Glass from a 3D printer
ETH researchers used a 3D printing process to produce complex and highly porous glass objects. The basis for this is a special resin that can be cured with UV light.
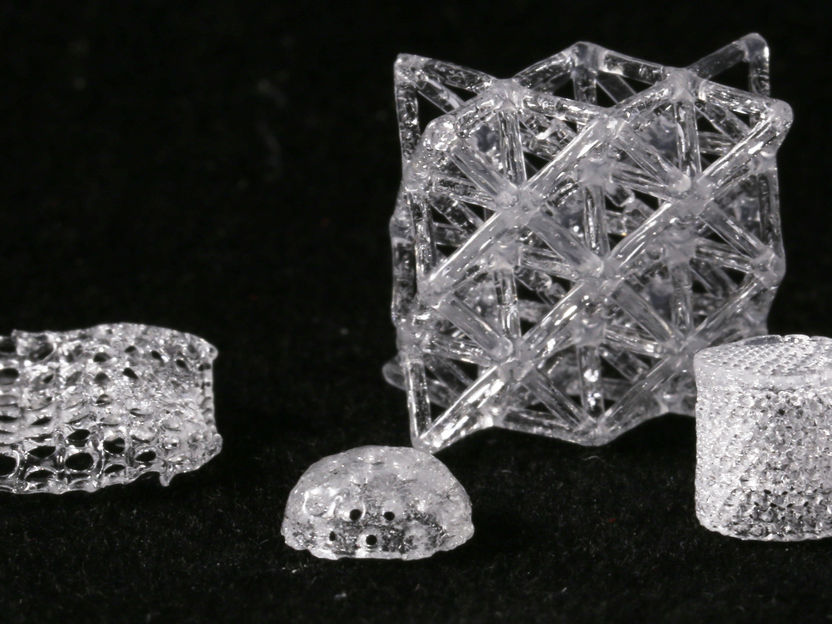
Various glass objects created with a 3D printer.
Group for Complex Materials / ETH Zurich
Producing glass objects using 3D printing is not easy. Only a few groups of researchers around the world have attempted to produce glass using additive methods. Some have made objects by printing molten glass, but the disadvantage is that this requires extremely high temperatures and heat-resistant equipment. Others have used powdered ceramic particles that can be printed at room temperature and then sintered later to create glass; however, objects produced in this way are not very complex.
Researchers from ETH Zurich have now used a new technique to produce complex glass objects with 3D printing. The method is based on stereolithography, one of the first 3D printing techniques developed during the 1980s. David Moore, Lorenzo Barbera, and Kunal Masania in the Complex Materials group led by ETH processor André Studart have developed a special resin that contains a plastic, and organic molecules to which glass precursors are bonded.
Light used to “grow” objects
The resin can be processed using commercially available Digital Light Processing technology. This involves irradiating the resin with UV light patterns. Wherever the light strikes the resin, it hardens because the light sensitive components of the polymer resin cross link at the exposed points. The plastic monomers combine to form a labyrinth-like structure, creating the polymer. The ceramic-bearing molecules fill the interstices of this labyrinth.
An object can thus be built up layer by layer. The researchers can change various parameters in each layer, including pore size: weak light intensity results in large pores; intense illumination produces small pores. “We discovered that by accident, but we can use this to directly influence the pore size of the printed object,” says Masania.
The researchers are also able to modify the microstructure, layer by layer, by mixing silica with borate or phosphate and adding it to the resin. Complex objects can be made from different types of glass, or even combined in the same object using the technique.
The researchers then fire the blank produced in this way at two different temperatures: at 600˚C to burn off the polymer framework and then at around 1000˚C to densify the ceramic structure into glass. During the firing process, the objects shrink significantly, but become transparent and hard like window glass.
Patent application submitted
These 3D-printed glass objects are still no bigger than a die. Large glass objects, such as bottles, drinking glasses or window panes, cannot be produced in this way – which was not actually the goal of the project, emphasises Masania.
The researchers have submitted a patent application for their discovery and already have one potential commercial partner interested in the technology: a supplier from the canton of Valais that provides glassware to many vineyards and wine cellars.
Original publication
Other news from the department science
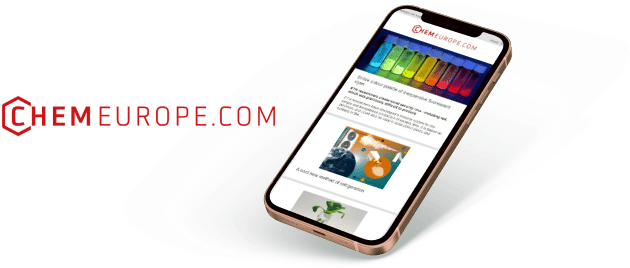
Get the chemical industry in your inbox
By submitting this form you agree that LUMITOS AG will send you the newsletter(s) selected above by email. Your data will not be passed on to third parties. Your data will be stored and processed in accordance with our data protection regulations. LUMITOS may contact you by email for the purpose of advertising or market and opinion surveys. You can revoke your consent at any time without giving reasons to LUMITOS AG, Ernst-Augustin-Str. 2, 12489 Berlin, Germany or by e-mail at revoke@lumitos.com with effect for the future. In addition, each email contains a link to unsubscribe from the corresponding newsletter.
Most read news
More news from our other portals
Last viewed contents
GE Plastics expands capacity with new European production location
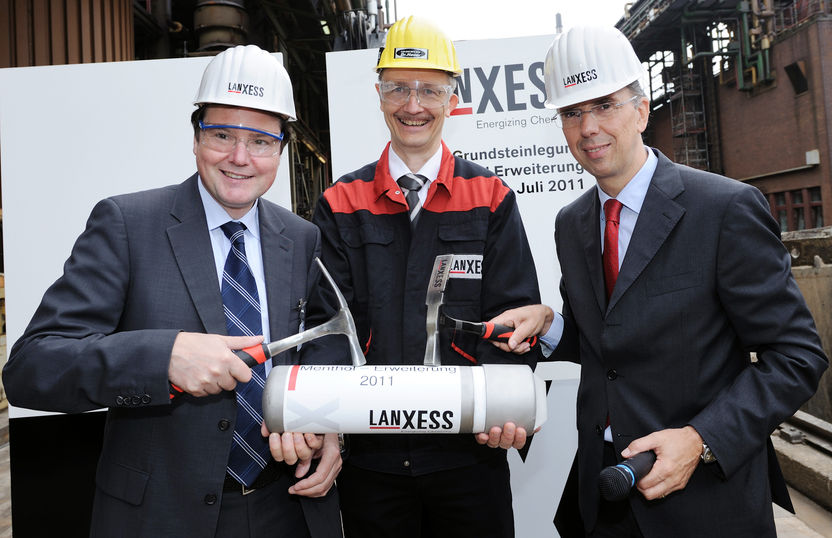
LANXESS to enlarge its menthol facility in Krefeld
50-state plan to transform US to renewable energy
Scientists have created a ceramic, resistant to extreme temperatures
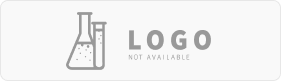