How cola still tingles after a year
A few nanometers of thin quartz-like coatings can multiply the shelf life of food, enable brilliant OLED TV pictures or separate gases from each other
If polymers are specifically made to form and deposit on the surfaces surrounding the plasma, they can be coated in a targeted manner. Thanks to this so-called Plasma Enhanced Chemical Vapor Deposition, or PECVD for short, it is possible, for example, to apply ultra-thin, gas-tight coatings to the inside of PET bottles, ensuring that the contents last longer, or to protect organic light-emitting diodes (OLEDs) from moisture so that the TV screens work for a long time. The Teams of General Electrical Engineering and Plasma Technology and Experimental Physics II of Ruhr-Universität Bochum (RUB) have perfected this technique. They report in Rubin, the RUB’s science magazine.
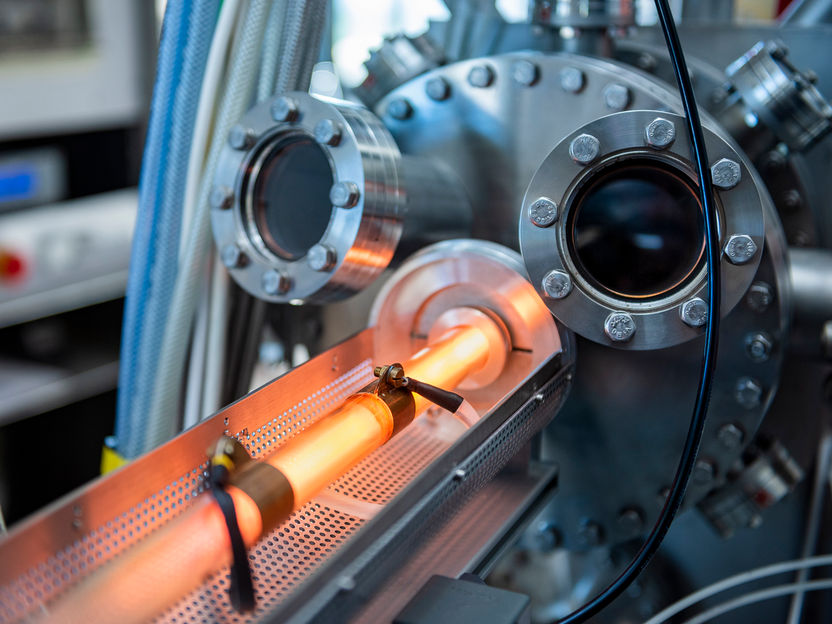
A capacitively coupled plasma source (CCP) for the generation of nanoparticles. The nanoparticles are embedded in composite layers for filter membranes to control selectivity for different gases.
Damian Gorczany
Making milk and medicines last longer
The deposition is only possible because the plasmas are cold and thus do not damage the PET bottle or other surfaces to be coated with heat. Only the fast electrons in the plasma are hot, and they do not damage the surfaces. The glass-like coating of the plastic, which is only 20 to 30 nanometres thin, ensures that 10 to 100 times less gas escapes through the bottle. This extends the shelf life of a soda pop from the previous four weeks to about a year. The method is also of interest for the packaging of milk and other foods, as well as medicines and even microelectronic components. “This type of coating is also environmentally friendly, because the tiny amount of material can simply be neglected during recycling,” explains Dr. Marc Böke from the Experimental Physics II department at RUB.
Oxygen tips the scales
The challenge lies in controlling the formation of the layers. “The layers should not only be ultra-thin, but also absolutely dense, gap-free and uniform,” explains Marc Böke. The adjusting screws for this are manifold. For one thing, it depends on the gas mixture. Atomic Oxygen is a particularly important player. The pressure at which the plasma is operated is also significant. Similarly, the geometry of the reactor and the choice of energy source influence what happens in the plasma and how it affects the surrounding surfaces. For example, an appropriate plasma can be ignited by microwaves, but also by inductively or capacitively coupled radio frequency. “In general, different sizes of plasma reactor are possible, up to the huge dimensions needed to coat entire window panes for high-rise buildings,” says Professor Peter Awakowicz, holder of the chair for Electrical Engineering and Plasma Technology.
Measurement techniques had to be developed
The researchers have gradually been able to fathom and perfect many aspects of the possible processes. For example, PET bottles are cleaned and activated before coating, also by means of plasma. But here, too, the surface of the bottle changes, which in turn influences the subsequent coating. Measurements of the particle flows during cleaning revealed what happens in the process. If all these aspects are taken into account during cleaning and the process is run optimally, this has a considerable influence on the success of the subsequent coating: “We were able to increase the impermeability, which was initially a factor of 100 (depending on the substrate material), to a factor of 500 through the correct setting of the previous cleaning,” says Peter Awakowicz.
The latest application, which is currently being worked on, makes a virtue out of necessity: if one actually wishes for layers that are as dense and defect-free as possible, defects such as tiny pores in the coating are almost impossible to avoid. They allow the research teams to use plasma coating to develop non-swelling filter membranes that exhibit previously unknown properties. They can desalinate water or separate gases from each other, such as oxygen from CO2.
Most read news
Other news from the department science
These products might interest you
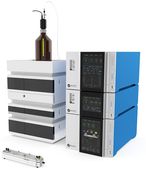
Eclipse by Wyatt Technology
FFF-MALS system for separation and characterization of macromolecules and nanoparticles
The latest and most innovative FFF system designed for highest usability, robustness and data quality
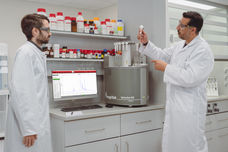
Spinsolve Benchtop NMR by Magritek
Spinsolve Benchtop NMR
Spinsolve is a revolutionary multinuclear NMR spectrometer that provides the best performance

HYPERION II by Bruker
FT-IR and IR laser imaging (QCL) microscope for research and development
Analyze macroscopic samples with microscopic resolution (5 µm) in seconds
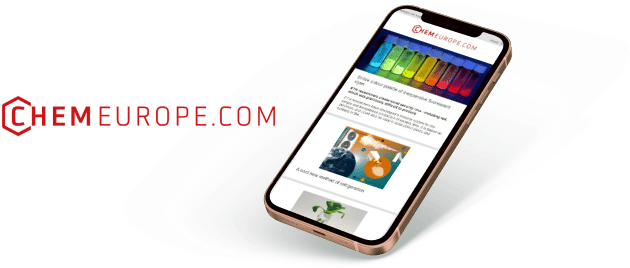
Get the chemical industry in your inbox
By submitting this form you agree that LUMITOS AG will send you the newsletter(s) selected above by email. Your data will not be passed on to third parties. Your data will be stored and processed in accordance with our data protection regulations. LUMITOS may contact you by email for the purpose of advertising or market and opinion surveys. You can revoke your consent at any time without giving reasons to LUMITOS AG, Ernst-Augustin-Str. 2, 12489 Berlin, Germany or by e-mail at revoke@lumitos.com with effect for the future. In addition, each email contains a link to unsubscribe from the corresponding newsletter.