SEPC successfully starts up new petrochemical complex
Saudi Ethylene and polyethylene Company (SEPC) has successfully started up its Petrochemical Complex in Al-Jubail Industrial City, located in the Kingdom of Saudi Arabia. SEPC, formed in 2006, is a joint venture owned by LyondellBasell Industries (25%) and Tasnee and Sahara Petrochemical Company (75%).
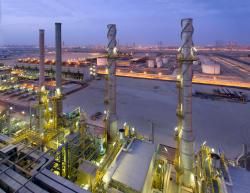
Saudi Ethylene and Polyethylene Company (SEPC) has successfully started up its Petrochemical Complex in Al-Jubail Industrial City, located in the Kingdom of Saudi Arabia.
LyondellBasell Industries
The complex includes facilities that produce:
- 400 KT per year of high density, mulitmodal polyethylene based on LyondellBasell’s latest-generation Hostalen ACP process
- 400K KT per year of low density polyethylene based on LyondellBasell’s Lupotech T technology
- 1000 KT per year of ethylene
- 285 KT per year of propylene
“Through the combined strengths of both partners, we’ve created a world-class manufacturing complex with highly competitive feedstock and operating costs in close proximity to our target markets,” said Saleh Al-Nazha, President of SEPC. “By using the most advanced PE technologies available in the market, we can manufacture specialty and high-performance products but within a cost structure that can take into account the financial pressures and cyclicality of a commodity market.”
“This complex is an important part of our strategy to grow and diversify our feedstock base, which will help us to meet the needs of our customers in Europe, Asia and the Middle East region,” explained Manuel Fraga, LyondellBasell’s Divisional Vice President for Operations in the Africa and Middle East Region.
The Hostalen ACP unit for multimodal HDPE addresses customer needs that are beyond the limits of standard bi-modal HDPE, producing resins with an advanced toughness/stiffness balance, superior impact resistance, higher stress crack resistance and significantly improved processing advantages. The process enables producers to create resins that meet demanding requirements for major HDPE applications ranging from thin-wall packaging to crack-resistant pipe.
The LDPE plant is based on the leading high-pressure tubular reactor process, Lupotech T. The technology offers attractive economics and world-scale capabilities, and has become the benchmark in LDPE manufacturing by providing the lowest operating costs currently in the market, while producing high-performance resins. Additional features of Lupotech T technology include fast start up and grade changes, as well as a high on-stream factor, making it today’s technology of choice for the production of LDPE and EVA copolymers.
Other news from the department manufacturing
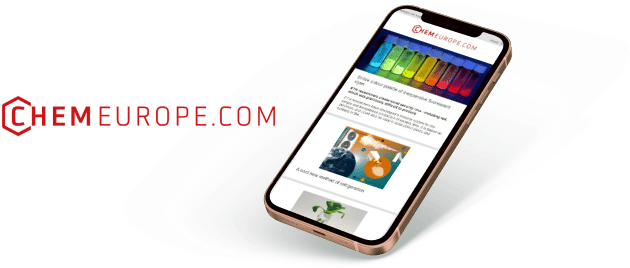
Get the chemical industry in your inbox
By submitting this form you agree that LUMITOS AG will send you the newsletter(s) selected above by email. Your data will not be passed on to third parties. Your data will be stored and processed in accordance with our data protection regulations. LUMITOS may contact you by email for the purpose of advertising or market and opinion surveys. You can revoke your consent at any time without giving reasons to LUMITOS AG, Ernst-Augustin-Str. 2, 12489 Berlin, Germany or by e-mail at revoke@lumitos.com with effect for the future. In addition, each email contains a link to unsubscribe from the corresponding newsletter.