Hollow structures in 3D
Researchers succeed in printing channel structures in glass
quartz glass is the preferred material for applications that require long-term use because of its high chemical and mechanical stability and excellent optical properties. The engineer Prof. Dr. Bastian E. Rapp from the Department of Microsystems Engineering (IMTEK) at the University of Freiburg and his team have developed the Glassomer process, a method that enables scientists to shape glass like plastic. In the scientific journal “Nature Communication”, they recently presented a new application: They are now able to produce three-dimensional hollow structures in quartz glass.

Three-dimensional hollow structures in quartz glass.
AG Rapp
Glass is chemically very resistant, which is why cavities such as optical waveguides or microfluidic channels are difficult to produce in it, especially if they have to be three-dimensional. The Glassomer process developed by Rapp and his team simplified this process. Glassomer is a mixture in which high-purity silicon oxide is added in fine powder form to a liquid plastic. As long as this mixture is liquid, it can be processed like a plastic. When exposed to light, it hardens so that it can, for example, be drilled or milled. During the final heat treatment step in the process, the plastic is decomposed leaving leaving a dense glass component. Until now, channel structures could not be manufactures because the researchers had to remove the liquid material from the cavities which is not possible for long channels.
The Freiburg scientists are therefore taking a different approach by first creating the desired cavity as a polymeric component in the 3D printer: A later channel is printed as a polymer thread and then encapsulated with Glassomer. The finished printed product is then heated to 1,300 degrees Celsius so that the plastic - including the polymer thread – is decomposed. The result is a channel surrounded by real glass.
Original publication
Other news from the department science
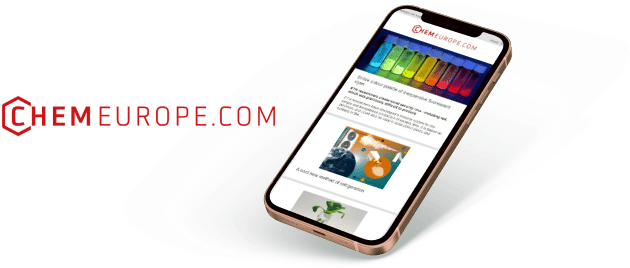
Get the chemical industry in your inbox
By submitting this form you agree that LUMITOS AG will send you the newsletter(s) selected above by email. Your data will not be passed on to third parties. Your data will be stored and processed in accordance with our data protection regulations. LUMITOS may contact you by email for the purpose of advertising or market and opinion surveys. You can revoke your consent at any time without giving reasons to LUMITOS AG, Ernst-Augustin-Str. 2, 12489 Berlin, Germany or by e-mail at revoke@lumitos.com with effect for the future. In addition, each email contains a link to unsubscribe from the corresponding newsletter.