Evonik wants to make green hydrogen more affordable
Polymer chemistry is the key to efficient electrolysis
Green hydrogen is a beacon of hope in the energy transition, both as a carbon-free fuel for industry and transportation, and as a key raw material for the chemical industry. Green hydrogen is produced from water by electrolysis using electricity generated from renewable resources. It is still much more expensive than conventional hydrogen, which is generally obtained from methane gas in a process that releases carbon dioxide. As well as sufficient low-cost electricity generated from renewables, investment in the electrolyzer is a key factor in cost-efficient production of green hydrogen.
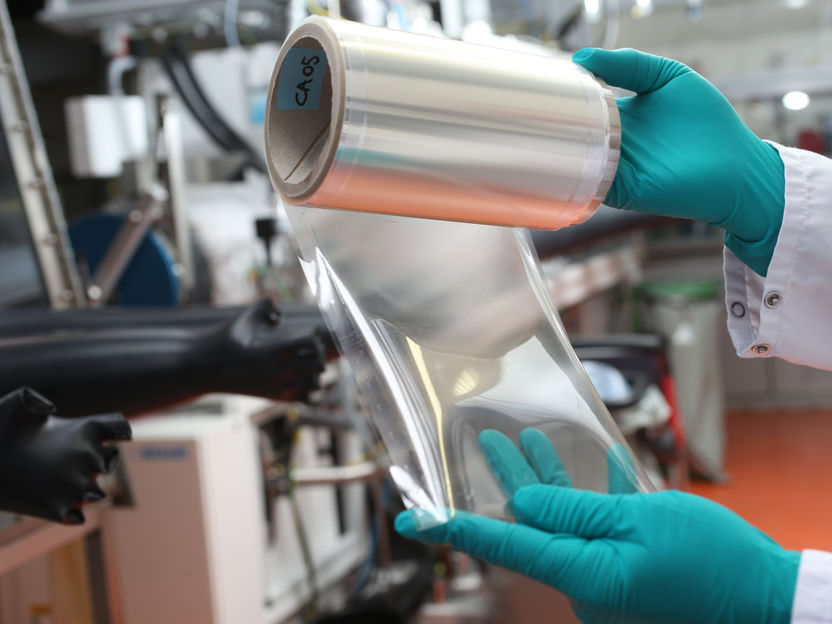
The central component of the electrolyzer, which has a major influence on efficiency and reliability, is an ion-conducting membrane. Evonik has now developed a novel anion exchange membrane (AEM), which should contribute to the breakthrough of electrolytic production of hydrogen.
Evonik
The central component of the electrolyzer, which has a major influence on efficiency and reliability, is an ion-conducting membrane. Evonik has now developed a novel anion exchange membrane (AEM), which should contribute to the breakthrough of electrolytic production of hydrogen. “Our membrane could allow commercial realization of highly efficient and economically viable electrolysis technology,” says Oliver Conradi, who is responsible for membrane research at Creavis, Evonik's strategic innovation unit.
The membrane developed by researchers at Creavis and experts from the High Performance Polymers unit in the Membranes innovation growth field comprises a resistant polymer with excellent conductivity. Conradi: “The polymer chemistry behind this membrane is the key to efficient electrolysis. And we now hold that key.”
Electrolysis with anion exchange membranes has clear benefits compared with other electrolytic processes such as conventional alkaline electrolysis using diaphragms (AEL) or the more recent method of proton exchange membrane electrolysis (PEM) which is highly dependent on raw materials such as precious metals. The innovative AEM concept reduces investment costs because the cells used for electrolysis in alkaline conditions do not require precious metals. Therefore, far less expensive materials can be used. Other attributes of this AEM electrolysis platform are high current density, very good efficiency, and high flexibility.
In the CHANNEL project, a consortium of highly qualified partners from industry and research organizations will plan, construct, and test an AEM electrolysis system based on the new membranes from Evonik. CHANNEL stands for Cost-efficient Hydrogen production unit based on ANionN exchange membrane Electrolysis. The project will run for three years and will receive funding of around €2 million from the European Union’s Horizon 2020 research program. In addition to Evonik, which is providing the AEM membrane, the other project partners are Shell (Netherlands; hydrogen user), Enapter (Italy; plant engineer for the electrolyzer), Forschungszentrum Jülich (Germany; R&D on membrane-electrode assemblies), the Norwegian University of Science and Technology (NTNU; catalysts), and SINTEF, an independent research organization in Norway, which is responsible for project coordination. The consortium therefore covers the entire value chain for the production of green hydrogen.
Topics
Organizations
Other news from the department science
These products might interest you
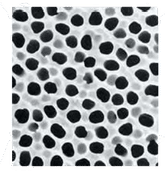
Anopore™ by Cytiva
Precise filtration made easy with Anopore inorganic membranes
The aluminum oxide filter membrane that can increase the purity or yield of your analyte
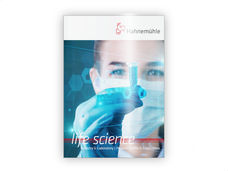
Hahnemühle LifeScience Catalogue Industry & Laboratory by Hahnemühle
Wide variety of Filter Papers for all Laboratory and Industrial Applications
Filtration Solutions in the Life Sciences, Chemical and Pharmaceutical Sectors
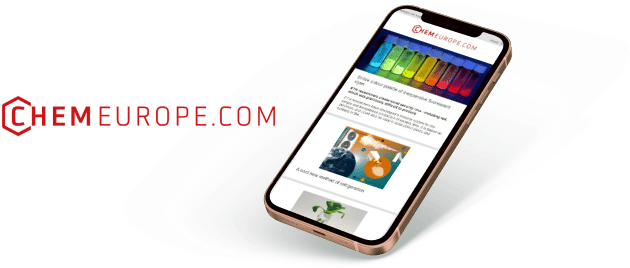
Get the chemical industry in your inbox
By submitting this form you agree that LUMITOS AG will send you the newsletter(s) selected above by email. Your data will not be passed on to third parties. Your data will be stored and processed in accordance with our data protection regulations. LUMITOS may contact you by email for the purpose of advertising or market and opinion surveys. You can revoke your consent at any time without giving reasons to LUMITOS AG, Ernst-Augustin-Str. 2, 12489 Berlin, Germany or by e-mail at revoke@lumitos.com with effect for the future. In addition, each email contains a link to unsubscribe from the corresponding newsletter.