Temperature can regulate wetting properties of sprayed latex surfaces
Properties are essential for spray manufacturing and the printing industry
A Swedish-German research team has been using DESY’s X-ray source PETRA III to investigate how surface coatings can be made to attract or repel water using tailor-made latex nanoparticles. Being able to influence the wettability of surfaces during production is important in many applications, from the printing industry to polymer solar cells.
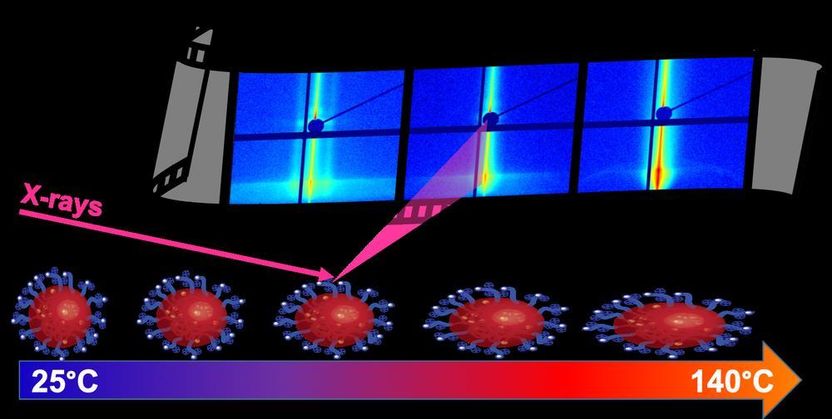
Latex nanoparticles deformed by heat are made visible by X-ray light
Advanced Functional Materials CC-BY 4.0
Most people are familiar with the phenomenon of water droplets immediately spreading out and wetting certain surfaces, while rolling off others, such as a lotus leaf or water-repellent functional clothing. The degree to which liquids form droplets and run off surfaces is described by the wettability of the surface, which is defined in terms of the angle between the boundary of the liquid and the surface, known as the contact angle. The larger the contact angle, the more water-repellent the surface. Dirt- and water-repellent paints are now available that exploit this so-called lotus effect.
Scientists are currently studying new types of polymer solar cells that can be manufactured by spraying thin layers of active materials made of nanoparticles onto a carrier film. The efficiency of such solar cells depends crucially on the individual layers being of a reliable thickness and load-bearing capacity. This in turn depends directly on the wettability of the substrate.
Working at PETRA III, the Swedish-German team has now found how to precisely adjust the wettability of sprayed surfaces through thermal annealing, a form of heat treatment. The scientists used so-called core-shell latex particles for their experiments. These are similar in structure to tiny chocolate truffles, consisting of a polymer core encased in smaller latex particles. The team used a special process to manufacture four different types of such nanoparticles: all the particles had the same outer shell, but two different synthetic polymers were used for the core. The scientists produced particles made of the two core polymers in two different sizes (30–40 nanometres and 80–100 nm). The size of the spheres also corresponds to their degree of polymerisation, a measure of the length of the polymer chains, which also describes the rigidity of the core.
The team sprayed very thin layers of the various different types of nanoparticles onto a silicon substrate and used X-rays from PETRA III to examine in real time how the nanostructure of the different latex particles was modified by heating these coatings. The temperature was varied in five steps from 20 up to 140 degrees Celsius. Following the annealing, for at least one hour, the surface structure of the samples was imaged using electron microscopes, and the contact angle of droplets resting on them was measured.
Above temperatures of about 70 degrees, the polymers reorganise themselves very distinctly and reproducibly, through expansion, domain formation, mixing and merging. This occurs particularly during the drying phase of the latex polymer coat, whereby the smaller nanoparticles and those with a short-chained, softer core, display more pronounced changes than the larger ones with rigid cores. Once they have dried completely, they remain stable even when treated for prolonged periods at temperatures of over 100 degrees. The scientists believe that this is a result of the mobility of the molecules in the liquid phase.
“We want to fine-tune the hydrophilic properties of the surfaces through thermal annealing, but also optimize the type and size of the latex particles for applications involving specific working temperatures,” says DESY’s Stephan Roth, who is in charge of PETRA’s P03 beamline. This type of spray deposition can be used when making new types of polymer solar cells, for example, but also for nanostructured sensors or special-purpose inks used in relief printing.
The findings presented also offer interesting insights for industrial spray manufactured materials. Calvin Brett from the Royal Institute of Technology (KTH) in Stockholm explains: “In order to achieve faster drying times in industrial applications, the materials to be coated are usually heated. However, if doing so in itself alters the properties of the material that is applied, then this has a direct influence on the manufacturing process.”
Eva Malmström Jonsson, who was in charge of the experiments on behalf of KTH, emphasises the huge potential of further research at PETRA III: “By combining our areas of expertise, we have the means of gaining new insights into how colloidal particles behave on a surface and how their properties can be customised through careful chemical design.”