X-ray view into hydrogen production
Analysis points the way to more durable iridium electrodes
green hydrogen is expected to play a central role in the energy industry of the future: Among other things, it can replace oil and gas as energy carriers and also enable emission-free production of steel and cement. For an efficient hydrogen economy, however, the production of the energy-containing gas must be improved. Researchers from DESY, the Justus Liebig University Giessen, the Universities of Lund and Copenhagen and the Helmholtz Institute Erlangen-Nuremberg for Renewable Energies have now investigated the costly wear of electrodes for hydrogen production at DESY's X-ray light source PETRA III. The analysis points the way to more durable electrodes, as the team reports in the journal ACS Catalysis of the American Chemical Society (ACS).
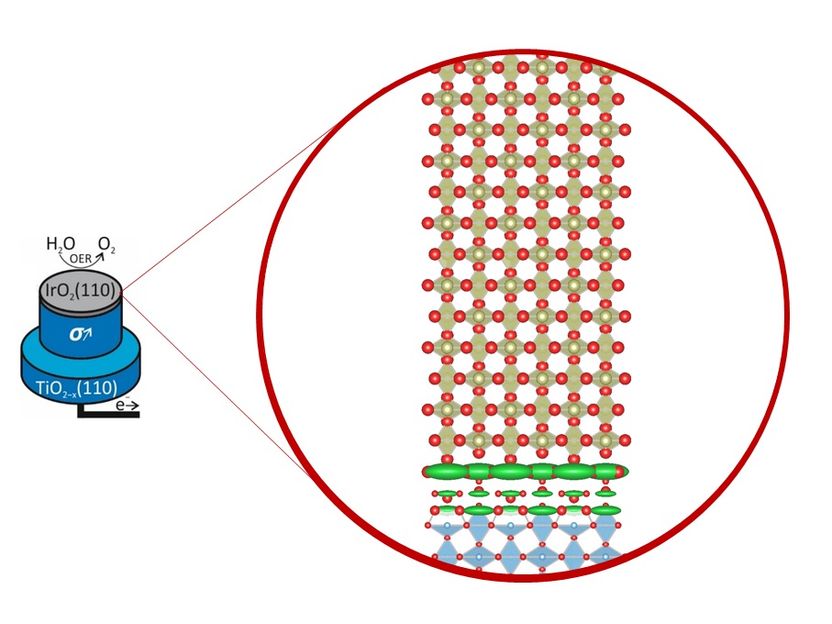
If the electrodes for hydrogen production are coated particularly evenly with stabilising iridium, they do not wear out as quickly. This insight can make the electrical splitting of water (electrolysis) more efficient.
DESY, Vedran Vonk
Green, or climate-neutral hydrogen is produced today with so-called electrolysers. With the help of electricity from renewable energies, they split water into its components oxygen and hydrogen. For this molecule splitting to work, current must be passed through a reactive acidic solution. For this purpose, very corrosion-resistant electrodes are used, which also serve as catalysts and decisively accelerate the reaction. One of the materials used for this is the rare precious metal iridium: in many electrolysers, the anodes are coated with a thin layer of iridium oxide. The problem is that these coatings wear off over time and corrode. This reduces the durability of the equipment and makes production costs more expensive.
With the help of X-rays from PETRA III, the researchers took a closer look at the possible wear processes. To create realistic conditions, the experts immersed a thin layer of iridium oxide in an electrolyte and applied an electric current. “Then we used the focused X-ray beam at the beamline P21.2 to observe what happened over several hours,” explains co-author Tim Weber from the University of Gießen. “Based on the measurement data, we were able to precisely record whether and how the thickness and roughness of the layer changed.” The electrolyte can be easily penetrated by the X-ray beam, and the measurement method is so fast that even rapid structural changes could be monitored.
The iridium oxide layers examined in the study had a particularly good and uniform quality, because they were produced with a high-precision process by the team of Herbert Over at the University of Giessen. “The five-nanometre-thick layer remained practically constant during our measurements,” says co-author Vedran Vonk from the DESY NanoLab. “Neither the thickness nor the crystal structure changed appreciably.” These results provide industry with an important clue: the better and more uniform the coating with iridium oxide, the more stable and durable the anodes and the more economically the electrolysers can operate in the long term. “Only if we manage to understand the corrosion processes on an atomic scale will we also have the opportunity to look for materials that can replace iridium,” says Over, who led the study. The present results are an important step in this direction.
Original publication
T. Weber, V. Vonk, D. Escalera-López, G. Abbondanza, A. Larsson, V. Koller, M.J.S. Abb, Z. Hegedüs, T. Bäcker, U. Lienert, G.S. Harlow, A. Stierle, S. Cherevko, E. Lundgren, H. Over; "Operando Stability Studies of Ultrathin Single-Crystalline IrO2(110) Films under Acidic Oxygen Evolution Reaction Conditions"; ACS Catalysis; 2021
Original publication
T. Weber, V. Vonk, D. Escalera-López, G. Abbondanza, A. Larsson, V. Koller, M.J.S. Abb, Z. Hegedüs, T. Bäcker, U. Lienert, G.S. Harlow, A. Stierle, S. Cherevko, E. Lundgren, H. Over; "Operando Stability Studies of Ultrathin Single-Crystalline IrO2(110) Films under Acidic Oxygen Evolution Reaction Conditions"; ACS Catalysis; 2021
Topics
Organizations
Other news from the department science
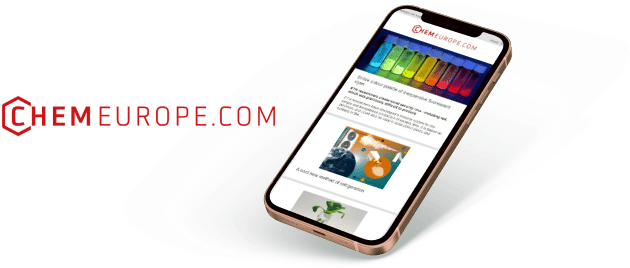
Get the chemical industry in your inbox
By submitting this form you agree that LUMITOS AG will send you the newsletter(s) selected above by email. Your data will not be passed on to third parties. Your data will be stored and processed in accordance with our data protection regulations. LUMITOS may contact you by email for the purpose of advertising or market and opinion surveys. You can revoke your consent at any time without giving reasons to LUMITOS AG, Ernst-Augustin-Str. 2, 12489 Berlin, Germany or by e-mail at revoke@lumitos.com with effect for the future. In addition, each email contains a link to unsubscribe from the corresponding newsletter.