Melting glasses from unmeltable compounds
Chemists at the University of Jena are developing a way of melting normally unmeltable metal-organic framework compounds – so-called MOFs. This allows the melt-based production of glass components for applications in energy and environmental technology.
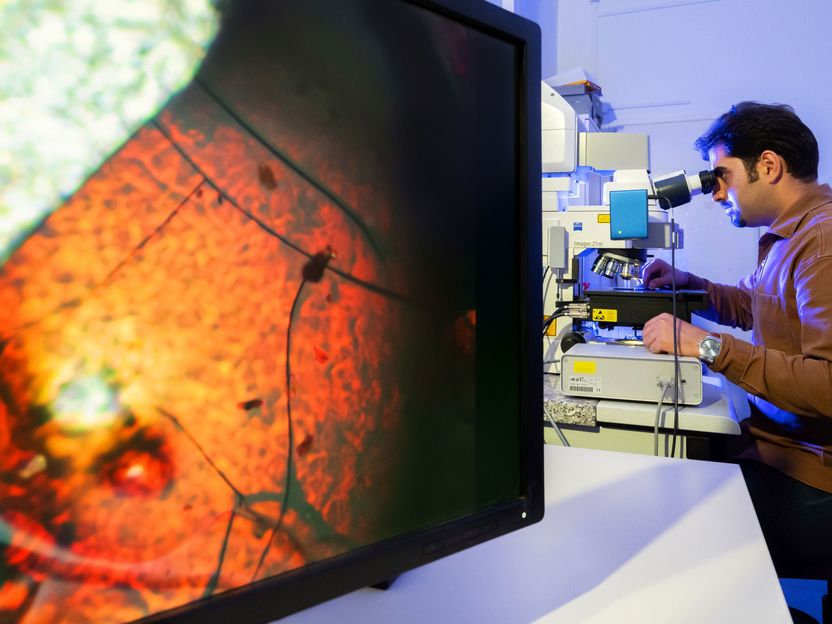
Vahid Nozari at the University of Jena uses a microscope to examine the new synthetic glass, which consists of a non-fusible metal-organic framework (MOF) compound.
Jens Meyer/Uni Jena
Glasses are an indispensable part of everyday life. One of the most important reasons for this is that glass objects can be manufactured almost universally and inexpensively in a wide variety of shapes and sizes using their corresponding melts. Processing in the (viscous) liquid phase offers a versatility that can hardly be achieved with other materials. However, this presupposes that the material from which the glass is made in terms of its chemical composition can be melted at all.
So-called metal-organic framework compounds – in short MOFs – have attracted a great deal of interest in recent years. Due to their special properties, they are considered to have great potential for future applications in energy and environmental technology, but also as sensor components and in the bio and life sciences. For example, MOFs can be used as starting materials for filter membranes for separating gases in technical combustion processes or for water treatment. The basis for the multitude of possible applications is above all one outstanding property of MOFs: their high and largely controllable porosity. MOF substances consist of inorganic particles that are connected by organic molecules to form a network of pores. As MOFs are predominantly in powder form, a primary challenge of the field is to produce bulk components. This is where glasses come into play.
Trade-off between properties and processability
But apart from a few exceptions, the porosity of all things prevents the materials from being meltable and, thus, processable into components of the desired shape. Chemists from the Friedrich Schiller University in Jena, Germany, and the University of Cambridge, United Kingdom, have now found a solution to this problem. They report on their research results in the current issue of "Nature Communications".
In order to produce components for industrial applications from MOFs, they can be processed into so-called hybrid glasses, for example. To do this, however, you have to melt them down - a process that is not straightforward in this specific case. So far, only a handful of candidates of this class of substances have actually been demonstrated to be meltable. "In most known MOF materials, the high porosity is one of the reasons that – upon heating – they thermally decompose before reaching their melting point, that is, they burn," explains Vahid Nozari, doctoral student at the Laboratory of Glass Science of the University of Jena. It is precisely the property that makes these materials so interesting that also prevents them from being processed using the glass route.
Identifying combinations of ionic liquids, MOF matrices and melting conditions
So how do you make a non-meltable material meltable in order to shape and process it in its liquid state? The team led by Jena professor Lothar Wondraczek has now found an answer to this question. “We filled the pores with an ionic liquid that stabilizes the inner surface in such a way that the substance can finally melt before it even decomposes,” explains Wondraczek. The researchers were able to show how normally non-meltable substances from the MOF family of zeolitic imidazolate frameworks (ZIFs) can actually be converted into a liquid state and, finally, a glass. “In this way, the desired component can be obtained, for example, in the form of a membrane or a disk. Residues of the employed ionic liquid can then be washed out after shaping."
The key to future applications are the interactions taking place between the ionic liquid and the MOF material. These determine the reversibility of the process, i.e., the possibility of washing out the auxiliary liquid after the melting process. If the reactions are not adapted, either the pore surface is not adequately stabilized or there is an irreversible chemical bond between the MOF and parts of the ionic liquid. Therefore, ideal combinations of liquids, matrix materials and melting conditions must be identified with a view to the desired application, so that large-volume objects would become possible.
