Catalyst for a greener future
Researchers improve the ability of catalysts made from metal-metal oxides to convert non-edible plants into renewable fuels, chemicals and plastics
catalysts are workhorses that help reactions occur. Put to work, they transform starting materials, such as fossil fuels, biomass or even waste, into products and fuels with minimal energy.
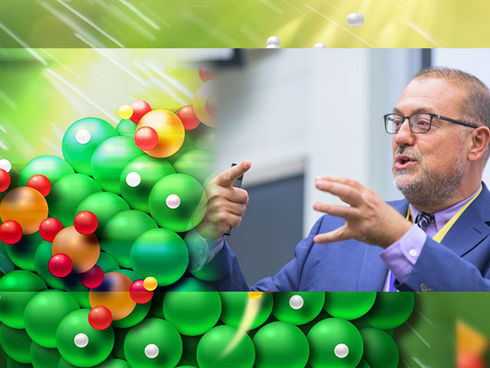
According to researchers in the Catalysis Center for Energy Innovation at the University of Delaware, irrigating a catalyst with hydrogen boosts the active sites and accelerates the chemistry that occurs there.
Graphic illustration by Jeffrey C. Chase
Researchers in the Catalysis Center for Energy Innovation (CCEI) at the University of Delaware have found a way to improve the ability of catalysts made from metal-metal oxides to convert non-edible plants, such as wood, grass and corn stover — the leaves, stalks and cobs leftover in the fields after harvest — into renewable fuels, chemicals and plastics.
Metal–metal oxide catalysts are central to reactions for upgrading petrochemicals, fine chemicals, pharmaceuticals and biomass.
The research team’s strategy capitalized on the dynamic nature of platinum-tungsten oxide catalysts to convert these starting materials into products up to 10 times faster than traditional methods. It’s the type of innovative catalytic technology that could help usher in a more sustainable and greener future, where processes require less catalyst to operate, leading to less waste and less overall energy use.
Boosting catalyst activity
The surface of a catalyst contains multiple active sites at which chemical reactions occur. These active sites are sensitive and dynamic, changing in response to their environment in highly complex and often difficult-to-predict ways. As a result, little is known about how processes on these active sites operate or how the sites interact with their surroundings. Traditional approaches for increasing understanding, such as studying catalysts under static conditions in a chemical reactor, don’t work.
So CCEI researchers combined modeling, advanced synthetic techniques, in-situ spectroscopies and probe reactions to get a better look at how platinum and tri-tungsten oxide catalyst materials come together, what structure they take and what happens on the catalyst’s surface. In particular, the research team was interested in how the active sites on a catalyst (where the chemical reactions occur) evolve over time and when exposed to specific changes.
“By identifying the telltale signs of their dynamics, we were able to establish, for the first time, a robust model to predict their behavior in various working environments,” said Jiayi Fu, the paper’s lead author, who recently earned his UD doctoral degree in chemical engineering and now works at Bristol Myers Squibb.
Fu explained that catalyst surfaces — like plants — flourish when given the proper balance of sunshine and sustenance. The research team successfully demonstrated a novel “irrigation” strategy which uses hydrogen pulsing to significantly increase the population of active sites on these catalysts, allowing reactions to occur 10 times faster.
"We’re not actually watering the catalysts, that’s just a metaphor. But, by pulsing hydrogen gas on and off, we create these active sites that mimic water, through a process known as hydroxylation,” said Dion Vlachos, the Unidel Dan Rich Chair in Energy, professor of chemical and biomolecular engineering and director of CCEI. “These active sites then do the chemistry. So, like light and water feeds the plants, here we feed hydrogen to ‘water’ the catalyst and make it produce — or grow — new chemicals.”
The work illustrates a successful example of how simulations can predict catalytic behavior and enable the rational design of more efficient catalytic processes, said Vlachos, who also directs the Delaware Energy Institute. The findings also provide a viable way to study, understand and control this important class of catalysts.
“Catalysts are known to evolve and respond to their environment, but they do this quickly, in ways that have been hard to observe in real time,” he said. “This work sets a platform for how to dissect their working behavior and, importantly, how to engineer them for unprecedented performance enhancement.”
Original publication
Most read news
Other news from the department science
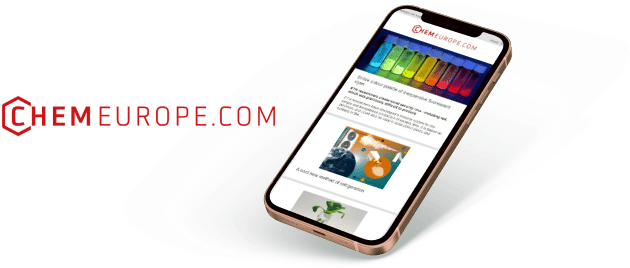
Get the chemical industry in your inbox
By submitting this form you agree that LUMITOS AG will send you the newsletter(s) selected above by email. Your data will not be passed on to third parties. Your data will be stored and processed in accordance with our data protection regulations. LUMITOS may contact you by email for the purpose of advertising or market and opinion surveys. You can revoke your consent at any time without giving reasons to LUMITOS AG, Ernst-Augustin-Str. 2, 12489 Berlin, Germany or by e-mail at revoke@lumitos.com with effect for the future. In addition, each email contains a link to unsubscribe from the corresponding newsletter.
