Micrometer-sized particles encased in tailored polymer membranes
Hereon team unravels how metal hydrides can better store hydrogen
metal hydrides are considered a cutting-edge storage material for hydrogen. These hydrides function even better, if the micrometer-sized hydride particles are coated with a thin polymer film. Using a sophisticated microscopy technique, a team at Helmholtz-Zentrum Hereon can now successfully show in detail, how the polymer-coated particles transform during charging and discharging with hydrogen. The results are encouraging and bring practical use of the new technology one step closer. The results are presented in the scientific journal Advanced Materials Technologies.
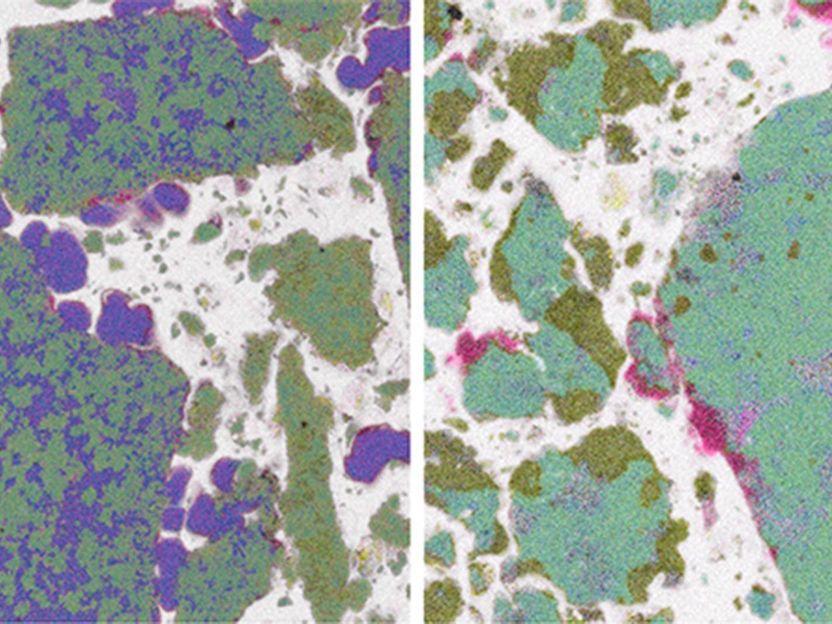
Both images of metal hydrides were taken with a scanning electron microscope/ energy dispersive X-ray microanalysis.
Hereon/ Clarissa Abetz
Hydrogen is considered a vital component of the energy transition: it can be produced from solar or wind power and therefore stores green energy in form of an environmentally friendly energy carrier, providing energy also at night and during periods of calm winds. Hydrogen also acts as a climate-neutral fuel for fuel-cell cars and trucks, enabling greater ranges than battery-powered vehicles. Common pressure gas tanks for hydrogen vehicles, however, are still too bulky and their cylindrical shape is difficult to accomodate. The experts are therefore working on an alternative: metal hydride storage. The metal compounds ground into fine powders can bind the hydrogen in astounding quantities. A metal hydride storage unit can store up to 50% more hydrogen than a 700-bar pressure tank of the same size, and due to low pressures, is conformable in shape.
Helmholtz-Zentrum Hereon has developed and patented an especially efficient metal hydride system. “Here we combine several hydrides together,” says Thomas Klassen, director of the Hereon Institute of Hydrogen Technology and professor at Helmut Schmidt University in Hamburg. “These hydrides react with each other providing additional energy for discharge of hydrogen.” This reduces the required temperature for discharge, and the system becomes more energy efficient.
Protection Against Oxygen
There are two limitations here, however. On the one hand, the different hydride components should not separate too far from each other during hydrogen charging, because their reaction during discharge would then be too sluggish. On the other hand, metal hydride particles are susceptible to surface oxidation, blocking hydrogen access. “Both problems can be alleviated by coating the grains with a polymer,” says Volker Abetz, director of the Hereon Institute of Membrane Research and professor at the University of Hamburg. “This polymer only allows hydrogen to pass through, but not oxygen, and it prevents long-range separation of the different metal hydrides.”
This polymer trick has actually been known in the laboratory for some time now. What exactly was going on, however, had so far been unclear. Through sophisticated imaging, the Abetz and Klassen teams could now visualize the changes during charging and discharging. Initially, the experts produced extremely fine and thinly layered metal hydride samples. They then examined these samples with a special scanning electron microscope. This resulted in high-resolution images of the micrometer-sized metal hydride grains coated by the polymer, both in the charged and discharged states.
Excellent Job
“Because the method is element specific, the different metal hydrides can be distinguished from one another,” explains Abetz. The measurements demonstrate that the polymer coating serves as excellent protection against oxygen. “Furthermore, we also could observe that the encapsulation in polymers actually prevents coarsening and segregation of the different metal hydride components,” adds Klassen. “Over many cycles, the system can quickly be charged and discharged with hydrogen. The polymers are therefore doing an excellent job!”
Based on these new insights, the Hereon experts are now able to systematically optimize the polymer-coated metal hydrides. Future plans include searching for further improved and tailored polymers that can be used to coat the hydride particulates even more effectively. In the framework of a subsequent project together with partners from the Technical University of Hamburg and the University of Hamburg as well as a commercial company, the researchers wish to test the concept of polymer coating for stationary hydrogen storage systems, thereby considerably increasing their durability.