (VoltaChem).
Electrolysis technology
The principle of electrolysis has been known for a long time. You take a container with a liquid that conducts electricity. You send the gaseous CO2 through it. You put two metal plates in the container, covered with a catalyst. You put a voltage across them. An electric current flows from one plate to the other, right through the gas/liquid mixture. This current causes the chemical bonds between the carbon and the oxygen and between the molecules of which the liquid is composed to be broken and new substances to be formed.
Before this technology can be applied on a large scale in the chemical industry, there are still some challenges to overcome, according to Ruud van Ommen and Martijn de Graaff. ‘We are going to build installations that produce 50 to 100 litres of product a day. For that, we need to design systems that are stable, which means that they keep producing the same quality at the same speed for months or years on end. That is not possible currently. We also want to use electricity generated by wind turbines or solar panels. But that supply is unpredictable. How do you design a process that can deal with that? And what does the fluctuating supply of electricity mean for the production capacity of such a plant?’
Scaling up the technology itself is also easier said than done, Van Ommen explains. ‘With traditional chemical processes, you just make your reactor vessel bigger. With an electrochemical process, for technical reasons, you have fixed distances between the two metal plates and a maximum height of the reactor vessel. So you can only scale up by using more plates or by making the plates wider. But what does that mean for the amount of current flowing through your reaction liquid, and for the temperature distribution during the reaction? From which material should you make the catalysts for the reactions, and are those materials available in sufficient quantity? e-Chem will help us find answers to these kinds of practical questions more quickly.’
Promising avenues to success
TU Delft has gained experience at e-Refinery in fundamental and applied research into materials, processes and reactors at all length scales, from the atomic to the reactor scale. TNO has extensive experience in practical testing and subjects such as life cycle analysis and business models. By combining this knowledge and expertise, both parties aim to set up demonstrations within a few years that will persuade industry to invest in this technology.
The research agenda will focus on the most promising avenues to success. ‘For example, it is a conscious choice to use CO2 from the air as a raw material,’ De Graaff says. ‘Because factories are already reducing the CO2 content of their flue gases, we believe that this source of CO2 will slowly dry up in the future.’ It is not a coincidence that they opted for products such as methanol, ethylene and kerosene either. ‘Ethylene and methanol have many possible applications, ranging from plastics to pills,’ De Graaff says. ‘For fuels, we also tried to identify the most promising business case. For passenger transport, there are advanced options to switch to batteries or hydrogen. But for aviation, kerosene will probably remain irreplaceable for a long time to come. A cleaner production process is therefore also very desirable in that case.’
Open invitation
Both researchers emphasise that e-Chem emerged from a shared ambition to accelerate the transition of a chemical industry based on fossil raw materials to a sector based on sustainable electricity and CO2. ‘The market is not going to do that on its own. And we are not going to succeed with only two parties either. We therefore urge other academic and industrial partners to join us.’