For graphite pellets, just add elbow grease
It's easy and economical to make shiny pellets of Graphite from functionalized graphene, according to scientists at Rice University.
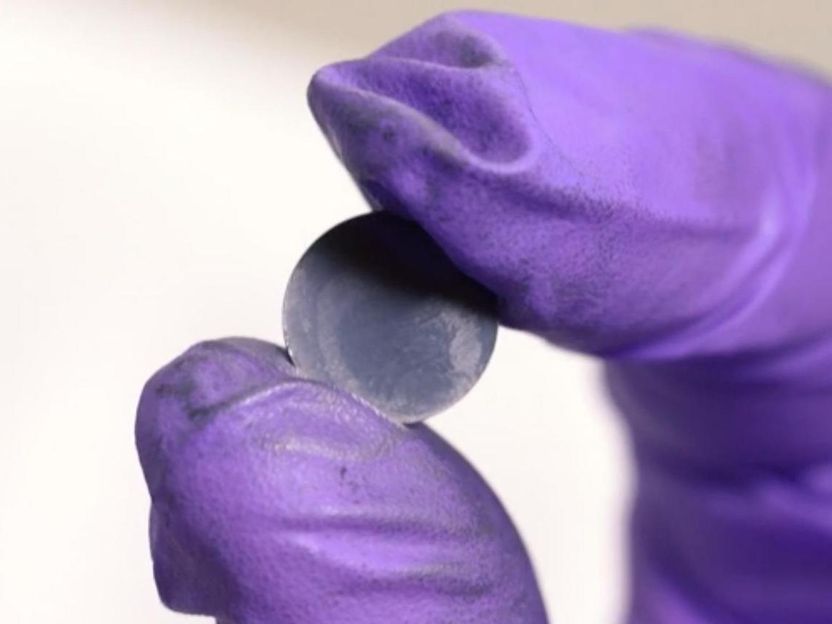
A graphite pellet made by hand from crushed graphene powder. The strong, light pellets developed at Rice University hold promise for electronic and catalytic applications.
Rice University
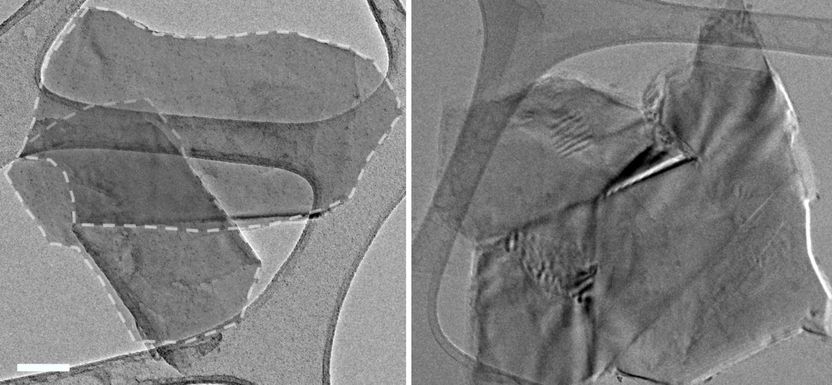
Scanning electron microscope images show graphene flakes before compression, at left, with individual flakes outlined, and well-connected graphene sheets after compression at right. Scale bar is 20 nanometers.
Ajayan Research Group/Rice University
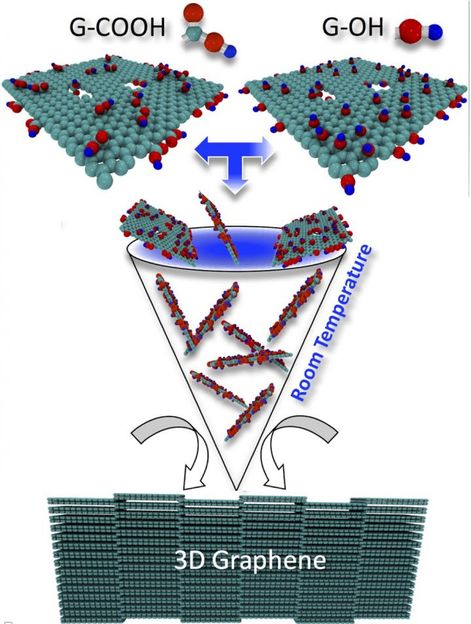
Researchers at Rice University consolidated functionalized graphene at room temperature by first crushing graphene powder and then pressing it into pellets. Chemically altering the graphene powder with carbon, oxygen and hydrogen provided a way to bind the graphene into a three-dimensional solid under pressure.
Ajayan Research Group/Rice University
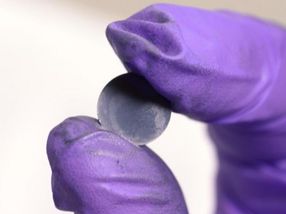
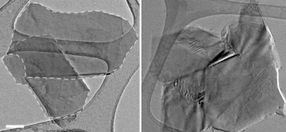
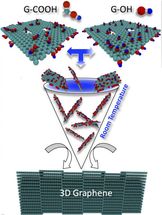
A report shows how chemically altered graphene powder can be pressed into a lightweight, semiporous solid that retains many of the strong and conductive qualities of graphite, the form of carbon found in pencils, lubricants and many other products that normally requires high-temperature processing to make.
Mohamad Kabbani, a former graduate student of Rice materials scientist Pulickel Ajayan and lead author of the paper, demonstrated the environmentally friendly, scalable process can be done in minutes by hand by grinding chemically modified graphene into a powder and using a hand-powered press to squeeze the powder into a solid pellet.
Kabbani previously showed how carbon nanotubes could be turned into graphene with a mortar and pestle rather than harsh chemicals. This time, he and his colleagues demonstrated how to make a battery-sized pellet, but the graphene powders with chemical functionalities attached to it can be pressed into any form. Kabbani said the material could be suitable for structural, catalytic, electrochemical and electronic applications.
"This is the first time anyone's made these at room temperature and without very high pressure," he said. "Usually these kind of materials require sintering (a process that uses pressure or heat to form solids without melting them) at temperatures above 1,000 degrees Celsius to produce strong pellets. In this case, mechano-chemistry at the nanoscale saved us a lot of energy and money."
The process began with two sets of functionalized nanotubes, one with carboxylic acid and the other with hydroxyl molecules. Once crushed to combine them either by hand or machine, they are placed in a lab-scale hydraulic press and subjected to 5 tons of pressure. The functional groups cross-linked the graphene sheets to each other, and even though no liquids were involved, they produced a tiny amount of water as a byproduct of the reaction, Kabbani said.
The pellets remained stable when placed in hot water for five hours, even when stirred; this confirmed the interlocking of the graphene sheets within, the researchers reported.
The combination of light weight, high strength and high conductivity is appealing for applications such as conducting cables and electrodes, Kabbani said. "The pellet material is stronger and lighter than commercial graphite electrodes and could be promising for electrical storage applications with high energy and power densities," he said.
Original publication
Mohamad A. Kabbani, Vidya Kochat, Sanjit Bhowmick, Matias Soto, Anirban Som, K.R. Krishnadas, Cristiano F. Woellner, Ygor M. Jaques, Enrique V. Barrera, Syed Asif, Robert Vajtai, Thalappil Pradeep, Douglas S. Galvão, Ahmad T. Kabbani, Chandra Sekhar Tiwary, Pulickel M. Ajayan; "Consolidation of functionalized graphene at ambient temperature via mechano-chemistry"; Carbon; 2018