Biofuel for ships
Diesel and gasoline sourced from renewables produces a lot less greenhouse gas
The combustion of conventional fossil fuels accounts for a large share of global CO2 emissions. A great deal of criticism is levelled against cruise and merchant ships for polluting the environment with sooty waste gas and toxic heavy fuels. Researchers at the Fraunhofer Institute for Environmental, Safety and Energy Technology UMSICHT in Oberhausen have been looking into alternative climate-friendly fuels. They are now able to produce a renewable biofuel that can be converted into gasoline, diesel and even Kerosene for aircraft. This synthetic fuel reduces greenhouse gas emissions by up to 30 percent compared to fossil fuel. It also produces less soot emissions.
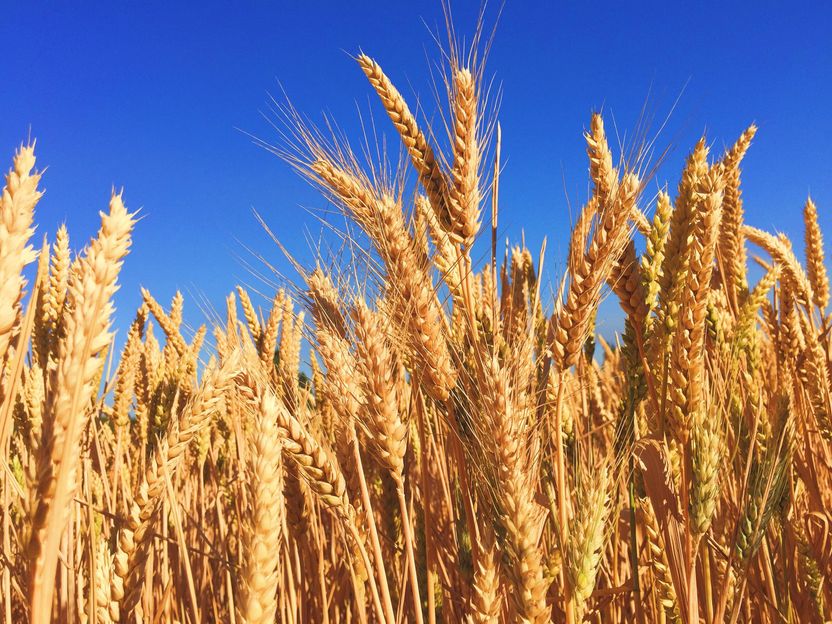
Researchers at Fraunhofer UMSICHT use bioethanol from wheat straw as fuel.
Photo by Melissa Askew on Unsplash
Ships are among the biggest climate sinners. Millions of tonnes of combusted marine diesel pollute the environment. The shipping industry is responsible for emitting around a billion metric tonnes of carbon dioxide worldwide each year. Dr. Andreas Menne, a mechanical engineer, and his colleagues at Fraunhofer UMSICHT in Oberhausen want to mitigate marine diesel’s adverse impact on the climate with a new technology. Menne, who heads up the Biorefinery and Biofuels department, and his team are producing synthetic diesel and gasoline made from renewable resources. To do so, they are converting bioethanol into diesel, gasoline or jet fuel that have nearly the same properties as fossil fuels. Renewables help slash the transportation sector’s CO2 emissions.
“Straw, leaves, sawdust, waste wood – we can use almost anything as the feedstock for bioethanol,” says Menne. The new climate-friendly biofuel produces a lot less greenhouse gas. Vehicles should be able to run on nothing but this fuel. By contrast, just five to ten percent of the E10 fuel is bioethanol; the rest is of fossil origin. “We’re not going to feel much of a climate effect with that,” says Menne. “Electric, hybrid and fuel-cell vehicles are not going to reduce greenhouse gas emissions as quickly as this has to happen. We need a holistic approach and a diversity of solutions for tomorrow’s fuels.” The pressure to take action is mounting with the revised Renewable Energies Directive (RED II) calling for advanced fuels to account for a share of 3.5 percent by 2030. The share of alternative fuels based on food crops is to be reduced by the same percentage.
Bioethanol made of wheat straw
The UMSICHT researchers are producing up to 20 liters of the new biofuel a week in an experimental plant. The feedstock is bioethanol sourced from wheat straw. “Actually, I could use any other alcohol,” says Menne. The straw alcohol initially retains its liquid form as it flows from the metal drum through the pipes of the test plant into a vaporizer. When the temperature reaches 350 degrees Celsius at a pressure of 20 bar, the gaseous alcohol flows into the heart of the plant, a tubular reactor. This reactor is filled with pieces of activated carbon coated with a newly developed catalyst material. These catalysts cause the gas to condense by forming bonds between individual carbon compounds. This produces gasoline, kerosene or diesel, depending on how many carbon molecules are combined. “A catalyst is often developed in the lab but may then turn out to be difficult to produce in large quantities. But we can buy the materials for this catalyst cheaply because it doesn’t consist of precious metals or rare earths. And most importantly, it remains stable over the long term,” says Menne.
The biofuel packs plenty of power, as researchers at the Fraunhofer Institute for Chemical Technology ICT in Pfinztal have confirmed. They put standard commercial engines on a test bench to run trials with the new fuel, rate engine power and measure waste gases with precision instruments. These readings were taken at different operating levels, during cold starts, under different loads and at varying engine speeds.
Tests confirm low waste gas emissions
These trials found the biofuel’s energy density to be slightly higher than that of conventional fuels. That means a vehicle with this new fuel in its tank would have a slight advantage in a real race. The synthetic fuel’s waste gas emissions were also a selling point with less carbon monoxide, carbon dioxide and hydrocarbons, and a lot less soot emanating from the exhaust. This biofuel’s physical properties come close to those of fossil diesel, so it can be made to comply with prevailing standards.
Venkat Aryan, a chemical engineer at Fraunhofer UMSICHT, has added up every molecule of the greenhouse gases in each process step to assess the ecological impact. A well-to-wheel analysis factors all greenhouse gases into the equation, from the extraction or harvesting of raw materials to the fuel’s conversion into kinetic energy. This includes crude oil extraction from underground wells, the cultivation of plants for biofuel and the waste gases. He found that the CO2 equivalents for synthetic diesel made from wheat straw amounted to 64.3 to 91.6 grams per megajoule, depending on the ethanol source. That is up to 32 percent less than the 94 grams for petroleum-based diesel.
Shipping companies can make their own biofuel
“Our fuel can be converted into gasoline, diesel or even kerosene for airplanes. But the latter is the most complicated,” says Menne. Marine diesel is a much simpler matter. It does not have to be processed in a refinery. “You could simply set up our plant in a port. Our process is so straightforward that shipping companies could produce their own diesel. Then the age of the big stinkers would soon be over,” says Menne.
The technology is ready to go to market. While the synthetic diesel is still more expensive than diesel made of petroleum, Menne is confident that this could soon change. As the new legislation takes effect, fossil fuels will no longer be as cheap to produce.