Key component for batteries of the future
Fraunhofer IWS scientists headed by Dr. Holger Althues have developed an innovative process for the cost-efficient production of thin lithium anodes made of molten lithium. In the BMBF-funded “MaLiBa” project, the Dresden Institute is working with the companies hpulcas and SGS as well as with scientists led by Prof. Dr. Jürgen Janek of the Justus Liebig University in Giessen to solve further crucial issues relating to this concept. The most important innovation consists in realizing an anode compound. This contains a few micrometers thick nickel foil with lithium film stabilized by means of protective layers.
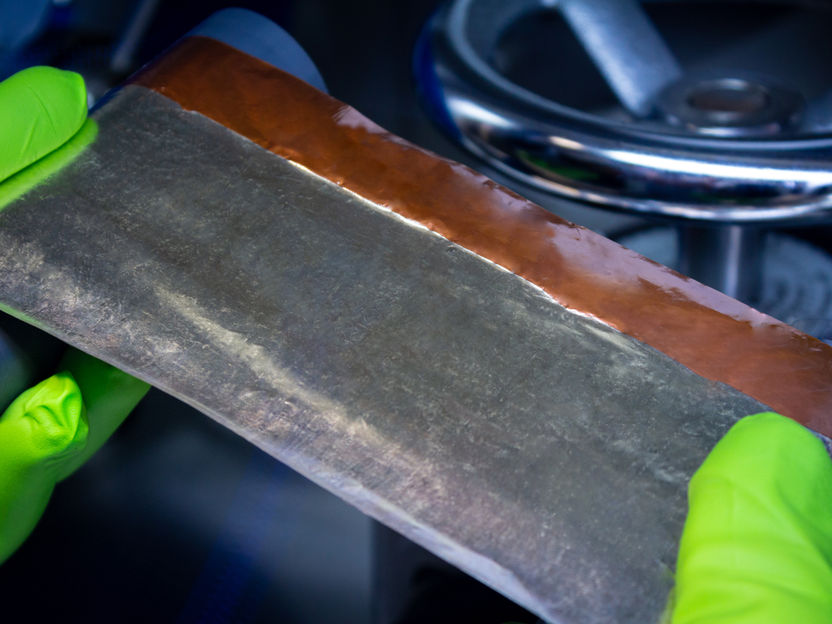
Lithium coating on copper foil created by IWS melt deposition: The process already permits producing prototype cells with lithium anode layers of 5 to 30 micrometers in thickness.
© Fraunhofer IWS Dresden
Lithium-metal anodes are regarded as key elements for battery systems of the future. They enable the energy density to be maximized both in terms of cell volume and mass. The lithium metal anode is already being used in lithium sulfur cells to achieve record specific energy values of more than 400 watt hours per kilogram. By comparison, the best lithium-ion battery cells currently only achieve 250 watt hours per kilogram. In addition, solid state batteries could exceed the volumetric energy density of today's lithium-ion batteries by more than 70 percent using the lithium metal anode. Conventional production solutions for lithium foils include rolling processes. Their disadvantage is the fact that the production of films with less than 50 micrometers over large areas is very challenging. The quality is also limited, as auxiliary materials or lubricants chemically contaminate the surface. Thus lithium foils cannot be produced on an industrial scale with the quality requirements necessary for battery applications. In addition, production technologies for high-quality and thin lithium coatings are not yet commercially available and the interface between lithium and other cell components is highly reactive. This in turn requires interface engineering to enable stable and safe use of the lithium anodes.
