Electronics integrated in plastic becomes more sustainable
Recyclability by Design
The idea of sustainability has now found its way into developing and producing innovative products. Innovation no longer only means faster, better, cheaper, but also cleaner, more energy-efficient, and more environmentally friendly, right through to enabling more efficient recycling. In the EU-funded ReIn-E project, which enters its second half in January 2022, INM - Leibniz Institute for New Materials (INM) is working with project partners from research and industry to develop materials and methods to make electronics embedded in plastic recyclable.

From material development to recycling: electronics integrated in plastic
INM
Modern applications of electronics require ever further miniaturisation. This affects not only the electronics themselves but also their combination with the materials that hold and protect them. Conventional components are often too bulky and too inflexible. So, it is not surprising that the industry is increasingly turning to space-saving solutions. The idea of integrating the electronic elements directly into a carrier material or printing them on it is obvious. So-called in-mould and printed electronics technologies are economical, enable new designs, and save space, weight, and material.
These are the best prerequisites for their use in vehicles or household appliances, were it not for one serious disadvantage: it will be challenging to remove the electronics from the appliances again at the end of their life! Even with conventional metal-plastic components, material separation and subsequent recycling are difficult; with polymer-integrated electronics, it is almost impossible.
This is where ReIn-E comes in: The aim of the project is to develop designs and sustainable materials to enable the recycling of the components. At INM, the team led by Prof. Tobias Kraus is researching a layer that is applied between the polymer and the metal. This release layer must be such that it ensures optimum adhesion of the two components during the use of the device and enables the plastic and metal to be separated from each other again if necessary.
Tobias Kraus explains the research approach: "A solution of water and polyvinyl alcohol (PVA) is applied to the surface of a polymer substrate in which electroconductive materials are to be integrated. PVA is a water-soluble polymer and behaves similarly to table salt: it dissolves in the liquid and can be returned to its original solid state by heating and evaporating the water. By adding water, the PVA film becomes liquid again. In this way, the different materials of in-mould and printed electronics can first be connected via the PVA layer and then separated from each other again. So, when the device is no longer used, its components can be recycled separately."
In addition to the development of the release layer, INM is also working on the synthesis of special pastes and inks for printing electronic circuits, thus complementing the project tasks of the partners from Belgium and Germany: the Centre Terre et Pierre specialises in recycling processes for solid waste and electronic scrap and is developing methods for recovering the metals and polymers; the Hahn-Schickard-Gesellschaft für Angewandte Forschung is printing electronics and testing the performance and stability of the printed and integrated materials and structures; and finally, the Sirris Technology Research Centre will manufacture the integrated components based on the designs and materials developed.
A special feature of the ReIn-E project is the involvement of small and medium-sized enterprises (SMEs), which could play a key role in the sustainable transformation of electronics manufacturing. They are to be enabled to help shape and profit from the transition from conventional technology to integrated electronics.
Most read news
Other news from the department science
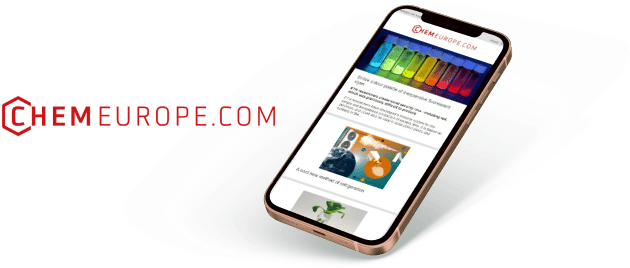
Get the chemical industry in your inbox
By submitting this form you agree that LUMITOS AG will send you the newsletter(s) selected above by email. Your data will not be passed on to third parties. Your data will be stored and processed in accordance with our data protection regulations. LUMITOS may contact you by email for the purpose of advertising or market and opinion surveys. You can revoke your consent at any time without giving reasons to LUMITOS AG, Ernst-Augustin-Str. 2, 12489 Berlin, Germany or by e-mail at revoke@lumitos.com with effect for the future. In addition, each email contains a link to unsubscribe from the corresponding newsletter.