Eco-friendly process for synthesizing organic materials developed for high-performance materials industry
Green production with 25 percent initial cost savings
Until now, the production of materials from organic substances was only possible with the use of highly toxic solvents. A team led by Uni Konstanz Prof. and CeMM Adjunct PI Miriam Unterlass has now developed a method for making organic substances suitable for use as high-performance materials in an eco-friendly and completely non-toxic way by generating them in only hot water. The study represents an important milestone in the green production of organic materials and thus also provides an important incentive to switch from inorganic to organic, renewable materials. Beside that the method is environmentally friendly, cost-effective, easy to use and also reduces the weight of the products.
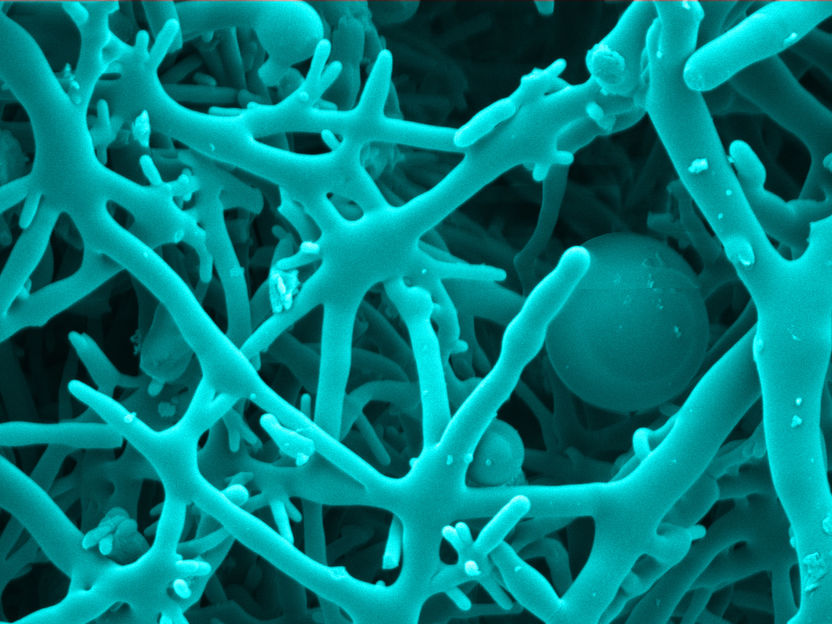
Colored microscopy image of the monolith
Lahnsteiner M., Unterlass M
Many of the products we use every day, such as rechargeable batteries and electronic materials, are made using inorganic substances - substances that are gradually becoming rarer on our planet. Chemists are looking for ways to replace inorganic materials with organic materials made of carbon, nitrogen, hydrogen or oxygen. To make these substances usable for the desired applications, highly toxic chemicals, so-called solvents, are still used today. This is precisely the problem that chemist Miriam Unterlass, Professor at the University of Konstanz and Adjunct Principal Investigator at the CeMM Research Center for Molecular Medicine of the Austrian Academy of Sciences, is addressing in her current study as part of her FWF START project. She explains, "Organic materials have many positive characteristics: they can be obtained from renewable raw materials, are environmentally friendly and, above all, are extremely lightweight. With our process, we can now also produce them and make them usable completely free of toxic solvents, very simply and inexpensively. In our current study, we have focused on the production of particularly porous materials that are needed for the manufacture of high-performance materials, especially in industry, for example for filter systems, membranes for fuel cells, but also for insulation in electronics."
The connection with water
While inorganic substances such as salts are soluble in water, organic substances are apolar and do not dissolve with water in a conventional state. For their new method, study author Marianne Lahnsteiner, a PhD student in Unterlass' research group at CeMM, and project leader Miriam Unterlass heated water and found that it also changed its ability in the process. "By heating molecules containing only oxygen, hydrogen, nitrogen, and carbon in water between 180 and 250 degrees and under pressure, these molecules can bind. Depending on the temperature and duration of this process, we thus achieve different structures, which we have been able to explore in detail in hundreds of experiments," Unterlass said, "so we now know exactly which structures are created by which, at which temperature and processing time. The materials in our study were specifically developed as high-performance materials and are accordingly particularly temperature-stable and robust."
Screening, filtering, conducting
In one gram of the material produced by Lahnsteiner and Unterlass, there are an enormous 7250 mm3 of hollow space. Accordingly, it offers - depending on its shape - the perfect characteristics for filtering, seprarting and conducting molecules, and that at low weight. To make the structures created by the process more observable, the researchers collaborated with the research group of network scientist Jörg Menche, a professor at the University of Vienna and also an adjunct principal investigator at CeMM. Menche's research group used Artificial Intelligence to analyze the emerging structures and patterns based on the microscopy images. "With the help of Artificial Intelligence, we were able to quickly categorize a variety of emergent structures in a way that we know how to synthetically achieve these structures," Lahnsteiner said.
