Creating solar cells and glass from wood – or a billion tons of biowaste
Researchers map out how biomass from plants could replace unrenewable resources in optical applications
A digital, urbanised world consumes huge amounts of raw materials that could hardly be called environmentally friendly. One promising solution may be found in renewable raw materials, according to research published in Advanced Materials. In their paper, the international research group has taken a close look at how lignocellulose — or plant biomass — can be used for optical applications, potentially replacing commonly used materials like sand and plastics.
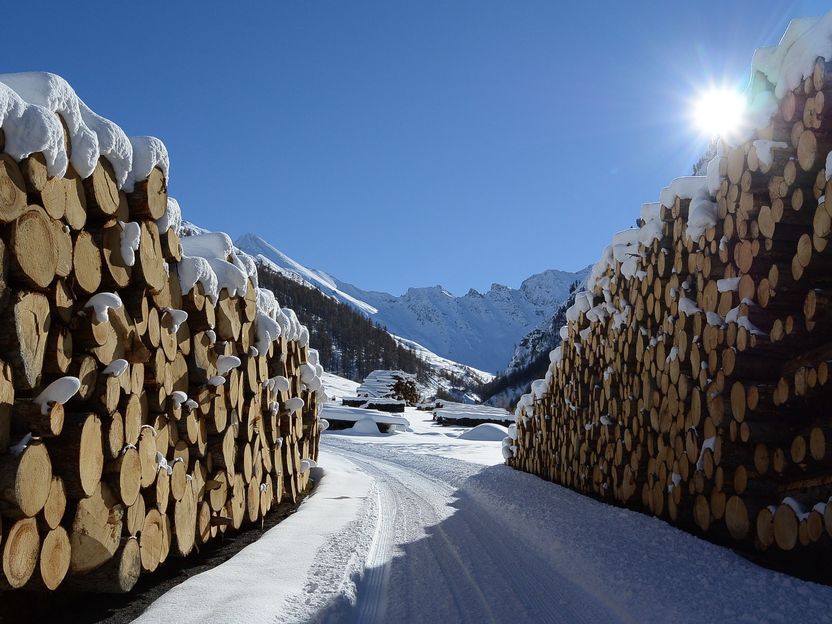
Symbolic image
pixabay.com
‘We wanted to map out as comprehensively as possible how lignocellulose could replace the unrenewable resources found in widely used technology, like smart devices or solar cells,’ says Jaana Vapaavuori, assistant professor of functional materials at Aalto University, who carried out the analysis with colleagues at the University of Turku, RISE – Research Institute of Sweden, and University of British Columbia.
Lignocellulose, the term that encompasses cellulose, hemicellulose and lignin, is found in nearly every plant on Earth. When scientists break it down into very small parts and put it back together, they can create totally new, usable materials.
In their extensive review of the field, the researchers assessed the various manufacturing processes and characteristics needed for optical applications, for example, transparency, reflectiveness, UV-light filtering, as well as structural colours.
‘Through combining properties of lignocellulose, we could create light-reactive surfaces for windows or materials that react to certain chemicals or steam. We could even make UV protectors that soak up radiation, acting like a sunblock on surfaces,’ explains Vapaavuori.
‘We can actually add functionalities to lignocellulose and customise it more easily than glass. For instance, if we could replace the glass in solar cells with lignocellulose, we could improve light absorption and achieve better operating efficiency,’ says Kati Miettunen, professor of materials engineering at the University of Turku.
Because forest biomass is already in high demand and vast carbon sinks are crucial to the health of the planet, as a source of lignocellulose the researchers point to what’s not being used: more than a billion tons of biomass waste created by industry and agriculture each year.
‘There is massive untapped potential in the leftovers of lignocellulose from other industries,’ Vapaavuori emphasises.
For now, researchers are still studying bio-based materials and creating prototypes. At Aalto University, for example, scientists have developed light fibres and light-reactive fabrics.
Vapaavuori says that the leap to scaling-up and commercialisation could be achieved in two ways.
‘Either we create new uses for bio-based waste through government regulations or research brings about such cool demos and breakthroughs that it drives demand for renewable alternatives for optical applications. We believe that we need both political direction and solid research.’
A major obstacle in the development and commercialisation of lignocellulose-based innovations has been its manufacturing cost. Eyes were on nanocellulose already at the beginning of the 2000s but it’s only now that the energy consumption and cost of production have dropped enough to make industrial use possible. Another ongoing challenge lies in a simple but fundamental ingredient of processing: water.
‘Cellulose loves water. To use it in optical applications, we need to find a way make it stable in humid conditions,’ says Vapaavuori.
Original publication
Other news from the department science
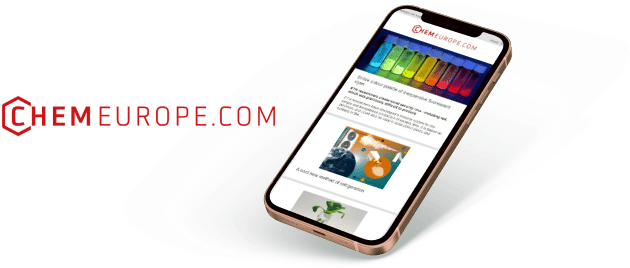
Get the chemical industry in your inbox
By submitting this form you agree that LUMITOS AG will send you the newsletter(s) selected above by email. Your data will not be passed on to third parties. Your data will be stored and processed in accordance with our data protection regulations. LUMITOS may contact you by email for the purpose of advertising or market and opinion surveys. You can revoke your consent at any time without giving reasons to LUMITOS AG, Ernst-Augustin-Str. 2, 12489 Berlin, Germany or by e-mail at revoke@lumitos.com with effect for the future. In addition, each email contains a link to unsubscribe from the corresponding newsletter.
Most read news
More news from our other portals
Last viewed contents
Jakob_Böhme
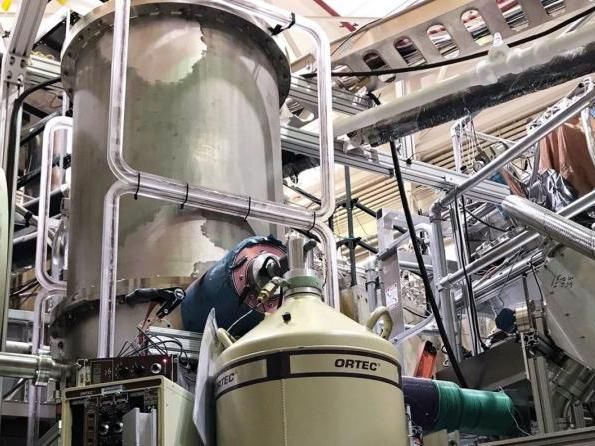