Most read news
More news from our other portals
Last viewed contents
Pfizer to Acquire BioRexis to Access Novel Technology Platform and Early Stage Diabetes Pipeline
Category:Methyl_indoles
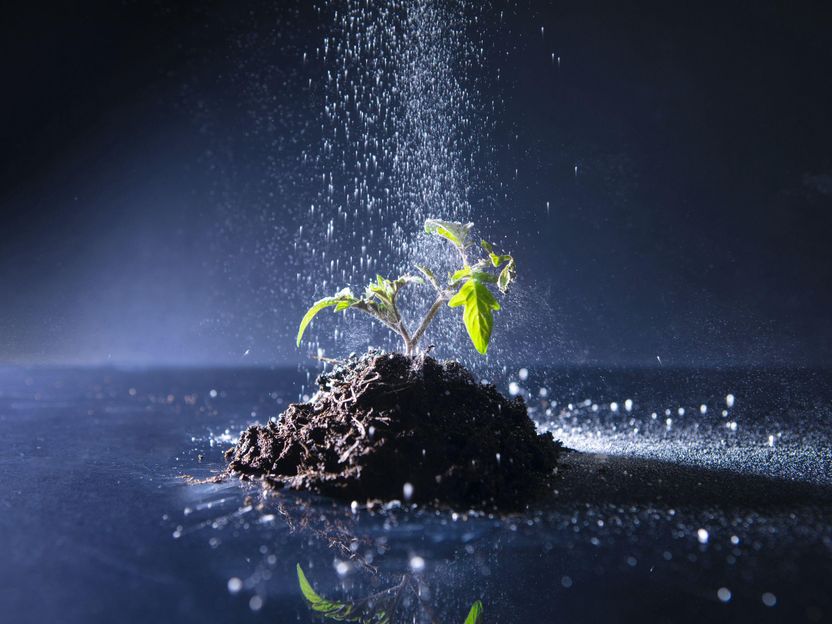
PETRA III shines a light on efficient production technique for a novel ‘green’ fertiliser - Advanced milling technique produces slow-release soil nutrient crystals
Luis_Federico_Leloir
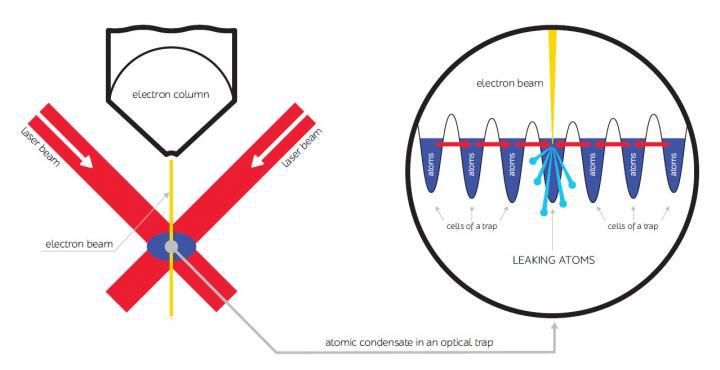
Antilaser for Bose-Einstein condensate
Edgar_Fahs_Smith
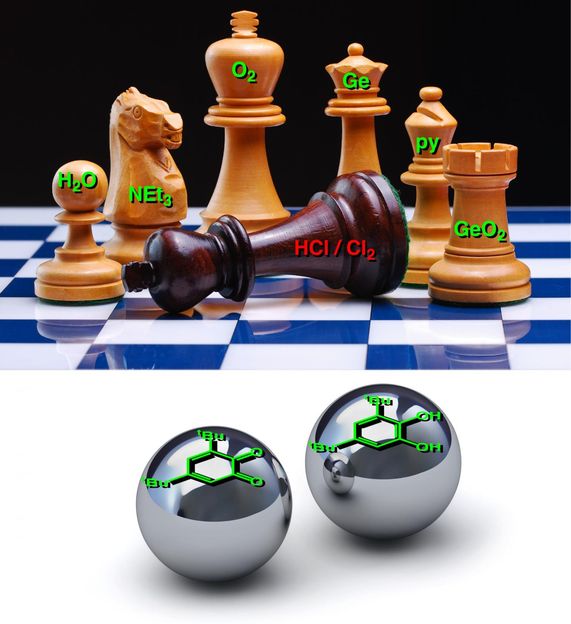