Chemists' surprising discovery of nanoconfined reactions could aid catalytic design
Georgia State University chemistry researchers have unlocked one of the mysteries of catalytic reactions on a microscopic scale, allowing for the design of more efficient industrial processes.
Catalysts -- which speed up chemical reactions in everything from the digestion of food to combustion engines in vehicles -- are essential in turning raw materials into useful products in industries, including petroleum, plastics, paper, pharmaceuticals and brewing. Understanding how reactions occur can help scientists engineer better catalysts that are more energy-saving and environmentally sustainable.
The researchers established a new imaging strategy that can track single molecules as they shimmy through tiny pores in the shells of silica spheres and monitor the chemical reaction dynamics on catalytic centers at the core, producing the first quantitative measurements of how confinement on a nano scale actually speeds up catalytic reactions.
Understanding this surprising "nanoconfinement effect" could help guide the precision design of more efficient industrial catalysts that can conserve energy.
"You want to make a specific product and you have the choice of different porous materials that can make different things. Which one will give you the best conversion rate and highest speed?" said Ning Fang, associate professor in Chemistry at Georgia State, who published the results of the research in Nature Communications. "Now we have a theory based on experimental evidence that we add to simulations to have a better prediction of what might be the result of using certain catalysts."
Study of catalytic reactions was previously limited to theoretical and computational models. The single-molecule imaging system, designed by Georgia State postdoctoral research associate Bin Dong and published in Nature Catalysis, allows researchers for the first time to see and measure the reactions occurring on a tiny multi-layered porous sphere created by collaborators at Iowa State University led by professor Wenyu Huang and postdoctoral research associate Yuchen Pei.
The reactant molecules have to orient themselves in a specific direction to fit through nanopores - openings that are roughly 100 times smaller than the width of a strand of hair. The nanopores are comparable in diameter to the size of the reactant molecule and when its tip reaches the active core, it immediately triggers the first step of the reaction upon contact. The generated intermediate product, however, is trapped by the nanopore as the reaction continues through three steps to form the final product molecule.
Contrary to conventional theory, this "nanoporous barrier" speeds up the reaction instead of slowing it down, based on Fang's experimental measurement of activation energy. Despite molecular movement being restricted by the presence of a porous shell, the process is actually magnified by the confinement, the study found.
"Instinctively, one would expect a decreasing activity when catalytic centers are shielded away from reactant molecules by a nanoporous shell," Fang said. "However, our experimental evidence tells a different story. And more surprisingly, the catalytic activities are further enhanced for catalysts with longer and narrower nanopore structures until the benefits of nanoconfinement are overtaken by the restrained molecular transport in the nanoporous shell."
This discovery could have major implications in the engineering of new catalysts. For example, the equivalent of more than 500 million barrels of gasoline is used every year to convert ethane and propane into alkenes that are used to make plastics, detergents and other products. Applying more efficient catalysts on a grand scale could save a lot of energy in the process.
Original publication
Other news from the department science
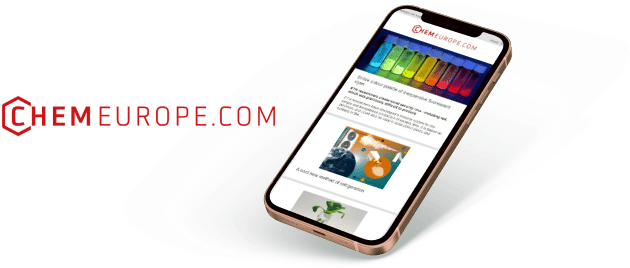
Get the chemical industry in your inbox
By submitting this form you agree that LUMITOS AG will send you the newsletter(s) selected above by email. Your data will not be passed on to third parties. Your data will be stored and processed in accordance with our data protection regulations. LUMITOS may contact you by email for the purpose of advertising or market and opinion surveys. You can revoke your consent at any time without giving reasons to LUMITOS AG, Ernst-Augustin-Str. 2, 12489 Berlin, Germany or by e-mail at revoke@lumitos.com with effect for the future. In addition, each email contains a link to unsubscribe from the corresponding newsletter.