Oil change due? Optimal date is to be determined during normal operation
If lubricants and hydraulic fluids in construction machines, airplanes or industrial installations are used too long, gears and other components can be heavily damaged. On the other hand, each oil change especially for large equipment is time consuming and expensive. Engineers at Saarland University and the new Center for Mechatronics and Automation (ZeMA) are developing a new method for determining the oil quality during normal operation. The measurement approach will indicate exactly when the oil should be changed. The development will be presented at the Hannover Industrial Trade Fair.
Today additives are used to make lubricants for gears or hydraulic fluids more durable. However, when the additives are worn out by aging processes, the oil quality will deteriorate rapidly. "Due to this fact the oil is changed very early to prevent damaging the expensive equipment in many applications", Andreas Schütze, Professor for measurement technology at Saarland University, says. His team is currently developing a measurement cell together with academic and industrial partners, which can be mounted directly in hydraulic systems. Using an infrared light source based on silicon micromachining the oil is screened. An infrared detector determines which wavelengths pass through the fluid. The more the oil is aged the more the detected light pattern is changed. "This allows indicating the optimal time for the next oil change. In addition, we can also determine if the system was contaminated by water", the engineer explains.
The measurement cell can currently be used up to a pressure of 100 bar. In the future this range will be expanded to address further applications, e.g. in airplane hydraulics. Also the method will be applied to other fluids like alcohol or glycol. "Today laboratory analytical techniques are used to determine the aging of fluids. We are trying to measure the wear during normal operation", Andreas Schütze says. This is especially important for closed hydraulic systems , e.g. in airplanes. But also application areas like automotive could benefit, if the cell can be produced cheaply in high volumes. "Considering the high oil volumes, e.g. in large hydraulic installations, optimized oil change intervals are not only much more cost effective. The environment will also benefit, by less waste of oil. So the total demand of oil can be reduced and the consumption of this expensive resource is more economic", Schütze explains.
The method is developed in close cooperation with the new Center for Mechatronics and Automation (ZeMA) in Saarbrücken. The primary goal of ZeMA is application oriented research and the transfer of new methods from academia to industrial application. ZeMA works together with Saarland University, the University of Applied Sciences (HTW) as well with partners from industry. ZeMA addresses challenging projects with the goal of improving the efficiency of industrial processes.
Most read news
Organizations
Other news from the department science
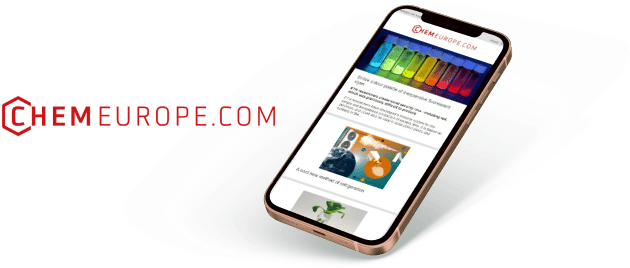
Get the chemical industry in your inbox
By submitting this form you agree that LUMITOS AG will send you the newsletter(s) selected above by email. Your data will not be passed on to third parties. Your data will be stored and processed in accordance with our data protection regulations. LUMITOS may contact you by email for the purpose of advertising or market and opinion surveys. You can revoke your consent at any time without giving reasons to LUMITOS AG, Ernst-Augustin-Str. 2, 12489 Berlin, Germany or by e-mail at revoke@lumitos.com with effect for the future. In addition, each email contains a link to unsubscribe from the corresponding newsletter.