Lithiophilic current collector surface enables lithium melt wetting
For several years now, the Fraunhofer IWS has been working on a coating process that permits producing lithium films with just a few micrometers thickness. The most important innovation involves a lithiophilic surface that allows cost-effective and homogeneous deposition of molten lithium’s thin coatings on metallic substrates. “We are able to process thin nickel and copper foils in such a way that it becomes possible to coat them by liquid (molten) lithium,” explains Dr. Holger Althues, head of the Department of Chemical Surface and Battery Technology at Fraunhofer IWS. Since spheres form when liquid lithium is applied to an untreated copper or nickel foil, it is not possible to wet the foil surface with lithium. “However, this is absolutely necessary in order to create a coating, and we are able to achieve this with a lithiophilic substrate surface,” Dr. Althues concretizes. Further advantages include the fact that the developed IWS technology could be implemented at particularly low cost and could already be scaled up to industrial standards in the roll-to-roll process. Modifications of the lithium surface are intended in order to enhance this coating process within the “MaLiBa” project. The project team, coordinated by IWS, aims at significantly improving the handling, stability and safety of lithium anodes for use in battery cells. This research will be complemented by developing a laser cutting process within the “LiMeCut” project, which will enable flexible cutting of lithium anodes. The result will be a toolbox for adapting anodes to customer-specific cell systems and formats. “We see a growing demand in the development of lithium metal batteries,” explains battery researcher Dr. Althues. “Already today we can meet many requirements by fabricating tailor-made anodes.”
Other news from the department science
These products might interest you
Most read news
More news from our other portals
See the theme worlds for related content
Topic World Battery Technology
The topic world Battery Technology combines relevant knowledge in a unique way. Here you will find everything about suppliers and their products, webinars, white papers, catalogs and brochures.
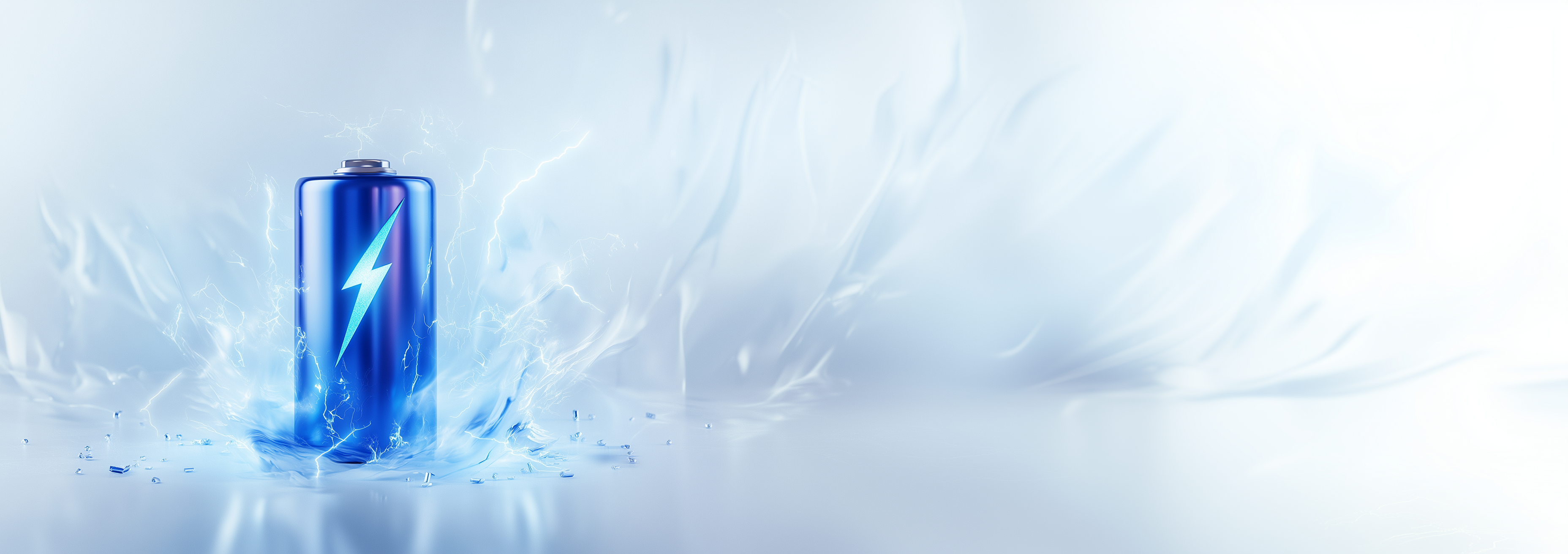
Topic World Battery Technology
The topic world Battery Technology combines relevant knowledge in a unique way. Here you will find everything about suppliers and their products, webinars, white papers, catalogs and brochures.