Green production with 25 percent initial cost savings
"Smog is a key sign of environmental pollution. Chemical processes are unfortunately partly responsible for its formation, through the use of toxic solvents. With our new method, we are creating an enormously important alternative for processing organic materials that does not require such toxic solvents at all. At the same time, very common elements are used instead of rare ones," Unterlass said. "In addition, the process is very cost-effective. Using water versus toxic solvents in the production of porous materials saves about 25 percent of the cost. And we don't produce pollutants."
Original publication
Other news from the department science
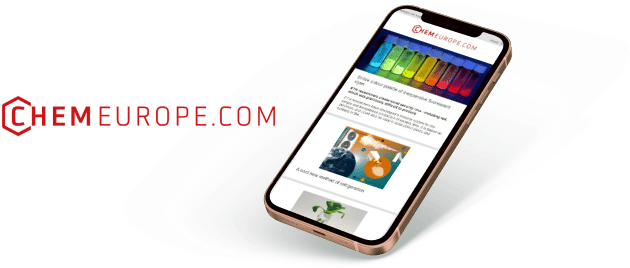
Get the chemical industry in your inbox
By submitting this form you agree that LUMITOS AG will send you the newsletter(s) selected above by email. Your data will not be passed on to third parties. Your data will be stored and processed in accordance with our data protection regulations. LUMITOS may contact you by email for the purpose of advertising or market and opinion surveys. You can revoke your consent at any time without giving reasons to LUMITOS AG, Ernst-Augustin-Str. 2, 12489 Berlin, Germany or by e-mail at revoke@lumitos.com with effect for the future. In addition, each email contains a link to unsubscribe from the corresponding newsletter.
Most read news
More news from our other portals
Last viewed contents
Cheap, simple and efficient molybdenum carbide electrocatalysts for hydrogen production
Ocean Optics Spectrometers Head to Mars
Opisthorchis_viverrini
BASF, Cargill and Novozymes achieve milestone in bio-based acrylic acid process - Success in producing 3-hydroxypropionic acid for bio-based acrylic acid
WACKER stops short-time work at Burghausen’s polysilicon manufacturing facilities
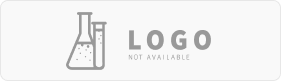
Turbo Components& Engineering - Houston, USA
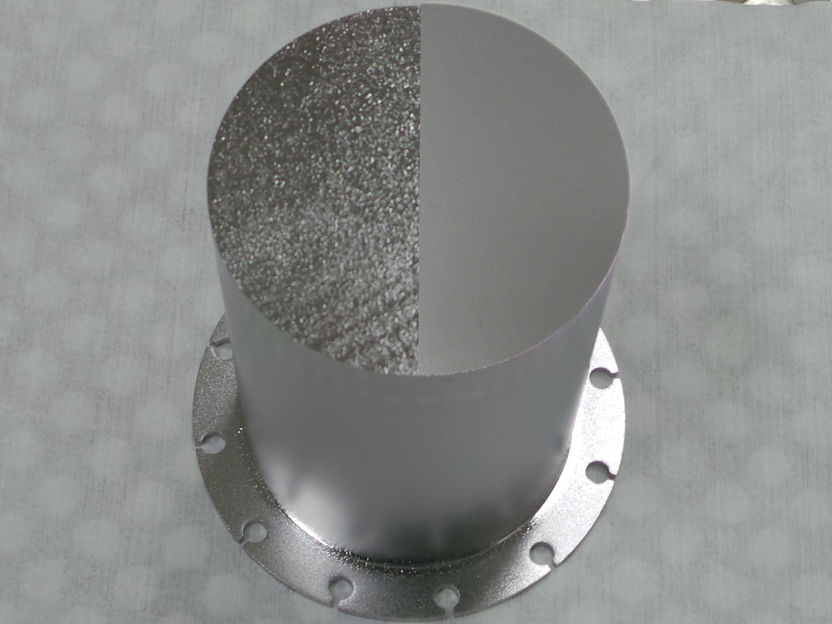
Alternative material investigated for superconducting radio-frequency cavity resonators
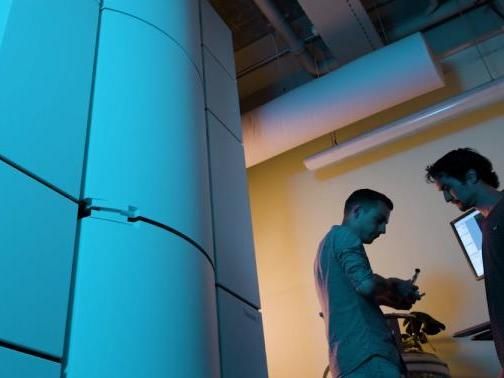