Original publication
Other news from the department science
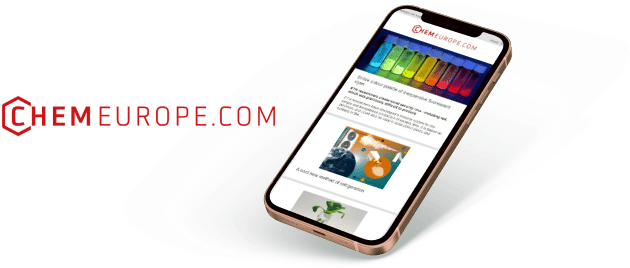
Get the chemical industry in your inbox
By submitting this form you agree that LUMITOS AG will send you the newsletter(s) selected above by email. Your data will not be passed on to third parties. Your data will be stored and processed in accordance with our data protection regulations. LUMITOS may contact you by email for the purpose of advertising or market and opinion surveys. You can revoke your consent at any time without giving reasons to LUMITOS AG, Ernst-Augustin-Str. 2, 12489 Berlin, Germany or by e-mail at revoke@lumitos.com with effect for the future. In addition, each email contains a link to unsubscribe from the corresponding newsletter.
Most read news
More news from our other portals
Last viewed contents
Research and Markets: Global chemical industry 2013 - new challenges being created for an already highly regulated industry

LAUDA appoints Dr. Ralf Hermann as the new General Manager Constant temperature equipment

Turning polymer films into self-sensing high-tech actuators
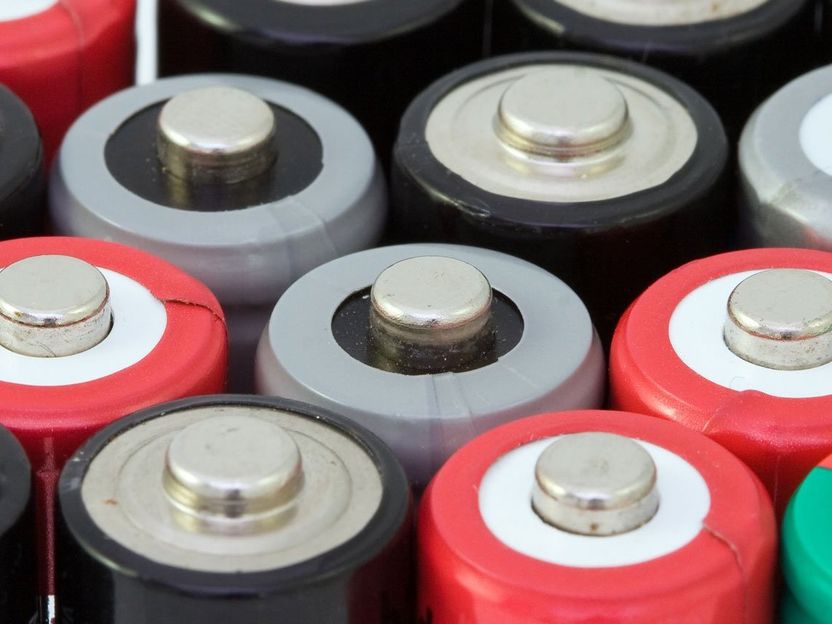
BASF to build new battery recycling prototype plant in Schwarzheide, Germany - Use of innovative technology for extracting lithium, nickel, cobalt and manganese from end-of-life lithium-ion batteries and production scrap
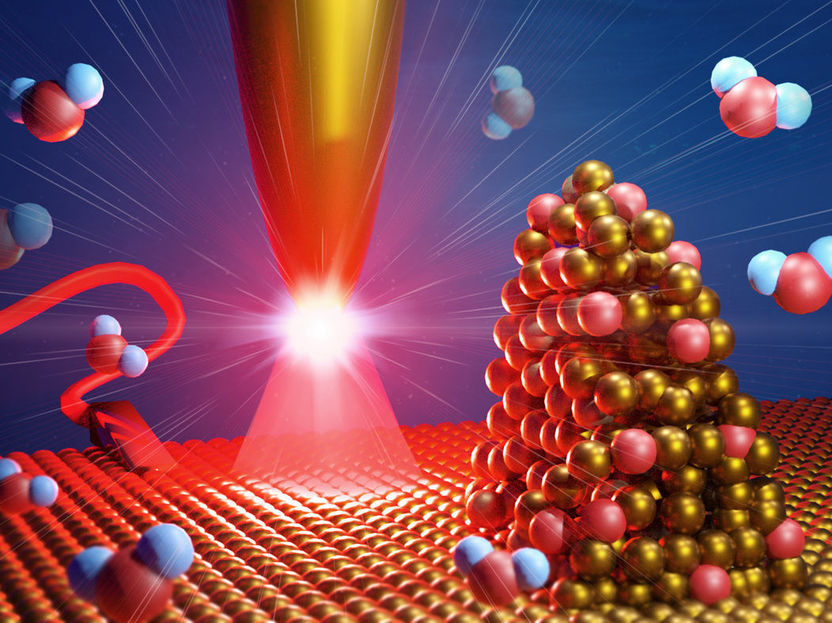
Water splitting observed on the nanometer scale - New method provides fundamental insights into electrocatalytic water splitting under operating conditions
Sigma-Aldrich Sells Majority of Diagnostics' Chemistry Product Line
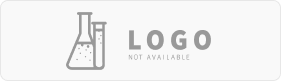