Ecofriendly plastic alternative: Scraps to synthetics
No petroleum-based synthetic components needed
A new type of plastic made of reclaimed waste readily degrades in less than a year. The substance that will soon serve to manufacture and break down mainly disposable products in an ecofriendly way goes by the name of polyhydroxybutyrate. This material can be produced on an industrial scale in a new process developed by the Fraunhofer Institute for Production Systems and Design Technology IPK and its partners.
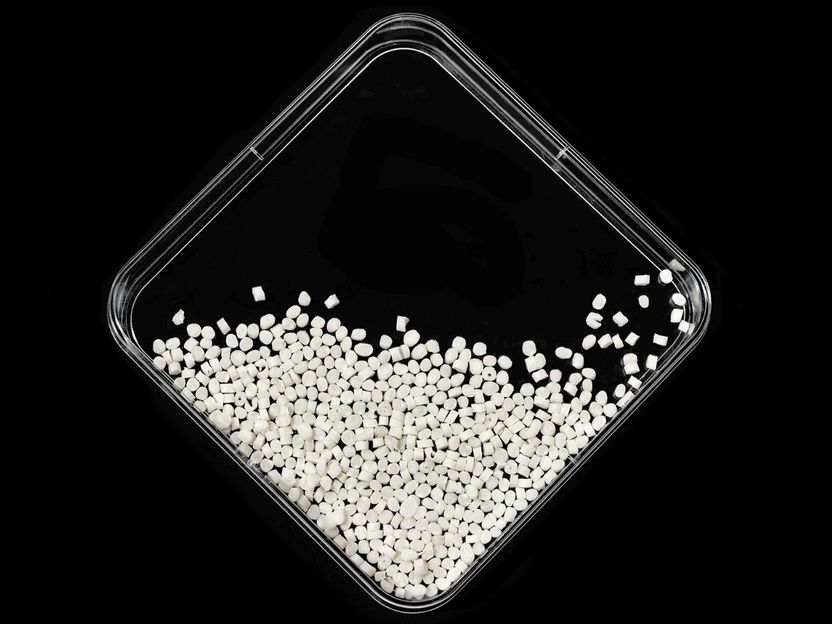
Compounded and granulated polyhydroxybutyrate (PHB).
© Fraunhofer IPK/Andy King
Everyday life devoid of plastics – that would be hard to imagine. They figure prominently in packaging and consumer goods, and are indispensable to industry applications such as automotive and medical engineering. Reuse and recycling of plastics from fossil resources is hardly common practice. On top of that, they degrade at a glacial pace and pollute the environment for a long time to come. The great patches of plastic waste floating on our oceans attest to their power to pollute. Plastic bottles and bags despoil beaches and, in many places, entire stretches of land.
The Bioeconomy International research initiative
The need for global recycling strategies is urgent, given plastics’ heavy use all over the world. More and more governments are resorting to bans to curb the swelling tide of plastic waste. A viable option to replace fossil-based plastics on a large scale has yet to be found. This is why the German Federal Ministry of Education and Research (BMBF) launched the “Bioökonomie International” (Bioeconomy International) research initiative in close cooperation with Fraunhofer IPK, the Department of Bioprocess Technology of the Technical University of Berlin, regional industrial partners and international research partners from Malaysia, Columbia and the USA. These researchers are developing a method of manufacturing polymers without drawing on premium resources such as mineral, palm and rapeseed oils, the production of which is very detrimental to the environment.
A new plastic much like polypropylene
This new process turn industrial leftovers such as waste fats that contain a lot of mineral residue into polyhydroxybutyrate (PHB). Microorganisms can metabolize these residues in special fermentation processes. They deposit the PHB in their cells to store energy. “Once the plastic has been dissolved from the cell, it is still not ready for industrial use, because the hardening process takes far too long,“ says Christoph Hein, head of the Microproduction Technology department at Fraunhofer IPK. The raw material has to be mixed with chemical additives downstream in post-production stages. For example, the research team adjusted the plasticizing and processing parameters to trim the recrystallization time to fit the timing of industrial processing. The resultung biopolymer's properties resemble those of polypropylene. But unlike PP, this plastic degrades fully in six to twelve months.
In this method of producing plastic, microorganisms synthesize the entire polymer in a biotechnical process. “To this end, we convert biogenic residues such as waste fats into polyesters that can be put to technical use,” says Hein. The researcher and his team opted for microorganisms, genetically modified with molecular methods, to serve as biocatalysts. With the help of chemical purification processes and an extensively optimized material, they have been able to develop a novel family of materials that
satisfy the demands of technical plastics.
No petroleum-based synthetic components needed
The new process not only dispenses with petroleum-based synthetic components altogether; it also enables green plastic alternatives. Naturally occurring microorganisms can break down these newly developed plastics, so they need not be subjected to the special conditions that serve to degrade matter in industrial composting plants. They offer an ecofriendly alternative to making and degrading single-use products and other disposable items.
The process also lends itself to producing high-quality plastic parts for certain technical applications and periods of use. The specifications for this sort of product are more demanding. They may have to exhibit specific geometric tolerances and surface qualities or be reproducible with great precision. The researchers developed highly specialized replication processes to meet these requirements.
Topics
Organizations
Other news from the department science
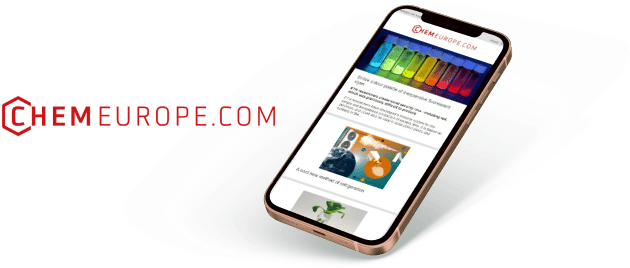
Get the chemical industry in your inbox
By submitting this form you agree that LUMITOS AG will send you the newsletter(s) selected above by email. Your data will not be passed on to third parties. Your data will be stored and processed in accordance with our data protection regulations. LUMITOS may contact you by email for the purpose of advertising or market and opinion surveys. You can revoke your consent at any time without giving reasons to LUMITOS AG, Ernst-Augustin-Str. 2, 12489 Berlin, Germany or by e-mail at revoke@lumitos.com with effect for the future. In addition, each email contains a link to unsubscribe from the corresponding newsletter.
Most read news
More news from our other portals
Last viewed contents
Ethambutol
Super_hydrophilicity
Maitland_Jones,_Jr
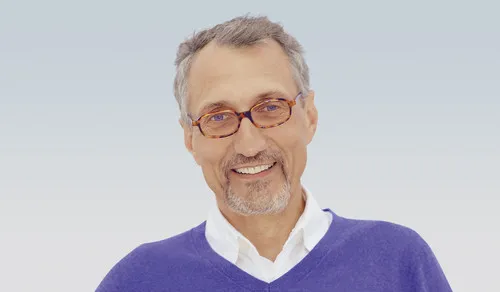