High reaction rates even without precious metals
Precious metals are often efficient catalysts. But they are expensive and rare. However, it has so far been difficult to determine how efficient non-precious metal alternatives are.
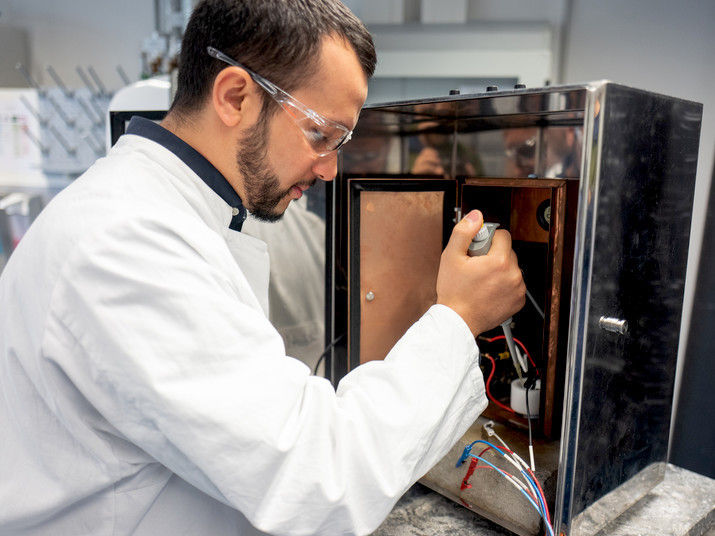
In this shielded cell, Abdelilah El Arrassi is testing the nanoparticles in electrochemical experiments.
© RUB, Kramer
Non-precious metal nanoparticles could one day replace expensive catalysts for hydrogen production. However, it is often difficult to determine what reaction rates they can achieve, especially when it comes to oxide particles. This is because the particles must be attached to the electrode using a binder and conductive additives, which distort the results. With the aid of electrochemical analyses of individual particles, researchers have now succeeded in determining the activity and substance conversion of nanocatalysts made from cobalt iron oxide – without any binders. The team led by Professor Kristina Tschulik from Ruhr-Universität Bochum reports together with colleagues from the University of Duisburg-Essen and from Dresden in the Journal of the American Chemical Society, published online on 30 May 2019.
“The development of non-precious metal catalysts plays a decisive role in realising the energy transition as only they are cheap and available in sufficient quantities to produce the required amounts of renewable fuels,” says Kristina Tschulik, a member of the Cluster of Excellence Ruhr Explores Solvation (Resolv). Hydrogen, a promising energy source, can thus be acquired by splitting water into hydrogen and oxygen. The limiting factor here has so far been the partial reaction in which oxygen is produced.
Better than reaction rates currently achieved in industry
How efficiently cobalt iron oxide particles are able to catalyse oxygen generation was investigated by the researchers in the current work. They analysed many individual particles one after the other. The chemists allowed a particle to catalyse oxygen generation on the surface of the electrode and measured the current flow from this, which provides information about the reaction rate. “We have measured current densities of several kiloamps per square metre,” says Tschulik. “This is above the reaction rates currently possible in industry.”
The team showed that, for particles smaller than ten nanometres, the current flow is dependent on the particle size – the smaller the catalyst particle, the smaller the current. The current is also limited by the oxygen that is produced in the reaction and that diffuses away from the particle surface.
Extremely stable despite high stress
Following the catalysis experiments, the chemists observed the catalyst particles under the transmission electron microscope. “Despite the high reaction rates, i.e. although the particles had created so much oxygen, they hardly changed,” summarises Tschulik. “The stability under extreme conditions is exceptional.”
The analysis approach used in the current work can also be transferred to other electrocatalysts. “It is essential to find out more about the activities of nanocatalysts in order to be able to efficiently further develop non-precious metal catalysts for the renewable energy technologies of tomorrow,” says the Bochum-based chemist. In order to analyse the effect of the particle size on the catalytic activity, it is important to synthesise nanoparticles with defined size. As part of the University Alliance Ruhr, the Bochum team cooperates closely with researchers from the University of Duisburg-Essen led by Professor Stephan Schulz, who produce the catalyst particles.
Original publication
Other news from the department science
These products might interest you
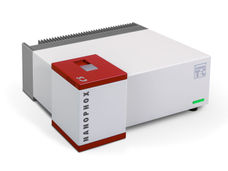
NANOPHOX CS by Sympatec
Particle size analysis in the nano range: Analyzing high concentrations with ease
Reliable results without time-consuming sample preparation
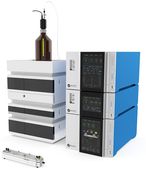
Eclipse by Wyatt Technology
FFF-MALS system for separation and characterization of macromolecules and nanoparticles
The latest and most innovative FFF system designed for highest usability, robustness and data quality
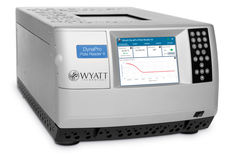
DynaPro Plate Reader III by Wyatt Technology
Screening of biopharmaceuticals and proteins with high-throughput dynamic light scattering (DLS)
Efficiently characterize your sample quality and stability from lead discovery to quality control
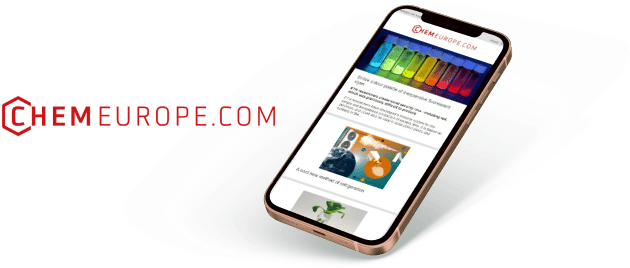
Get the chemical industry in your inbox
By submitting this form you agree that LUMITOS AG will send you the newsletter(s) selected above by email. Your data will not be passed on to third parties. Your data will be stored and processed in accordance with our data protection regulations. LUMITOS may contact you by email for the purpose of advertising or market and opinion surveys. You can revoke your consent at any time without giving reasons to LUMITOS AG, Ernst-Augustin-Str. 2, 12489 Berlin, Germany or by e-mail at revoke@lumitos.com with effect for the future. In addition, each email contains a link to unsubscribe from the corresponding newsletter.